North America 3D Printing Market By Component (Hardware, Software, Services), By Printer Type (Desktop 3D Printer, Industrial Printer), By Technology (Stereolithography, Fuse Deposition Modeling, Selective Laser Sintering, Electron Beam Melting, Laminated Object Manufacturing, Others), By Process (Powder Bed Fusion, Vat Polymerization/ Liquid Based, Material Extrusion, Binder Jetting, Material Jet
Published Date: November - 2024 | Publisher: MIR | No of Pages: 320 | Industry: ICT | Format: Report available in PDF / Excel Format
View Details Buy Now 2890 Download Sample Ask for Discount Request CustomizationForecast Period | 2025-2029 |
Market Size (2023) | USD 6.92 Billion |
Market Size (2029) | USD 17.53 Billion |
CAGR (2024-2029) | 16.58% |
Fastest Growing Segment | Industrial Printer |
Largest Market | United States |
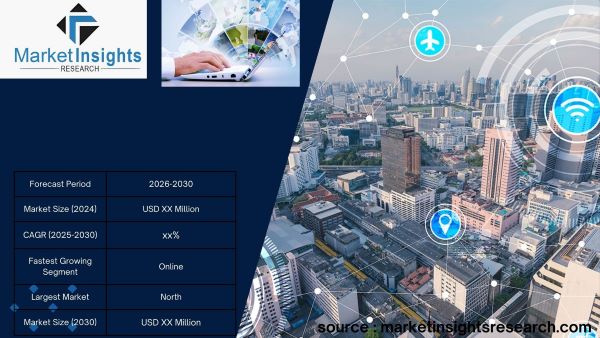
Market Overview
The North America
The North America 3D printing market is experiencing significant growth, driven by advancements in technology, increased adoption across industries, and growing investments in research and development. The market, which encompasses various components such as hardware, software, services, and materials, is largely supported by industries like automotive, aerospace, healthcare, and manufacturing. The ongoing demand for customized products and the shift toward on-demand production are major factors propelling the expansion of 3D printing in the region.
In the automotive and aerospace sectors, 3D printing offers enhanced design flexibility, enabling the production of complex and lightweight parts with greater precision. This capability is particularly crucial in reducing overall vehicle weight, thereby improving fuel efficiency and performance. In the healthcare industry, 3D printing is being increasingly utilized to produce patient-specific medical implants, prosthetics, and even bioprinted organs, revolutionizing the way treatments are delivered. As technology evolves, the potential for personalized healthcare solutions continues to grow, contributing to the expansion of the 3D printing market in North America.
One of the key trends influencing market growth is the shift from prototyping to full-scale production. Traditionally, 3D printing was predominantly used for prototyping due to its ability to create detailed models quickly and cost-effectively. However, as technologies advance, particularly with metal and polymer-based 3D printers, there is a notable move toward end-use production, making 3D printing a viable option for mass manufacturing. This transition is particularly evident in industries like consumer electronics, where companies are leveraging the technology for rapid product iterations and shorter time-to-market.
Furthermore, government initiatives and funding are playing a significant role in supporting the 3D printing ecosystem in North America. Various programs are aimed at promoting innovation, enhancing manufacturing capabilities, and supporting the development of skilled labor to meet the growing demand for 3D printing expertise. Additionally, collaborations between industry players, academic institutions, and research organizations are fostering the development of new materials and advanced printing techniques.
Key Market Drivers
Technological Advancements in 3D Printing
The North America 3D printing market is primarily driven by continuous technological advancements. Innovations such as multi-material printing, hybrid manufacturing, and improvements in speed, precision, and scalability are expanding the capabilities of 3D printing. For instance, metal 3D printing, which initially faced challenges related to cost and reliability, has seen significant breakthroughs in recent years. Techniques like Direct Metal Laser Sintering (DMLS) and Electron Beam Melting (EBM) are now being widely adopted across industries like aerospace, automotive, and healthcare. Furthermore, the integration of AI and machine learning with 3D printing processes is enhancing production efficiency and material optimization. These developments allow for better design flexibility, shorter production times, and cost-effective manufacturing, which are critical for the adoption of 3D printing in end-use production. As technology continues to evolve, the range of applications for 3D printing in North America is expected to expand, driving market growth.
