United States 3D Printing Market Segmented by Component Type ((Printer Type (Desktop, Industrial), Material (Polymer, Metal, Ceramic), Software (Design, Inspection, Printer, and Scanning)), By Technology (Stereolithography, Fuse Deposition Modelling, Selective Laser Sintering, Inkjet Printing, Polyjet Printing, Laser Metal Deposition, and Others), By End User (Automotive, Aerospace & Defense, Heal
Published Date: November - 2024 | Publisher: MIR | No of Pages: 320 | Industry: ICT | Format: Report available in PDF / Excel Format
View Details Buy Now 2890 Download Sample Ask for Discount Request CustomizationForecast Period | 2024-2028 |
Market Size (2022) | USD 1.82 Billion |
CAGR (2023-2028) | 20.52% |
Fastest Growing Segment | Desktop |
Largest Market | Northeast Region |
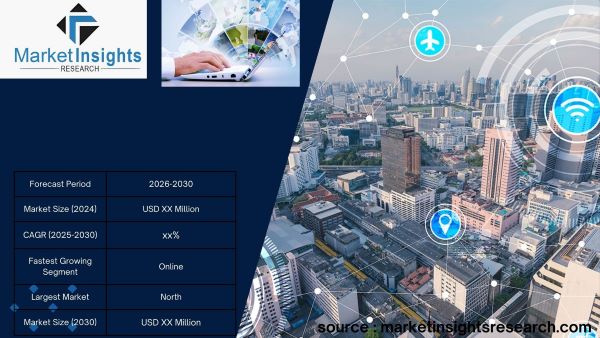
Market Overview
The United States 3D Printing market
Key Market Drivers
Advancements in 3D Printing Technologies
One of the primary drivers propelling the United States 3D printing market is the continuous advancements in 3D printing technologies. Over the years, 3D printing has evolved from a novelty to a sophisticated manufacturing process capable of producing complex, high-precision components with a wide range of materials. These technological advancements encompass improvements in printing speed, resolution, and the variety of materials that can be used. Innovations such as multi-material printing, continuous printing, and high-speed 3D printing have expanded the applications of 3D printing across industries. One notable advancement is the development of metal 3D printing, enabling the production of robust and intricate metal parts for aerospace, automotive, and medical applications. Additionally, the emergence of large-scale industrial 3D printers has enabled the creation of larger, more complex components, opening new possibilities in industries like construction and architecture. As technology continues to evolve, the United States remains at the forefront of these developments, driving the growth and adoption of 3D printing across a spectrum of sectors.
Increasing Adoption in Aerospace and Defense
The aerospace and defense industries play a pivotal role in driving the growth of the United States 3D printing market. These sectors demand lightweight, high-performance components with precise geometries, making 3D printing an ideal manufacturing method. Aerospace manufacturers leverage 3D printing to produce aircraft components like turbine blades, fuel nozzles, and structural elements. It offers the advantage of reduced weight, improved fuel efficiency, and faster prototyping, all critical factors in aviation. In the defense sector, 3D printing is used to create customized components for military equipment and vehicles. Rapid prototyping capabilities enable quick design iterations and the production of specialized parts. Furthermore, the ability to print complex shapes and structures, such as drones and unmanned vehicles, enhances military capabilities. The ongoing collaboration between government agencies, defense contractors, and 3D printing companies in the United States continues to drive innovation and adoption in these crucial industries.
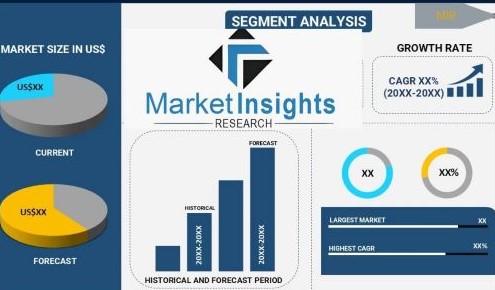
Growth in Healthcare Applications
The healthcare sector has emerged as a significant driver of the United States 3D printing market, with applications ranging from patient-specific implants and prosthetics to anatomical models and pharmaceuticals. Personalized medicine is at the forefront of this trend, with 3D printing enabling the production of customized medical devices tailored to individual patient needs. Orthopedic implants, such as hip and knee replacements, are commonly produced using 3D printing, ensuring a precise fit and reducing the risk of complications. Additionally, the technology is employed in dental applications, where it is used to create crowns, bridges, and dental models.
