Metal 3D Printing Market – Global Industry Size, Share, Trends, Opportunity, and Forecast, By Product (Titanium, Nickel), By Form (Filament, Powder), By Application (Aerospace & Defense, Medical & Dental, Others), By Region, and By Competition Forecast 2018-2028
Published Date: November - 2024 | Publisher: MIR | No of Pages: 320 | Industry: ICT | Format: Report available in PDF / Excel Format
View Details Buy Now 2890 Download Sample Ask for Discount Request CustomizationForecast Period | 2024-2028 |
Market Size (2022) | USD 6.03 Billion |
CAGR (2023-2028) | 25.82% |
Fastest Growing Segment | Filament |
Largest Market | North America |
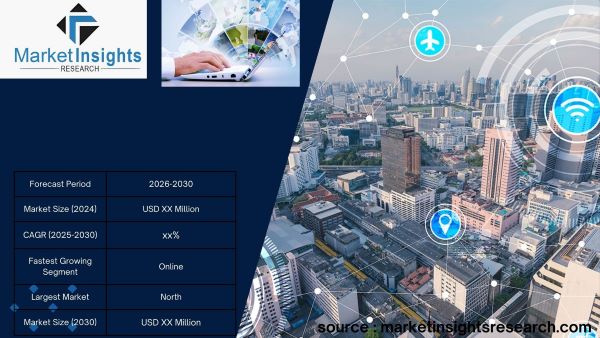
Market Overview
The global Metal 3D Printing market has emerged as a transformative force across various industries, redefining the way manufacturers conceptualize, design, and produce metal components. Leveraging the power of additive manufacturing, Metal 3D Printing has unlocked new frontiers in precision engineering, enabling the creation of complex geometries and high-performance parts with unmatched efficiency. This market, characterized by continuous innovation and technological advancements, has witnessed remarkable growth in recent years.
Technological AdvancementsMetal 3D Printing has evolved significantly in terms of technology and materials. Innovations in printing techniques, including powder bed fusion and directed energy deposition, have expanded the range of printable metals, offering solutions that cater to diverse industry needs. Titanium, aluminum, stainless steel, and nickel-based alloys are among the metals increasingly used in Metal 3D Printing.
Diverse Industry ApplicationsThe versatility of Metal 3D Printing has paved the way for applications in aerospace, automotive, healthcare, defense, and more. In aerospace, it has revolutionized the production of lightweight, complex components. The automotive sector harnesses it for rapid prototyping and custom part manufacturing. Healthcare benefits from patient-specific implants and prosthetics.
Supply Chain OptimizationMetal 3D Printing has disrupted traditional supply chains. It enables on-demand production, reducing inventory costs and eliminating the need for large warehouses. Companies can print components as needed, reducing waste and mitigating supply chain risks.
Customization and Design FreedomOne of the key strengths of Metal 3D Printing is its ability to offer customization and design freedom. This has profound implications for industries where unique, specialized parts are essential, such as medical implants and aerospace components.
Sustainability and Material EfficiencyAs sustainability gains importance, Metal 3D Printing aligns with eco-friendly manufacturing practices. The technology minimizes material wastage, optimizing resource utilization. This is particularly relevant in industries aiming to reduce their environmental footprint.
Challenges and CompetitionChallenges persist, including high initial costs, limitations in scaling production for mass markets, and the need for skilled operators. The market is also highly competitive, with numerous companies vying to innovate and expand their product portfolios.
Future OutlookThe Metal 3D Printing market is poised for continuous growth. Advances in materials, increased adoption across industries, and a growing ecosystem of service providers contribute to a promising future. The market will play a pivotal role in shaping the manufacturing landscape, driving efficiency, sustainability, and innovation across sectors.
Key Market Drivers
Growing Demand for Complex and Lightweight Components
The global Metal 3D Printing market is being driven by the increasing demand for complex and lightweight components in various industries, including aerospace, automotive, and healthcare. Traditional manufacturing methods often struggle to produce intricate geometries and structures without multiple assembly steps. Metal 3D Printing enables the creation of parts with complex internal features, reducing the need for assembly and improving overall performance.
In aerospace, for example, the ability to design lightweight and aerodynamic components is crucial for fuel efficiency. Metal 3D Printing allows for the production of aircraft parts that are not only lighter but also stronger and more reliable. This demand for lightweight, high-performance components is a significant driver for the adoption of Metal 3D Printing technology.
Advancements in Metal Powder Development
The quality and availability of metal powders play a critical role in Metal 3D Printing. Recent advancements in metal powder development have expanded the range of materials that can be used in 3D printing processes. Traditionally, materials like titanium, aluminum, and stainless steel dominated the market, but today, there is a broader selection of alloys and metals found at.