Rising Demand for Customized Products
The increasing demand for personalized and customized products across various industries is a major driver of the North America 3D printing market. Industries such as healthcare, automotive, and consumer goods are leveraging 3D printing’s ability to produce customized products tailored to specific customer needs. In the healthcare sector, for example, 3D printing is being used to create patient-specific medical devices, implants, and prosthetics. This customization ensures better fit and functionality, improving patient outcomes. Similarly, in the consumer goods sector, 3D printing allows for the production of customized jewelry, footwear, and fashion accessories. The automotive industry is also adopting 3D printing for customized parts and components that are designed according to specific vehicle models. The growing trend towards mass customization is expected to fuel the adoption of 3D printing technologies, as traditional manufacturing methods are often too rigid or costly to accommodate individualized production.
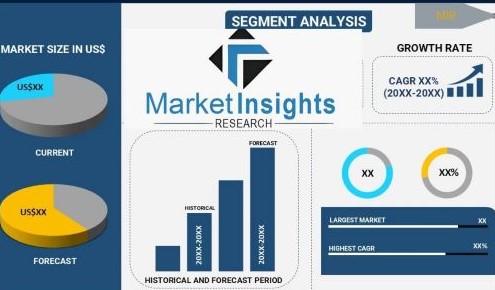
Growing Adoption in Aerospace and Defense Industries
The aerospace and defense industries in North America are significant adopters of 3D printing technologies. The ability to produce lightweight yet durable components with intricate geometries makes 3D printing particularly attractive to these sectors. In aerospace, weight reduction is a critical factor as it directly impacts fuel efficiency and operational costs. By using 3D printing, manufacturers can create complex structures that are both strong and lightweight, something traditional manufacturing methods struggle to achieve. Additionally, the defense industry benefits from the flexibility and speed that 3D printing offers, enabling rapid prototyping and the production of mission-critical components on demand. This is especially important in scenarios where supply chains are disrupted, and immediate part replacement is required. The increasing focus on enhancing operational efficiency, coupled with the ongoing innovation in material science, is expected to drive further adoption of 3D printing in these sectors, boosting market growth in North America.
Government Initiatives and Funding Support
Government initiatives and funding play a vital role in driving the North America 3D printing market. Federal and state governments are actively promoting the adoption of advanced manufacturing technologies, including 3D printing, as part of broader initiatives to strengthen domestic manufacturing capabilities and maintain technological leadership. Programs such as the National Network for Manufacturing Innovation (NNMI) and America Makes are focused on accelerating the development and deployment of 3D printing technologies by providing funding, infrastructure, and training. Additionally, government agencies are partnering with academic institutions and private enterprises to foster innovation and develop skilled workforces. Grants and subsidies are also being provided to small and medium-sized enterprises (SMEs) to encourage the adoption of 3D printing technology. These initiatives not only lower the barriers to entry for companies but also stimulate research and development efforts, resulting in new applications and broader market adoption.
Key Market Challenges
High Initial Investment Costs
One of the most significant challenges facing the North American 3D printing market is the high initial investment required for adopting this technology. While 3D printing is often praised for its long-term cost benefits, such as reduced material waste and faster production cycles, the upfront costs associated with acquiring advanced 3D printers, software, and skilled labor can be prohibitively expensive for many businesses. Industrial-grade 3D printers, which are capable of producing high-quality and complex parts, often come with a steep price tag that can range from tens of thousands to several hundred thousand dollars. Moreover, businesses need to invest in specialized software that facilitates design and production, as well as in ongoing maintenance and upgrades. These high costs create a barrier to entry, particularly for small and medium-sized enterprises (SMEs), limiting the widespread adoption of 3D printing in North America. For many companies, the return on investment (ROI) is not immediately clear, especially in industries where traditional manufacturing methods are well-established and already optimized for efficiency. As a result, businesses may be hesitant to transition from conventional production methods to 3D printing without concrete proof of financial gains.
