Precision Engineering Machines Market – Global Industry Size, Share, Trends, Opportunity, and Forecast Segmented By Type (CNC Machine Tools, EDM Machine Tools, Others), By End-use (Automotive, Non-Automotive), Region, By Competition, 2018-2028
Published Date: November - 2024 | Publisher: MIR | No of Pages: 320 | Industry: ICT | Format: Report available in PDF / Excel Format
View Details Buy Now 2890 Download Sample Ask for Discount Request CustomizationForecast Period | 2024-2028 |
Market Size (2022) | USD 13.02 billion |
CAGR (2023-2028) | 6.98% |
Fastest Growing Segment | CNC Machine Tools |
Largest Market | Asia Pacific |
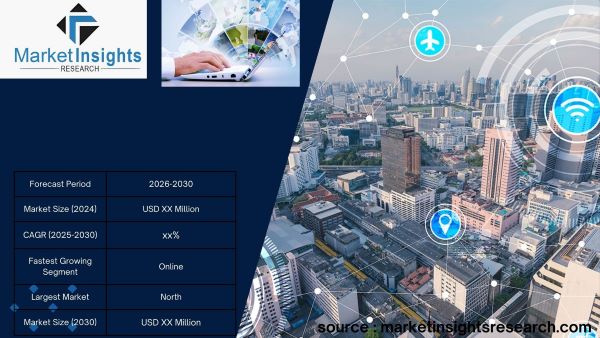
Market Overview
Global Precision Engineering Machines Market has experienced tremendous growth in recent years and is poised to continue its strong expansion. The Precision Engineering Machines Market reached a value of USD 13.02 billion in 2022 and is projected to maintain a compound annual growth rate of 6.98% through 2028.
Key Market Drivers
Increasing Demand for High-Precision Manufacturing
The global Precision Engineering Machines market is experiencing a significant surge in demand, primarily driven by the increasing need for high-precision manufacturing across various industries. This escalating demand is reshaping the landscape of manufacturing processes and revolutionizing the way products are designed, developed, and produced.
One of the primary drivers behind this trend is the relentless pursuit of precision and accuracy in manufacturing. In industries such as aerospace, automotive, electronics, medical devices, and defense, where components must meet stringent quality standards, the demand for precision engineering machines has reached unprecedented levels. These machines encompass a wide range of equipment, including CNC (Computer Numerical Control) machining centers, grinding machines, and EDM (Electrical Discharge Machining) systems, among others, each designed to achieve a specific level of precision.
The automotive industry, for instance, relies heavily on precision engineering machines to manufacture critical components like engine parts and transmission gears. The demand for vehicles with higher fuel efficiency and reduced emissions has necessitated the production of precise components, which can only be achieved through the use of advanced machining tools and equipment.
Similarly, in the medical device industry, precision engineering machines are instrumental in creating intricate and miniature components for medical implants, surgical instruments, and diagnostic devices. These machines enable manufacturers to meet strict tolerances and ensure the safety and effectiveness of medical products, ultimately improving patient outcomes.
The electronics sector is another major beneficiary of precision engineering machines. The trend toward miniaturization and the demand for smaller, more powerful electronic devices have pushed manufacturers to adopt high-precision machining processes. Microelectronics, semiconductors, and printed circuit boards all require precision engineering to create the tiny components and connections essential for modern electronics.
Aerospace and defense industries are no strangers to the demand for precision. Aircraft and spacecraft components must be manufactured to exacting standards to ensure safety and performance. Precision engineering machines enable the creation of intricate parts, such as turbine blades, with high levels of accuracy, contributing to the reliability and efficiency of aerospace systems.
Furthermore, the global trend towards Industry 4.0 and smart manufacturing is amplifying the demand for precision engineering machines. These machines are often integrated into digitally connected production lines, allowing for real-time monitoring and adjustments. This level of automation and control not only enhances precision but also improves efficiency and reduces waste, further underscoring their importance in modern manufacturing.
The increasing complexity of product designs is yet another factor fueling demand. As products become more intricate and incorporate advanced materials, traditional manufacturing methods struggle to meet the precision requirements. Precision engineering machines excel in handling complex geometries and materials, making them indispensable for industries that push the boundaries of innovation.