Innovations in metal powder production techniques have led to improved powder consistency and quality, making Metal 3D Printing more reliable and predictable. This, in turn, has opened up new applications and industries for metal additive manufacturing.
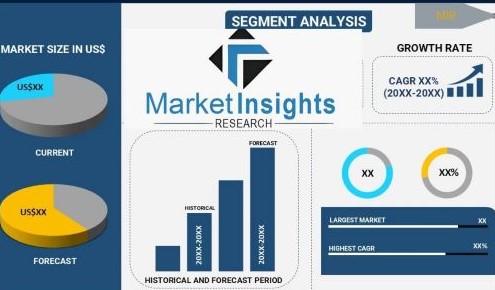
Industry 4.0 and Digital Transformation
The global manufacturing landscape is undergoing a significant transformation through Industry 4.0 and digitalization. Metal 3D Printing is a key enabler of this transformation, as it aligns perfectly with the principles of smart manufacturing, automation, and digitalization.
Manufacturers are increasingly adopting digital twin technologies, which involve creating digital replicas of physical products and processes. Metal 3D Printing plays a vital role in the creation of these digital twins, allowing for rapid prototyping, product customization, and the efficient optimization of designs. As industries embrace digital transformation, the demand for Metal 3D Printing as a core technology continues to rise.
The healthcare sector represents a significant driver for the global Metal 3D Printing market. The ability to produce patient-specific implants and medical devices has revolutionized healthcare practices. Metal 3D Printing is widely used in the production of orthopedic implants, dental prosthetics, and customized surgical instruments.
The aging global population, coupled with a rising demand for personalized healthcare solutions, is fueling the adoption of Metal 3D Printing in the medical field. It allows for the creation of implants that precisely match a patient's anatomy, resulting in better outcomes and reduced recovery times. This growing healthcare market presents a lucrative opportunity for Metal 3D Printing manufacturers.
Sustainability and Reduced Material Waste
Sustainability is a driving force in many industries today, and Metal 3D Printing aligns well with this trend. Traditional manufacturing processes often generate significant material waste, whereas 3D printing can significantly reduce material usage. Metal 3D Printing is an additive manufacturing process, meaning it adds material layer by layer, only using what is necessary to build the desired part.
Reduced material waste not only contributes to sustainability efforts but also leads to cost savings for manufacturers. As environmental concerns continue to grow and regulations on material waste become stricter, Metal 3D Printing's sustainability advantages become more compelling.
Key Market Challenges
High Material and Equipment Costs
One of the primary challenges facing the global Metal 3D Printing market is the high cost associated with both materials and equipment. Metal powders used in 3D printing are often expensive, and the cost can vary significantly depending on the type of metal being used. For example, titanium and nickel-based alloys are costly materials. Additionally, the specialized equipment required for Metal 3D Printing, such as selective laser melting (SLM) or electron beam melting (EBM) machines, can come with a hefty price tag. These high costs can be a barrier to entry for smaller manufacturers and limit the adoption of Metal 3D Printing in various industries.
To address this challenge, manufacturers and researchers are working on cost-effective alternatives, including the development of more affordable metal powders and the design of lower-cost 3D printers. However, achieving cost parity with traditional manufacturing methods remains a significant hurdle.
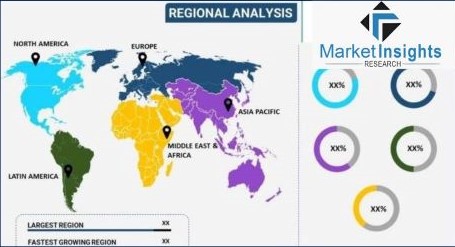
Limited Material Options and Quality Assurance
While Metal 3D Printing offers the advantage of creating complex geometries, there are limitations when it comes to material options and quality assurance. Not all metals are readily found at in powder form suitable for 3D printing. This limits the range of alloys and materials that can be used for specific applications. Moreover, ensuring the quality and consistency of printed metal parts can be challenging. Variations in material properties and printing parameters can lead to defects and inconsistencies in parts, affecting their performance and reliability.
Quality control and assurance are paramount in industries such as aerospace and healthcare, where safety and precision are critical. Addressing this challenge involves developing stricter quality standards, improving in-situ monitoring and inspection techniques, and enhancing post-processing methods to achieve the desired material properties consistently.
Post-Processing and Surface Finish
Post-processing remains a significant challenge in Metal 3D Printing. While 3D printing can create intricate geometries, the resulting parts often require extensive post-processing to achieve the desired surface finish, dimensional accuracy, and mechanical properties. This can involve heat treatment, machining, surface coating, and other techniques, which add time and cost to the production process.