3D printing also plays a critical role in the creation of anatomical models for surgical planning and medical education. These detailed, patient-specific models allow surgeons to practice procedures and plan surgeries more effectively, ultimately improving patient outcomes. Furthermore, the pharmaceutical industry has embraced 3D printing for the development of personalized medications and drug delivery systems. The ability to produce precise dosages and formulations tailored to individual patients is a game-changer in pharmaceutical research and production.
Expanding Automotive Applications
The automotive industry is another influential driver of the United States 3D printing market. Automakers are increasingly turning to 3D printing to reduce production costs, improve design flexibility, and enhance the performance of vehicles. This trend is particularly evident in the production of prototypes, custom components, and even entire vehicles. 3D printing allows for rapid prototyping, enabling automotive manufacturers to iterate designs quickly and test new concepts with minimal lead time. This speed in product development accelerates time-to-market for new vehicle models and innovations. Moreover, 3D printing is used to create lightweight and complex parts, such as engine components, brackets, and interior elements, contributing to improved fuel efficiency and overall vehicle performance. In electric vehicles (EVs), 3D printing helps optimize the design of battery housings and other critical components. Additionally, the restoration and customization of classic cars have become popular applications of 3D printing. Enthusiasts use technology to replicate rare or obsolete parts, preserving automotive heritage.
Key Market Challenges
Intellectual Property and Counterfeiting Concerns
The United States 3D printing market is not without its challenges, and one of the prominent issues facing this industry is related to intellectual property (IP) and counterfeiting concerns. As 3D printing technology becomes more accessible and affordable, it has raised significant questions about the protection of intellectual property rights and the potential for widespread counterfeiting. One of the primary challenges in this area is the ease with which 3D printing allows individuals and entities to create replicas or counterfeit versions of products. This poses a significant threat to industries that rely on the exclusivity of their designs and products. For example, manufacturers of luxury goods, automotive parts, and consumer electronics are vulnerable to counterfeiting through 3D printing.
Furthermore, it can be difficult to trace and monitor the production of counterfeit goods in the 3D printing space. Traditional methods of tracking and enforcement, such as patents and trademarks, may not be sufficient to address this challenge effectively. As a result, companies must explore new strategies and technologies to protect their intellectual property. Another aspect of this challenge is the potential for unauthorized copying of copyrighted materials, such as movies, music, and literature. 3D printers can be used to create physical copies of copyrighted objects, which has the potential to infringe upon the rights of content creators and media companies. Policymakers and stakeholders in the 3D printing industry need to find a balance between fostering innovation and protecting intellectual property.
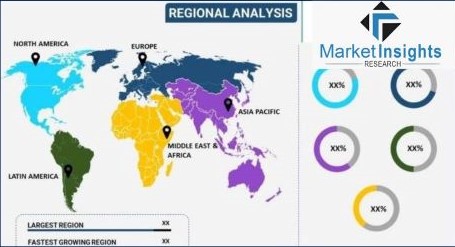
Material Limitations and Quality Control in 3D Printing
Another significant challenge facing the United States 3D printing market is related to material limitations and quality control. While 3D printing offers unparalleled design flexibility and customization, it is still constrained by the materials found at for printing and the need for consistent quality in manufactured products. One key limitation is the range of materials suitable for 3D printing. While there has been significant progress in developing new materials for various printing technologies, many industries require materials with specific properties, such as strength, durability, or biocompatibility. Ensuring the availability of a broad and diverse range of materials is crucial to meeting the needs of different applications.