In conclusion, the surging demand for high-precision manufacturing is the driving force behind the global Precision Engineering Machines market. Industries across the board, including automotive, medical devices, electronics, aerospace, and defense, are recognizing the pivotal role these machines play in achieving the levels of precision and quality demanded by today's market. As technological advancements continue to push the boundaries of what is possible, the demand for precision engineering machines is expected to persist and even accelerate, shaping the future of manufacturing in an increasingly interconnected and complex world.
Technological Advancements and Industry 4.0 Integration
The Global Precision Engineering Machines Market is experiencing a profound transformation, primarily propelled by technological advancements and the seamless integration of Industry 4.0 principles. This convergence of cutting-edge technology and manufacturing processes is revolutionizing the precision engineering landscape and reshaping industries across the board.
At the heart of this transformation are technological advancements that encompass various facets of precision engineering machines. These innovations span multiple areas
Enhanced AutomationAutomation has emerged as a defining feature of modern precision engineering machines. Advancements in robotics, machine vision, and artificial intelligence (AI) have enabled machines to perform complex tasks with minimal human intervention. This not only improves productivity but also ensures consistent precision in manufacturing.
Advanced Materials ProcessingThe development of high-performance materials, including composites, ceramics, and exotic alloys, has necessitated precision engineering machines capable of working with these materials. Cutting tools and machining processes have evolved to cater to the unique challenges posed by these materials, enabling the production of components with exceptional strength and durability.
Nanotechnology IntegrationThe integration of nanotechnology into precision engineering machines has opened up new frontiers in miniaturization and precision. Machines equipped with nanoscale positioning systems and measurement tools can manufacture components with submicron accuracy, paving the way for advancements in electronics, medical devices, and materials science.
Additive Manufacturing (3D Printing)Additive manufacturing technologies, often referred to as 3D printing, have gained prominence in precision engineering. These technologies allow for the creation of intricate and highly customized components layer by layer. They are particularly valuable in rapid prototyping, aerospace, and healthcare applications.
Digital Twins and SimulationDigital twin technology enables manufacturers to create virtual replicas of physical products and processes. This allows for real-time monitoring, analysis, and optimization of manufacturing operations. By simulating various scenarios, manufacturers can identify potential issues and optimize processes, reducing errors and waste.
IoT (Internet of Things) ConnectivityPrecision engineering machines are increasingly IoT-enabled, facilitating data collection and remote monitoring. Sensors embedded in machines provide real-time information about performance, maintenance needs, and quality control. This connectivity enables predictive maintenance, reducing downtime and improving overall efficiency.
Big Data AnalyticsThe vast amount of data generated by precision engineering machines can be harnessed through big data analytics. These analytics provide insights into machine performance, product quality, and production efficiency. Manufacturers can use this information to make data-driven decisions and continuously optimize operations.
Cloud ComputingCloud-based solutions are facilitating remote access to precision engineering machines and data. This allows manufacturers to manage and monitor their machines from anywhere, promote collaboration, and store large volumes of data securely.
These technological advancements dovetail seamlessly with the principles of Industry 4.0, which represents the fourth industrial revolution characterized by the fusion of digital technologies with manufacturing processes. The integration of Industry 4.0 principles into precision engineering machines has several profound implications
- Smart FactoriesPrecision engineering machines are central to the development of smart factories. These factories are equipped with interconnected machines and systems that communicate and collaborate in real time. This connectivity enables agile and flexible production, real-time decision-making, and resource optimization.
- Predictive MaintenanceIndustry 4.0 principles empower precision engineering machines to predict maintenance needs based on data analysis. Machines can alert operators to potential issues, reducing unplanned downtime and maintenance costs.
- Customization and Mass CustomizationAdvanced automation and data-driven processes enable the efficient customization of products to meet individual customer needs. Mass customization, the ability to produce unique products at scale, becomes achievable.
Industry 4.0 integration extends beyond the factory floor. It encompasses the entire supply chain, providing end-to-end visibility and optimization opportunities. Precision engineering machines contribute to the efficient production of components and products within this integrated ecosystem.
In conclusion, technological advancements and the integration of Industry 4.0 principles are driving the Global Precision Engineering Machines Market into a new era of innovation and efficiency. These developments are propelling industries forward, allowing for the production of increasingly complex and precise components while optimizing manufacturing processes. As the pace of technological progress continues, the impact on precision engineering will be profound, shaping the future of manufacturing in an interconnected and data-driven world..