Efforts are underway to develop more efficient and automated post-processing solutions that reduce the need for manual labor and shorten lead times. Innovations in post-processing technologies will be crucial to making Metal 3D Printing more competitive with traditional manufacturing methods.
Regulatory and Certification Hurdles
In industries like aerospace, healthcare, and automotive, products are subject to strict regulatory and certification requirements to ensure safety and reliability. Metal 3D Printing faces challenges in meeting these standards, especially when it comes to validating the quality and performance of printed parts. Obtaining the necessary certifications for 3D-printed components can be a lengthy and complex process.
To overcome this challenge, industry stakeholders, regulatory bodies, and certification organizations must work collaboratively to establish clear guidelines and standards for Metal 3D Printing. This will provide a more predictable and streamlined path to certification, encouraging broader adoption in safety-critical applications.
Intellectual Property and Security Concerns
With the rise of Metal 3D Printing, intellectual property (IP) and security concerns have become increasingly relevant. The digital nature of 3D printing files makes them susceptible to unauthorized copying and distribution. This raises concerns about the protection of proprietary designs and the potential for counterfeit parts to enter the market.
Addressing these challenges requires the development of robust digital rights management (DRM) solutions, secure supply chain practices, and legal frameworks to protect IP in the context of 3D printing. As the industry matures, stakeholders must collaborate to establish standards and best practices for IP protection.
Key Market Trends
Expanding Applications and Materials Diversity
The global Metal 3D Printing market is experiencing a significant trend in expanding applications and materials diversity. Traditionally dominated by aerospace and medical sectors, Metal 3D Printing is now finding utility in various industries. This diversification of applications includes automotive, energy, jewelry, and even consumer products. As a result, manufacturers are increasingly developing new metal alloys suitable for 3D printing, enabling the creation of complex, high-performance components. The ability to print with metals like titanium, nickel alloys, and aluminum is driving innovation across industries, unlocking novel designs and improved product performance.
Advancements in Process Technologies
Another notable trend is the continuous advancement in Metal 3D Printing process technologies. Traditional techniques like powder bed fusion (PBF) and directed energy deposition (DED) have seen improvements in speed, precision, and affordability. PBF processes, including selective laser melting (SLM) and electron beam melting (EBM), are becoming more accessible to a broader range of manufacturers. Additionally, newer technologies, such as binder jetting, are gaining traction due to their ability to print at high speeds while maintaining accuracy. These advancements are driving the adoption of Metal 3D Printing across industries by making it more cost-effective and scalable.
Enhanced Post-Processing and Quality Control
As Metal 3D Printing becomes more mainstream, there's a growing focus on post-processing and quality control. Manufacturers are investing in solutions to improve the surface finish, mechanical properties, and overall quality of printed parts. Innovations in post-processing techniques, such as heat treatment, machining, and surface coatings, are vital for achieving the required surface finish and part integrity. Additionally, the development of in-situ monitoring and inspection technologies is helping ensure that printed metal parts meet stringent quality standards. These advancements address concerns about the reliability and consistency of Metal 3D Printing and encourage its adoption in critical applications.
Sustainability and Circular Economy
Sustainability is a prominent trend in the global Metal 3D Printing market. Metal Additive Manufacturing allows for the creation of parts with minimal waste, reducing material consumption compared to traditional manufacturing methods. This aligns with the broader push for a circular economy, where materials are reused and recycled to minimize environmental impact. Metal 3D Printing's potential for on-demand production and localized manufacturing also contributes to sustainability efforts by reducing transportation emissions associated with global supply chains. As sustainability becomes a more significant concern for businesses and consumers, Metal 3D Printing's eco-friendly attributes are likely to drive its adoption further.
Industry 4.0 Integration
Integration with Industry 4.0 technologies is a transformative trend in the Metal 3D Printing market. The combination of Metal 3D Printing with IoT (Internet of Things) devices, artificial intelligence (AI), and data analytics allows for smart, data-driven manufacturing processes. This integration facilitates real-time monitoring of 3D printers, predictive maintenance, and the ability to optimize print parameters based on data analysis. It also enables seamless connectivity with other digital tools, such as computer-aided design (CAD) and product lifecycle management (PLM) systems, streamlining the entire product development process. Industry 4.0 integration enhances efficiency, quality control, and customization capabilities, positioning Metal 3D Printing as a key enabler of the smart factory of the future.
Segmental Insights
Product Insights
Titanium segment
The aerospace and defense sectors have been early adopters of Metal 3D Printing technology, and titanium's dominance aligns with their stringent requirements. The industry relies on lightweight yet durable components for aircraft and spacecraft, and titanium's unique properties make it an ideal choice. Companies like Boeing and Airbus have employed titanium Metal 3D Printing to create complex structural components, leading to significant weight reduction and fuel savings.