Quality control is another challenge, especially in industries where precision and reliability are paramount. The 3D printing process can introduce defects or inconsistencies in printed parts, which may not always be immediately apparent. In sectors like aerospace, healthcare, and automotive, these defects can have serious consequences. Ensuring consistent quality and reliability in 3D-printed parts is an ongoing challenge. Moreover, as 3D printing becomes more prevalent in industries like aerospace and healthcare, stringent regulatory requirements must be met. The development of standardized testing and certification processes for 3D-printed parts is essential to ensure compliance with industry standards and regulations.
Key Market Trends
Increased Adoption of 3D Printing in Healthcare
The United States 3D printing market has witnessed a significant uptick in the adoption of 3D printing technology across various industries, with one of the most prominent being healthcare. Over the past few years, 3D printing has gained prominence in healthcare due to its potential to revolutionize patient care, medical device manufacturing, and even pharmaceuticals. One of the key drivers of this trend is the customization and personalization capabilities of 3D printing technology. In the healthcare sector, 3D printing is being used to create patient-specific implants, prosthetics, and anatomical models. Surgeons can now use 3D-printed models of a patient's unique anatomy to plan and practice complex surgeries, resulting in better outcomes and reduced surgical risks.
Furthermore, the COVID-19 pandemic highlighted the agility of 3D printing in responding to emergencies. When faced with shortages of personal protective equipment (PPE), healthcare facilities and individuals turned to 3D printing to produce face shields, respirator parts, and other critical supplies. This experience has accelerated the integration of 3D printing into healthcare supply chains. The increased adoption of 3D printing in healthcare is not limited to medical devices and PPE. Pharmaceutical companies are exploring 3D printing to produce personalized medicines and drug delivery systems. This trend is expected to continue as regulatory frameworks adapt to accommodate 3D-printed pharmaceuticals.
Expansion of 3D Printing in Aerospace and Defense
The aerospace and defense sector in the United States has been at the forefront of 3D printing adoption. This trend is expected to continue and expand as 3D printing technology matures and proves its worth in various applications within the industry. One significant driver for the increased use of 3D printing in aerospace and defense is the ability to reduce the weight of components while maintaining or even enhancing their structural integrity. This weight reduction has a direct impact on fuel efficiency in aviation and mobility in defense systems. Moreover, the aerospace industry's rigorous testing and certification processes have validated the reliability of 3D-printed components, further boosting their adoption. In addition to weight reduction, 3D printing allows for the rapid prototyping and production of complex geometries that would be challenging or impossible to achieve with traditional manufacturing methods. This capability is particularly valuable in the development of advanced aircraft and spacecraft components. The defense sector is also exploring 3D printing for producing spare parts on-demand in remote locations, reducing the need for extensive supply chains and inventory management. This not only saves costs but also increases the readiness of military assets.
Growing Interest in Sustainable 3D Printing
Sustainability has become a major driver of market trends across various industries, including 3D printing. In the United States, there is a growing interest in making 3D printing processes more environmentally friendly and sustainable. One aspect of sustainability in 3D printing is the choice of materials. Traditional 3D printing materials, such as plastics, can be environmentally detrimental. However, there is a shift towards using more sustainable and biodegradable materials, including recycled plastics and bio-based polymers. Additionally, the development of metal 3D printing using recycled materials is gaining traction, particularly in industries like automotive and aerospace.
Another aspect is the reduction of waste in the 3D printing process itself. Additive manufacturing allows for precise material usage, minimizing waste compared to subtractive manufacturing methods. Recycling and reusing 3D-printed parts or materials are also becoming more common practices. Furthermore, 3D printing can contribute to sustainability by enabling local production, which reduces transportation emissions associated with long-distance shipping. This concept aligns with the broader trend of distributed manufacturing, where products are produced closer to the point of consumption.
Segmental Insights
Technology Insights
Based on technology, the stereolithography segment emerges as the predominant segment in the United States building automation & control systems market, exhibiting unwavering dominance projected throughout the forecast period.