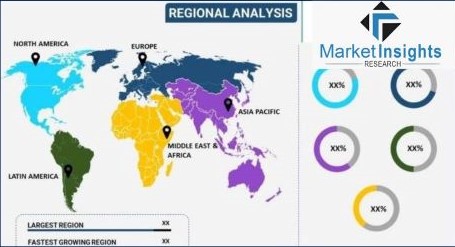
Complexity of Integrating with Traditional Manufacturing
Another challenge in the North American 3D printing market is the difficulty of integrating additive manufacturing processes into traditional manufacturing workflows. Unlike conventional manufacturing methods, which are well-understood and have established protocols, 3D printing requires a different set of skills, tools, and approaches. For businesses accustomed to mass production through injection molding, CNC machining, or casting, the integration of 3D printing presents several hurdles. Issues such as maintaining consistent quality across different production batches, ensuring scalability for large volumes, and aligning with existing supply chain and production schedules can be daunting. Additionally, the digital nature of 3D printing necessitates greater collaboration between design, engineering, and production teams, often requiring new training and changes in workflow management. These complexities can slow down adoption rates, as companies weigh the benefits of 3D printing against the potential disruptions it could introduce into their established processes. Moreover, in sectors where precision and reliability are paramount, such as aerospace and medical device manufacturing, the lack of standardization and certification protocols for 3D printed parts can create further integration challenges. The need for developing new quality control systems and gaining regulatory approval can delay the full-scale adoption of 3D printing.
Intellectual Property (IP) Concerns
The issue of intellectual property (IP) protection poses a significant challenge in the North American 3D printing market. The nature of 3D printing technology, which relies heavily on digital files for production, makes it vulnerable to unauthorized reproduction and distribution. As the technology advances and becomes more accessible, concerns over IP theft have grown. Companies that invest heavily in the research and development of new products risk having their designs copied and shared without their consent, leading to potential financial losses. This is particularly concerning in industries like consumer goods, automotive, and fashion, where design uniqueness is a critical competitive advantage. The ease with which digital files can be replicated, modified, and distributed online increases the likelihood of IP infringement. Current legal frameworks have struggled to keep pace with the rapid evolution of 3D printing technology, leaving businesses with limited recourse in the event of IP violations. This challenge is further compounded by the global nature of 3D printing, where products designed in one country can be easily reproduced in another, complicating enforcement across different jurisdictions. As a result, some companies may be hesitant to fully embrace 3D printing, fearing that their valuable designs could be compromised. Addressing these concerns will require not only advances in technology, such as secure file-sharing systems and watermarking, but also stronger legal protections and international agreements that can adapt to the nuances of digital manufacturing.
Material Limitations and High Costs
The North American 3D printing market faces significant material-related challenges, particularly in terms of availability, performance, and cost. Although there has been notable progress in the development of new materials for 3D printing, such as high-strength polymers, metals, and biocompatible substances, the range of materials that are widely found at and suitable for diverse applications remains limited. For many industries, material performance is a critical factor, especially in sectors like aerospace, automotive, and healthcare, where durability, safety, and compliance with industry standards are non-negotiable. The development of specialized materials that can meet these stringent requirements is often time-consuming and expensive, limiting their adoption. Additionally, the high cost of these advanced materials can be a deterrent for companies considering large-scale production using 3D printing. Unlike traditional manufacturing methods, which benefit from economies of scale when it comes to raw material procurement, 3D printing often incurs higher per-unit costs for materials, especially in the case of small batch production. This challenge is particularly acute for businesses that operate on tight margins, as the cost savings realized in other areas of the production process may be offset by the expense of acquiring high-quality printing materials. As a result, the choice of materials found at for 3D printing is often a limiting factor, influencing the type of products that can be feasibly manufactured and the industries that can benefit most from the technology.