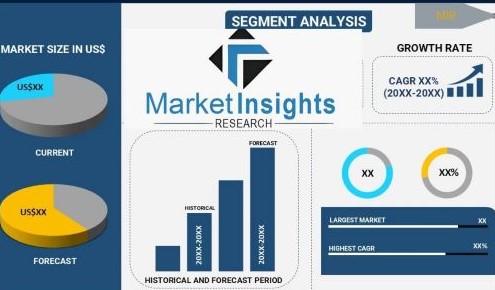
Growing Complexity of Product Designs
The Global Precision Engineering Machines Market is experiencing a notable surge in demand, largely propelled by the growing complexity of product designs across various industries. This increasing complexity is redefining the requirements for precision engineering, driving the need for advanced machines and technologies that can meet the intricate demands of modern product design.
One of the primary drivers behind the trend of growing product complexity is the relentless pursuit of innovation and differentiation. In today's highly competitive global market, companies are striving to develop products that stand out in terms of performance, functionality, aesthetics, and user experience. This drive for innovation has led to product designs that are far more intricate and sophisticated than ever before.
In the automotive sector, for example, the push for electric and autonomous vehicles has given rise to complex systems that require precise manufacturing. Electric vehicles incorporate intricate battery systems and advanced electronics, while autonomous vehicles rely on sensor arrays and sophisticated control systems. Precision engineering machines are crucial for producing the components and assemblies needed for these cutting-edge vehicles.
Similarly, the aerospace industry is witnessing a surge in complex product designs, driven by the demand for more fuel-efficient aircraft, advanced materials, and improved safety features. Aircraft components, such as turbine blades and complex airframe structures, require precision engineering machines capable of working with high-strength materials while maintaining tight tolerances.
The electronics sector is another key beneficiary of precision engineering advancements. The trend toward miniaturization has resulted in smaller, more intricate electronic devices. Precision engineering machines play a pivotal role in manufacturing microelectronics, semiconductor components, and advanced printed circuit boards (PCBs). These machines can handle the intricate geometries and tight tolerances essential for modern electronics.
In the medical device industry, product designs are becoming increasingly complex to meet the demands of minimally invasive procedures, patient-specific treatments, and improved diagnostic tools. Precision engineering machines enable the production of intricate medical implants, surgical instruments, and diagnostic equipment with high precision and reliability.
Furthermore, consumer electronics, such as smartphones and wearable devices, exemplify the growing complexity of product designs. These devices incorporate multiple sensors, high-resolution displays, and advanced materials, all of which require precision manufacturing to ensure quality and performance.
The advent of Industry 4.0 and the Internet of Things (IoT) further intensifies the complexity of product designs. Smart, connected devices often involve intricate assemblies of sensors, actuators, and communication modules. Precision engineering machines are essential for creating the precise components needed for these IoT-enabled products.
3D printing and additive manufacturing technologies also contribute to the complexity of product designs. While these technologies enable innovative and complex geometries, they require precision machines to ensure the accuracy and repeatability of printed parts.
Key Market Challenges
Rapid Technological Advancements and Obsolescence
The relentless pace of technological advancements poses a substantial challenge in the Precision Engineering Machines Market. Machines that were once state-of-the-art quickly become obsolete, rendering significant investments outdated. Manufacturers must grapple with the constant need for upgrades or replacements to stay competitive. Furthermore, the rapid evolution of technologies like additive manufacturing and nanotechnology necessitates constant adaptation, making it challenging for companies to keep up with the latest developments and integrate them effectively into their precision engineering processes.
Skill Shortages and Workforce Training
The Global Precision Engineering Machines Market faces a significant challenge in the form of skill shortages and the imperative need for workforce training. This challenge arises from the evolving nature of precision engineering, where cutting-edge technologies and automation have become integral to manufacturing processes. The shortage of skilled labor capable of operating, maintaining, and innovating with these advanced machines has become a critical bottleneck for many industries.
One of the primary facets of this challenge is the increasing complexity of precision engineering machines. As technology advances, these machines become more intricate, incorporating advanced control systems, automation features, and digital interfaces. Operating such machines requires a deep understanding of their functionalities, software interfaces, and the ability to troubleshoot when issues arise. Yet, there's a widening gap between the skills of the existing workforce and the requirements posed by these sophisticated machines.