End User Insights
Based on end user, the automotive segment in the United States building automation & control systems market emerges as a formidable frontrunner, exerting its dominance and shaping the market's trajectory throughout the forecast period. This dominance is attributed to the automotive industry's increasing adoption of BACS solutions to optimize manufacturing processes, enhance operational efficiency, and ensure the highest levels of product quality. Building automation systems play a pivotal role in automotive manufacturing plants by managing and controlling various aspects of production, including HVAC systems, robotics, and lighting. These systems enable automotive manufacturers to streamline their operations, reduce energy consumption, and maintain stringent quality standards. Additionally, as the automotive industry embraces automation and Industry 4.0 principles, the demand for advanced BACS technologies is expected to grow further, reinforcing the automotive segment's status as a key driver in shaping the trajectory of the United States BACS market.
Regional Insights
The Northeast region of the United States has undeniably established itself as the preeminent epicenter of innovation, adoption, and influence within the country's 3D printing market. Comprising states such as Massachusetts, New York, and Pennsylvania, this region has consistently demonstrated an exceptional commitment to pushing the boundaries of 3D printing technology. One of the key drivers of the Northeast's dominance is the concentration of world-class universities and research institutions. These academic powerhouses actively engage in cutting-edge research, pioneering advancements in 3D printing materials, processes, and applications. As a result, the region serves as a magnet for top talent and innovative startups eager to leverage these breakthroughs. Furthermore, the Northeast's industrial landscape, particularly in industries like healthcare, aerospace, and manufacturing, has a voracious appetite for 3D printing solutions. Hospitals and healthcare institutions employ 3D printing for customized medical implants and prosthetics, while aerospace companies utilize it for lightweight, complex aerospace components. This strong industrial demand propels the region's leadership in the 3D printing market.
Recent Developments
- In June 2023, HeyGearslaunched its first professional desktop 3D printer for consumers, theUltraCraft Reflex. The Reflex is an all-in-one production platform that enablesusers to realize their ideas faster and bring them to life. It features ahigh-resolution resin printer, a cleaning and curing machine, and HeyGears' ownself-developed materials. The Reflex is also equipped with pre-processingsoftware that makes it easy to use, even for beginners.
- In March 2023, the inaugurallaunch of the world's first 3D-printed rocket, known as the Terran 1, faced aseries of setbacks. This innovative rocket was crafted by Relativity Space, anaerospace startup based in California. Initially slated for liftoff on March 8,the launch had to be delayed due to concerns regarding the temperature of therocket's fuel. Subsequently, a second launch attempt was made on March 22, butthis too had to be abandoned due to an anomaly detected in the second-stageengine.
Key Market Players
- Stratasys Ltd.
- 3D Systems, Inc.
- Proto Labs, Inc.
- Materialise NV
- Desktop Metal Inc.
- HP Inc.
- Carbon, Inc.
- Formlabs, Inc.
- Markforged, Inc.
By Component | By Technology | By End User | By Region |
|
|
Related Reports
- Metaverse for Automotive Market Size - By Component (Hardware, Software, Services), By Technology (Virtual Reality, Augm...
- SVOD Market Size - By Content (General Entertainment, Niche Content, Original Programming), By Pricing Model (Premium, A...
- Multimodal AI Market Size - By Component (Solution, Service), By Technology (Machine Learning, Natural Language Processi...
- AVOD Market Size - By Content (Movies, TV Shows, Original Series, News, Sports, User-generated Content), By Platform (S...
- Premium Finance Market - By Type (Life Insurance, Non-life Insurance), By Interest Rate (Fixed Interest Rate, Floating I...
- Gift Cards Market - By Type (Closed-loop Gift Cards, Open-loop Gift Cards), By Distribution Channel (Online, Offline), B...
Table of Content
To get a detailed Table of content/ Table of Figures/ Methodology Please contact our sales person at ( chris@marketinsightsresearch.com )
List Tables Figures
To get a detailed Table of content/ Table of Figures/ Methodology Please contact our sales person at ( chris@marketinsightsresearch.com )
FAQ'S
For a single, multi and corporate client license, the report will be available in PDF format. Sample report would be given you in excel format. For more questions please contact:
Within 24 to 48 hrs.
You can contact Sales team (sales@marketinsightsresearch.com) and they will direct you on email
You can order a report by selecting payment methods, which is bank wire or online payment through any Debit/Credit card, Razor pay or PayPal.
Discounts are available.
Hard Copy