Regulatory and Certification Barriers
Regulatory and certification issues present another challenge for the North American 3D printing market. As 3D printing increasingly moves from prototyping to full-scale production, particularly in highly regulated industries like aerospace, healthcare, and defense, ensuring compliance with safety, quality, and performance standards becomes crucial. The lack of established certification pathways for 3D printed products creates uncertainty for manufacturers and can slow down the adoption of the technology. For example, in the medical field, gaining regulatory approval for 3D printed implants, prosthetics, and other devices can be a lengthy and complex process, involving rigorous testing to demonstrate that the products meet all necessary safety standards. Similarly, in the aerospace sector, 3D printed parts need to comply with strict industry certifications, which often require extensive documentation, testing, and validation. The absence of uniform standards and clear regulatory guidelines for additive manufacturing means that each new product may require a case-by-case evaluation, increasing time-to-market and overall costs. Moreover, as new materials and techniques are launched, existing regulations may need to be updated to account for the unique characteristics of 3D printed products. This regulatory complexity not only creates operational challenges for companies but also introduces legal and compliance risks. Overcoming these barriers will require greater collaboration between industry stakeholders, regulators, and standardization bodies to develop frameworks that facilitate the safe and efficient integration of 3D printing into mainstream production.
Key Market Trends
Growth of Metal 3D Printing
The growth of metal 3D printing in North America is one of the most significant trends in the market. Metal 3D printing, also known as additive manufacturing, is increasingly being adopted across industries such as aerospace, automotive, and medical devices. The demand for lightweight, durable, and complex metal components is driving this trend. In aerospace, for instance, metal 3D printing allows for the production of parts with intricate geometries that are difficult or impossible to achieve through traditional manufacturing methods. This not only reduces the weight of components but also enhances fuel efficiency and performance, crucial in an industry where even minor improvements can lead to significant cost savings. In the automotive sector, the ability to produce custom and high-performance parts quickly and cost-effectively is another driving force behind the adoption of metal 3D printing. Furthermore, in the medical industry, metal 3D printing is enabling the creation of patient-specific implants and prosthetics, improving treatment outcomes and patient satisfaction. As advancements in metal 3D printing technologies continue, including improvements in printing speed, material diversity, and quality control, the market is expected to see sustained growth. Additionally, the decreasing cost of metal 3D printers and materials is making this technology more accessible to small and medium-sized enterprises (SMEs), further expanding its market reach. This trend is also supported by increased research and development efforts aimed at improving the properties of metal powders and the capabilities of 3D printing systems. Overall, the growth of metal 3D printing is poised to revolutionize manufacturing processes across multiple industries in North America, offering new opportunities for innovation and efficiency.
Rise of On-Demand Production
The rise of on-demand production is a transformative trend in the North America 3D printing market, reshaping traditional manufacturing and supply chain models. On-demand production refers to the ability to produce goods as they are needed rather than relying on large inventories of pre-manufactured items. This trend is particularly impactful in industries such as consumer electronics, automotive, and healthcare, where customization and quick turnaround times are highly valued. The flexibility offered by 3D printing technology allows companies to produce highly customized products tailored to individual customer specifications. This is especially beneficial in the healthcare sector, where 3D printing is being used to create patient-specific medical devices, prosthetics, and even surgical tools. The ability to produce these items on demand reduces waste, lowers inventory costs, and ensures that products are found at exactly when needed. In the automotive and consumer electronics industries, on-demand production enables rapid prototyping and iterative design processes, allowing companies to bring new products to market faster and with greater agility. This trend also supports sustainability initiatives, as it reduces the need for mass production and the associated material waste and energy consumption. Moreover, on-demand production is fostering the growth of localized manufacturing, where products are produced closer to the point of use, reducing shipping costs and carbon emissions. As 3D printing technology continues to advance, particularly in terms of printing speed, material capabilities, and automation, the rise of on-demand production is expected to accelerate, offering significant advantages to companies in North America seeking to optimize their manufacturing processes and respond more effectively to changing market demands.