Moreover, precision engineering is no longer confined to traditional machining techniques. It encompasses a broader spectrum, including additive manufacturing (3D printing), nanotechnology, and mechatronics. These diverse areas demand specialized knowledge and skills. For instance, additive manufacturing requires expertise in CAD (Computer-Aided Design), materials science, and an understanding of the unique considerations for building parts layer by layer. Finding individuals with this multifaceted skill set is a formidable task.
The shortage of skilled labor in the precision engineering sector is further exacerbated by the retirement of experienced technicians and engineers. As a generation of skilled professionals reaches retirement age, their expertise and institutional knowledge depart with them, leaving a void that is challenging to fill. The loss of this knowledge can hinder the efficient operation and maintenance of precision engineering machines, impacting productivity and quality.
To address these skill shortages, workforce training becomes essential. However, it's not just a matter of training for current technologies; it's about preparing the workforce for the future. This involves comprehensive training programs that encompass various aspects
Technical ProficiencyEmployees need to acquire proficiency in operating precision engineering machines, understanding their intricacies, and being able to optimize their performance. This includes knowledge of CNC (Computer Numerical Control) systems, automation, and control interfaces.
Software CompetenceAs precision engineering machines increasingly rely on software control and automation, employees must become adept at using software tools for machine programming, data analysis, and simulation. Proficiency in CAD/CAM (Computer-Aided Manufacturing) software is often essential.
Safety and ComplianceSafety is paramount in precision engineering. Workers must undergo training to ensure they can operate machines safely and adhere to industry regulations and safety standards.
Adaptability and InnovationGiven the rapid pace of technological change, workforce training should emphasize adaptability and the ability to embrace innovation. Employees should be encouraged to keep up with industry trends and emerging technologies.
Problem-Solving SkillsPrecision engineering often involves troubleshooting and problem-solving. Training programs should nurture these skills, enabling workers to identify and resolve issues efficiently.
Cross-Disciplinary KnowledgeWith the convergence of various technologies in precision engineering, workers may need cross-disciplinary knowledge. Training programs should expose them to related fields such as materials science, electronics, and robotics.
Continuous LearningWorkforce training should not be a one-time event but an ongoing process. Companies should invest in continuous learning opportunities to keep their employees' skills up-to-date.
In conclusion, the challenge of skill shortages and workforce training in the Global Precision Engineering Machines Market is multifaceted. It encompasses the need for highly specialized skills, the retirement of experienced professionals, and the demand for continuous learning and adaptability. Addressing these challenges requires a concerted effort by industries, educational institutions, and governments to develop comprehensive training programs and strategies for attracting and retaining talent in the precision engineering sector. Only through such efforts can the industry continue to thrive and innovate in an increasingly complex technological landscape.
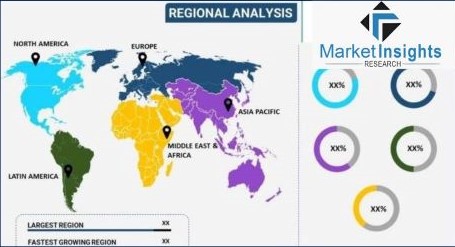
Cost and Budget Constraints
Precision engineering machines often involve substantial capital investments. These machines are critical for industries that demand high precision and quality, but the cost can be prohibitive for some businesses, particularly small and medium-sized enterprises (SMEs). Budget constraints can limit the adoption of advanced precision engineering technologies, potentially hindering competitiveness. Moreover, the need to continuously invest in cutting-edge machines, software, and tools to stay ahead in the market presents an ongoing financial challenge for companies seeking to balance innovation with cost management..
Key Market Trends
AI and Machine Learning Integration
Certainly, here are three prominent trends shaping the Global Precision Engineering Machines Market
Industry 4.0 Integration and Smart ManufacturingIndustry 4.0, often referred to as the fourth industrial revolution, is making a profound impact on the precision engineering machines market. The integration of Industry 4.0 principles into manufacturing processes is driving the development of smart factories and enabling highly connected and data-driven production environments. Precision engineering machines are at the forefront of this transformation, with several key trends emerging
Precision machines are equipped with sensors and communication interfaces, allowing them to collect and transmit data in real time. This connectivity enables remote monitoring, predictive maintenance, and data analytics, helping manufacturers optimize machine performance and minimize downtime.