In the healthcare sector, titanium's biocompatibility and corrosion resistance have led to its extensive use in the production of medical implants and devices. From custom implants tailored to a patient's anatomy to dental prosthetics and surgical instruments, Metal 3D Printing with titanium has revolutionized healthcare by enabling the creation of patient-specific solutions.
Form Insights
Powder segment
Metal 3D Printing using powder feedstock has found widespread adoption across numerous industries. The aerospace sector employs it to create complex, lightweight components, while the healthcare industry leverages it for producing customized implants and medical devices. The automotive sector also utilizes metal powder for lightweighting and improving vehicle performance.
The powder bed fusion (PBF) technique is one of the most prevalent Metal 3D Printing methods, with several variants such as selective laser melting (SLM) and electron beam melting (EBM). In these processes, a bed of metal powder is selectively melted by a laser or electron beam to build up complex 3D structures layer by layer. PBF offers a high degree of precision and is known for producing parts with excellent mechanical properties.
Regional Insights
North America
North America is home to some of the world's largest aerospace and defense companies, and this sector has been an early adopter of Metal 3D Printing technology. The aerospace industry requires lightweight yet durable components, which Metal 3D Printing can deliver. Companies like Boeing and Lockheed Martin have embraced Metal 3D Printing for prototyping, production, and repairs, driving the technology's growth in the region.
The healthcare industry in North America has rapidly adopted Metal 3D Printing for various applications, including the production of patient-specific implants, medical devices, and dental prosthetics. The demand for personalized healthcare solutions and the region's strong medical research and development ecosystem have contributed to Metal 3D Printing's expansion in this sector.
North America benefits from a regulatory environment that encourages innovation while ensuring safety and quality standards. Regulatory agencies, such as the FDA in the United States, have developed clear guidelines for additive manufacturing in healthcare, giving companies the confidence to invest in Metal 3D Printing for medical applications.
Recent Developments
- In November 2019, Renishawplc collaborated with Sandvik Additive Manufacturing to qualify new additivemanufacturing (AM) materials for production applications. These materialsinclude a range of metal powders and new alloy compositions that can beoptimized for the laser powder bed fusion (LPBF) process and superior materialproperties. With this collaboration, Renishaw plc developed new metal materialsfor 3D printing.
- In October 2019, GEAdditive entered into a five-year cooperative research and developmentagreement (CRADA) with the US Department of Energy’s Oak Ridge NationalLaboratory (ORNL). The agreement was focused on the processes, materials, andsoftware to increase customer adaptability towards additive manufacturing fromconventional manufacturing.
Key Market Players
- 3D Systems, Inc.
- Arcam AB
- GE Additive Manufacturing
- Hewlett-Packard
- Markforged, Inc.
- Renishaw plc
- SLM Solutions Group AG
- Stratasys Ltd.
- TRUMPF GmbH + Co. KG
- Velo3D, Inc.
By Product | By Form | By Application | By Region |
|
|
|
|
Related Reports
- Multimodal AI Market Size - By Component (Solution, Service), By Technology (Machine Learning, Natural Language Processi...
- AVOD Market Size - By Content (Movies, TV Shows, Original Series, News, Sports, User-generated Content), By Platform (S...
- Premium Finance Market - By Type (Life Insurance, Non-life Insurance), By Interest Rate (Fixed Interest Rate, Floating I...
- Gift Cards Market - By Type (Closed-loop Gift Cards, Open-loop Gift Cards), By Distribution Channel (Online, Offline), B...
- Biometric Payment Market Size - By Biometric Mode (Fingerprint Recognition, Facial Recognition, Voice Recognition, Iris ...
- QR Codes Payment Market Size - By Offerings (Solution [Static QR Code {Merchant-presented QR Code, Customer-presented QR...
Table of Content
To get a detailed Table of content/ Table of Figures/ Methodology Please contact our sales person at ( chris@marketinsightsresearch.com )
List Tables Figures
To get a detailed Table of content/ Table of Figures/ Methodology Please contact our sales person at ( chris@marketinsightsresearch.com )
FAQ'S
For a single, multi and corporate client license, the report will be available in PDF format. Sample report would be given you in excel format. For more questions please contact:
Within 24 to 48 hrs.
You can contact Sales team (sales@marketinsightsresearch.com) and they will direct you on email
You can order a report by selecting payment methods, which is bank wire or online payment through any Debit/Credit card, Razor pay or PayPal.
Discounts are available.
Hard Copy