Integration of AI and Machine Learning in 3D Printing
The integration of artificial intelligence (AI) and machine learning (ML) into the 3D printing process is a growing trend that is set to enhance the capabilities and efficiency of the technology in North America. AI and ML are being increasingly utilized to optimize various aspects of 3D printing, from design and material selection to real-time process monitoring and quality control. One of the key benefits of integrating AI into 3D printing is the ability to automate the design process. AI-driven design software can generate optimized geometries that maximize the strength and performance of a printed object while minimizing material usage. This is particularly valuable in industries such as aerospace and automotive, where weight reduction is a critical factor. Additionally, AI can be used to predict and mitigate potential issues in the printing process, such as warping or layer adhesion problems, ensuring higher quality and more reliable end products. Machine learning algorithms, on the other hand, can analyze large datasets generated during the printing process to identify patterns and correlations that can be used to improve efficiency and consistency. For instance, ML can help optimize print settings for different materials and designs, leading to faster print times and reduced material waste. Moreover, the integration of AI and ML into 3D printing is enabling the development of more advanced and autonomous printing systems that require less human intervention. These systems can self-adjust in real-time based on feedback from sensors and cameras, ensuring optimal print quality. As AI and ML technologies continue to evolve, their integration into 3D printing is expected to drive significant improvements in speed, precision, and overall productivity, making the technology even more attractive to industries in North America.
Expansion of 3D Printing in Healthcare
The expansion of 3D printing in healthcare is a major trend in the North America market, driven by the technology's ability to produce highly customized and patient-specific medical devices, implants, and even biological tissues. The healthcare sector is increasingly adopting 3D printing for a wide range of applications, from creating anatomical models for surgical planning to producing custom prosthetics and orthotics. One of the most promising areas of growth is in the field of bioprinting, where living cells are printed layer by layer to create tissues and organs. While still in its early stages, bioprinting holds the potential to revolutionize organ transplantation by providing an alternative to donor organs, which are often in short supply. In the meantime, 3D printing is already making a significant impact by enabling the production of patient-specific implants, such as cranial plates, dental implants, and joint replacements, which are tailored to the exact anatomical structure of the patient. This customization improves the fit, function, and overall success of these implants, leading to better patient outcomes. Additionally, 3D printing is being used to produce personalized surgical instruments that are specifically designed for the anatomy of individual patients, making surgeries more precise and less invasive. The ability to quickly produce these customized devices also reduces lead times and costs, making advanced medical treatments more accessible. Furthermore, 3D printing is facilitating the development of innovative drug delivery systems, such as customized pills and implants that release medication at controlled rates. As the technology continues to advance and regulatory frameworks evolve, the expansion of 3D printing in healthcare is expected to accelerate, offering new possibilities for personalized medicine and improved patient care in North America.
Segmental Insights
Technology Insights
Stereolithography segment
One of the primary reasons for SLA’s dominance is its extensive use in industries like healthcare, automotive, aerospace, and consumer goods. In healthcare, SLA is favored for producing medical devices, dental implants, and anatomical models due to its high resolution and biocompatibility. The technology allows for the creation of patient-specific solutions, which is critical for personalized medicine. Additionally, in the dental industry, SLA’s accuracy and smooth surface finish make it ideal for fabricating crowns, bridges, and orthodontic devices.
The automotive and aerospace sectors also contribute significantly to SLA’s leading position. In these industries, rapid prototyping and the production of lightweight, high-performance parts are crucial. SLA offers the speed and accuracy needed for iterative design and testing processes, helping companies reduce time-to-market while maintaining product quality. The ability to produce complex components with fine details makes SLA an attractive choice for these sectors. Another factor driving SLA’s dominance is the continuous advancements in material science. A growing range of resins, including those with enhanced mechanical properties, temperature resistance, and transparency, are found at, making SLA suitable for an even broader range of applications. Moreover, the technology’s scalability and decreasing costs make it accessible not only to large corporations but also to small and medium-sized enterprises (SMEs) looking to leverage 3D printing.
Regional Insights
United States dominated the North America 3D Printing market in 2023
In healthcare, the U.S. leads in adopting 3D printing for personalized medical devices, prosthetics, and bioprinting applications. The country’s well-established healthcare system and regulatory framework, combined with a high level of investment in medical research, have positioned the U.S. as a leader in integrating 3D printing into clinical practices. Moreover, the U.S. benefits from a favorable business environment that encourages innovation and entrepreneurship. Significant venture capital funding and government grants are directed toward 3D printing startups and research initiatives, enabling rapid development and commercialization of new technologies. The country’s extensive network of universities and research institutions also plays a crucial role in advancing 3D printing through academic-industry collaborations. Additionally, the presence of a large consumer base with a growing demand for customized products further drives 3D printing adoption in industries like consumer electronics and fashion. This combination of technological leadership, industry adoption, and supportive infrastructure makes the United States the dominant force in the North America 3D printing market in 2023.