The vast amount of data generated by precision machines is harnessed through big data analytics. These analytics provide insights into machine performance, quality control, and production efficiency. Manufacturers can make data-driven decisions, identify bottlenecks, and optimize operations.
Digital twin technology creates virtual replicas of physical machines and processes. Manufacturers can use these digital twins for simulation, testing, and real-time monitoring. This capability enables the identification of potential issues before they occur, reducing errors and enhancing product quality.
Autonomous ManufacturingThe integration of artificial intelligence (AI) and machine learning allows precision machines to make autonomous decisions. They can adjust parameters, optimize toolpaths, and adapt to changing conditions, increasing efficiency and reducing the need for human intervention. Smart manufacturing driven by Industry 4.0 principles is not only improving productivity but also enabling greater flexibility and agility in responding to market demands. Precision engineering machines are central to this transformation, as they are key enablers of the interconnected and data-driven manufacturing landscape.
Additive Manufacturing and 3D PrintingAdditive manufacturing, commonly known as 3D printing, is revolutionizing precision engineering. This trend is characterized by the layer-by-layer construction of parts and components, offering several advantages- Complex GeometriesAdditive manufacturing allows for the creation of highly complex and intricate geometries that were previously challenging or impossible to achieve with traditional machining methods.
Prototyping and Rapid Iteration3D printing enables rapid prototyping, reducing the time and cost required to develop and test new designs. This agility fosters innovation and accelerates product development cycles. CustomizationAdditive manufacturing supports mass customization, where products can be tailored to individual customer needs without significantly increasing production costs.
Materials InnovationAdvances in additive manufacturing are expanding the range of materials that can be used, including metals, polymers, ceramics, and composites. This broadens its applicability across various industries. While additive manufacturing is transforming industries such as aerospace, healthcare, and automotive, precision engineering machines are adapting to accommodate 3D printing technologies. Hybrid machines that combine traditional subtractive machining with additive capabilities are becoming more prevalent, allowing manufacturers to harness the benefits of both approaches.
Advanced Materials and NanotechnologyThe precision engineering machines market is witnessing a shift towards the use of advanced materials and nanotechnology, driven by the demand for products with exceptional strength, durability, and performance. Several trends are emerging in this regard
Precision engineering machines are increasingly employed to work with advanced alloys such as titanium, high-strength steels, and superalloys. These materials are essential in industries like aerospace and automotive, where lightweight yet strong components are required for improved fuel efficiency and performance.
- Nanotechnology, which involves manipulating materials at the nanoscale, is playing a pivotal role in precision engineering. Nanomaterials offer unique properties, and precision machines are used to manufacture components with nanoscale features. This is particularly relevant in electronics, optics, and medical devices.
Composite materials, made from a combination of different materials, are gaining prominence in industries like aerospace and automotive due to their lightweight and high-strength properties. Precision machines are essential for shaping and machining composite components to exact specifications. Precision engineering machines are adapting to work with ceramics and high-performance polymers. These materials are valued for their resistance to extreme temperatures, wear, and corrosion, making them suitable for demanding applications in various industries.
The trend towards advanced materials and nanotechnology underscores the need for precision engineering machines that can handle the unique challenges posed by these materials. This includes specialized cutting tools, tool coatings, and machining techniques designed to work with advanced materials while maintaining tight tolerances and surface finishes.
In conclusion, the Global Precision Engineering Machines Market is undergoing transformative changes driven by the integration of Industry 4.0 principles, the rise of additive manufacturing, and the adoption of advanced materials and nanotechnology. These trends are reshaping manufacturing processes, enhancing product capabilities, and opening up new opportunities for innovation across a wide range of industries. Precision engineering machines are at the forefront of these trends, enabling manufacturers to meet the challenges and opportunities of the rapidly evolving technological landscape.
Segmental Insights
Type Insights
The CNC Machine Tools segment is dominating the global precision engineering machines market. In 2022,VersatilityCNC machine tools are versatile machines that can be used to perform a wide range of tasks, including milling, turning, grinding, and drilling. This makes them ideal for manufacturing a wide range of products, from precision components to complex assemblies.
Accuracy and precisionCNC machine tools are capable of producing parts with high accuracy and precision. This is essential for many industries, such as aerospace, automotive, and medical.