Recent Developments
- In January 2024, MFG announce that AMFG haspartnered with 3D Marc to integrate our Instant Quote Portal, a key step inscaling its Additive Manufacturing capabilities. With a deep engagement in 3Dprinting since 2000, Marc identified the technology’s potential to bringdiscontinued products back to life. Over the years, he developed advancedexpertise in design and optimized printing techniques, refining his skills inplatforms like AUTOCAD to deliver high-quality, precision-driven solutions fordiverse manufacturing needs.
- In June 2024, Materialise, a leading provider of 3Dprinting software and services, and ArcelorMittal Powders, a division ofArcelorMittal specializing in high-quality steel powders, signed a memorandumof understanding (MOU) to enhance laser powder bed fusion (LPBF) technology andmetal 3D printing processes. This strategic collaboration aims to developinnovative solutions to optimize LPBF equipment performance and streamlinemetal additive manufacturing workflows. As part of the agreement, ArcelorMittalwill leverage Materialise’s next generation build processor for 3D printers,enabling improved precision, efficiency, and reliability in metal partproduction.
- In May 2023, Fuji Corporation announced a strategicpartnership with J.A.M.E.S. GmbH to drive the advancement of additiveelectronics. Fuji has introduced the FPM Trinity, an innovative electronics 3Dprinter designed to revolutionize manufacturing by integrating resin substrateprinting, circuit printing, and component mounting in a single process. Thisall-in-one solution enables the complete 3D printing of electronic devices,streamlining production and enhancing efficiency. The collaboration with J.A.M.E.S.GmbH aims to accelerate the adoption of additive electronics by leveragingFuji’s cutting-edge technology to deliver fully integrated, high-performanceelectronic manufacturing capabilities.
Key Market Players
- Stratasys Ltd
- 3DSystems Corporation
- EOSGmbH
- General Electric Company
- SismaSpA
- ExOneOperating, LLC
- NikonSLM Solutions AG
- ProtoLabs, Inc.
- HPInc.
- NanoDimension Ltd.
- MaterialiseNV
- voxeljetAG
By Component | By Printer Type | By Technology | By Process | By Vertical | By Country |
|
|
|
|
|
|
Related Reports
- Decentralized Identity Market Size, By Identity Type (Biometrics, Non-Biometrics), By Enterprise Size (Large Enterprise,...
- Blockchain Identity Management Market Size - By Offering (Software, Service), By Provider Type (Application Provider, Mi...
- PayTV Market - By Technology (Cable TV, Satellite TV, Internet Protocol TV), By Subscription Type (Postpaid, Prepaid), ...
- Generative AI in Logistics Market - By Type (Variational Autoencoder (VAE), Generative Adversarial Networks (GANs), Recu...
- AI in Industrial Machinery Market - By Component (Hardware, Software, Services), By Technology (Machine Learning, Comput...
- Explainable AI Market Size - By Component (Solution, Service), By Software Service (Standalone Software, Integrated Soft...
Table of Content
To get a detailed Table of content/ Table of Figures/ Methodology Please contact our sales person at ( chris@marketinsightsresearch.com )
List Tables Figures
To get a detailed Table of content/ Table of Figures/ Methodology Please contact our sales person at ( chris@marketinsightsresearch.com )
FAQ'S
For a single, multi and corporate client license, the report will be available in PDF format. Sample report would be given you in excel format. For more questions please contact:
Within 24 to 48 hrs.
You can contact Sales team (sales@marketinsightsresearch.com) and they will direct you on email
You can order a report by selecting payment methods, which is bank wire or online payment through any Debit/Credit card, Razor pay or PayPal.
Discounts are available.
Hard Copy