ProductivityCNC machine tools can operate at high speeds and with minimal manual intervention. This makes them highly productive machines, which can help businesses to reduce costs and improve efficiency. Other segments, such as EDM machine tools and others, are also experiencing significant growth in the precision engineering machines market. However, CNC machine tools are expected to remain the dominating segment in this market for the foreseeable future.
In the coming years, it is expected that the global precision engineering machines market will continue to grow at a rapid pace. This growth will be driven by the increasing demand for high-precision and complex components in a wide range of industries, such as aerospace, automotive, and medical. CNC machine tools are expected to play a key role in this growth, as they offer the versatility, accuracy, precision, and productivity that are required to manufacture these components.
Here are some additional insights into the CNC machine tools segment of the global precision engineering machines marketThe Asia Pacific region is the largest market for CNC machine tools, followed by North America and Europe. The automotive industry is the largest end-user of CNC machine tools, followed by the aerospace and medical industries. The increasing demand for automation and the growing adoption of smart manufacturing technologies are driving the growth of the CNC machine tools market. The CNC machine tools segment is a highly competitive segment with a number of key players, such as DMG Mori, Mazak, and Okuma. These players are constantly innovating and developing new CNC machine tools to meet the growing demands of their customers.
Regional Insights
Asia Pacific is the dominating region in the Global Precision Engineering Machines Market. This dominance is attributed to a number of factors, includingGrowing manufacturing sectorAsia Pacific is the world's largest manufacturing hub, with countries such as China, Japan, and South Korea playing a leading role. The growth of the manufacturing sector in the region is driving the demand for precision engineering machines. Government supportGovernments in the Asia Pacific region are providing significant support to the manufacturing sector, including financial incentives and subsidies for the purchase of precision engineering machines. Rising demand for high-quality productsConsumers in the Asia Pacific region are increasingly demanding high-quality products. This is driving the demand for precision engineering machines, which are essential for manufacturing high-quality products.
Other regions, such as North America and Europe, are also experiencing significant growth in the precision engineering machines market. However, Asia Pacific is expected to remain the dominating region in this market for the foreseeable future.
In the coming years, it is expected that the global precision engineering machines market in Asia Pacific will continue to grow at a rapid pace. This growth will be driven by the continued growth of the manufacturing sector in the region, the rising demand for high-quality products, and the increasing government support for the manufacturing sector.
Here are some additional insights into the precision engineering machines market in Asia Pacific
China is the largest market for precision engineering machines in Asia Pacific, followed by Japan and South Korea.The automotive, aerospace, and electronics industries are the major end-users of precision engineering machines in Asia Pacific. The increasing adoption of automation and the growing trend of smart manufacturing are driving the growth of the precision engineering machines market in Asia Pacific. The precision engineering machines market in Asia Pacific is highly competitive, with a number of key players, such as DMG Mori, Mazak, and Okuma. These players are constantly innovating and developing new precision engineering machines to meet the growing demands of their customers.
Recent Developments
- DMG MoriIn September2023, DMG Mori announced the launch of its new LASERTEC 12 5axis laser metaldeposition (LMD) machine. The LASERTEC 12 5axis is a highly versatile machinethat can be used to produce a wide range of parts, from simple to complex. Itis also one of the fastest LMD machines on the market, with deposition speedsof up to 10 kg/h.
- MazakIn August 2023,Mazak announced the launch of its new INTEGREX i-630V multi-tasking machine.The INTEGREX i-630V is a highly productive machine that can perform a widerange of tasks, including turning, milling, drilling, and boring. It is alsoequipped with a number of advanced features, such as a high-speed spindle and adirect drive table.
Key Market Players
- DMG MORI CO., LTD.
- Makino Milling Machine Co.,Ltd.
- Haas Automation, Inc.
- TRUMPF GmbH + Co. KG
- GF Machining SolutionsManagement SA
- Fanuc Corporation
- Okuma Corporation
- Chiron Group SE
- Yamazaki Mazak Corporation
- Mitsubishi Electric Corporation
By Type | For a single, multi and corporate client license, the report will be available in PDF format.
Sample report would be given you in excel format. For more questions please contact: Within 24 to 48 hrs. You can contact Sales team (sales@marketinsightsresearch.com) and they will direct you on email You can order a report by selecting payment methods, which is bank wire or online payment through
any Debit/Credit card, Razor pay or PayPal. Discounts are available. Hard Copy Email |