Wind Turbine Rotor Blade Market – Global Industry Size, Share, Trends, Opportunity, and Forecast Segmented By Location of Deployment (Onshore and Offshore), Blade Material (Carbon Fiber, Glass Fiber, and Other Blade Materials), By Region, Competition, 2018-2028
Published Date: December - 2024 | Publisher: MIR | No of Pages: 320 | Industry: Power | Format: Report available in PDF / Excel Format
View Details Buy Now 2890 Download Sample Ask for Discount Request CustomizationForecast Period | 2024-2028 |
Market Size (2022) | USD 19.26 Billion |
CAGR (2023-2028) | 7.26% |
Fastest Growing Segment | Offshore |
Largest Market | Asia Pacific |
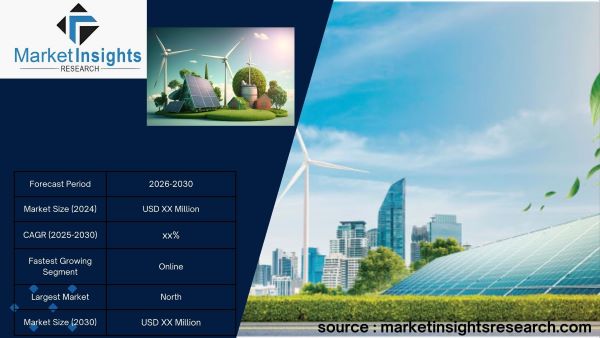
Market Overview
Global Wind Turbine Rotor Blade market was valued at USD 19.26 Billion in 2022 and is anticipated to project robust growth in the forecast period with a CAGR of 7.26% through 2028.
Key Market Drivers
Increasing Global Wind Energy Capacity will help with Wind Turbine Rotor Blade Market growth.
The increasing global wind energy capacity stands as a resounding beacon of hope in the pursuit of sustainable energy solutions. This pivotal factor acts as a major driver, propelling the growth and vibrancy of the global wind turbine rotor blade market. As nations worldwide grapple with the urgent need to address climate change, reduce greenhouse gas emissions, and transition away from fossil fuels, wind energy has emerged as a crucial player in this transformative journey. This growing global reliance on wind power generates a cascading demand for wind turbines, with their rotor blades serving as the vital heart of these towering clean energy giants. The very essence of wind energy hinges on the effectiveness of its energy-capturing mechanisms, and rotor blades play a pivotal role in this equation. Longer blades, equipped with advanced aerodynamics, enable turbines to harness more wind energy, increasing efficiency and energy output. As a result, manufacturers are compelled to continually innovate, pushing the boundaries of blade design and materials to ensure peak performance.
Governments around the world have recognized the incredible potential of wind energy and are offering incentives, subsidies, and favorable policies to promote its development. These initiatives translate into a vibrant marketplace for wind turbines and, consequently, bolster the wind turbine rotor blade market. Moreover, the soaring demand for wind energy underscores a broader commitment to a greener future. Nations have set ambitious renewable energy goals, making wind power a linchpin in these strategies. Rotor blades, being a central component of wind turbines, bear the weight of these aspirations, further stimulating market growth.
As economies of scale are achieved and manufacturing techniques continue to improve, the cost of wind energy production steadily declines. This cost competitiveness enhances the appeal of wind energy investments, thus perpetuating the need for rotor blades. In summary, the ever-increasing global wind energy capacity is a powerful force propelling the wind turbine rotor blade market forward. It reflects the collective global commitment to combating climate change and transitioning to cleaner energy sources. The relentless growth of wind power ensures a sustained demand for rotor blades, spurring innovation, and investment in this dynamic sector as we steer toward a more sustainable and eco-conscious energy landscape.
Advancements in Wind Turbine Technology Have Played a Crucial Role in The Growth of The Wind Turbine Rotor Blade Market
Advancements in wind turbine technology have emerged as a driving force behind the global wind turbine rotor blade market, reshaping the landscape of renewable energy production. These technological strides are pivotal in enhancing the efficiency, output, and overall viability of wind energy, with rotor blades at the forefront of these innovations. The evolution of wind turbine technology has led to the development of larger and more efficient turbines, equipped with longer rotor blades. Longer blades are instrumental in capturing more wind energy, significantly increasing energy generation and efficiency. This trend aligns with the industry's relentless pursuit of maximizing energy output while minimizing costs, making wind energy more competitive with other forms of electricity generation.
Furthermore, technological advancements have spurred the creation of more aerodynamic and durable rotor blade designs. These innovations reduce drag, allowing turbines to harness wind energy more effectively. Improved materials, such as composite materials and carbon fiber, have been incorporated into rotor blade construction, enhancing their strength and longevity while simultaneously reducing weight. This not only boosts the efficiency of energy conversion but also extends the lifespan of rotor blades, reducing maintenance costs and improving overall cost-effectiveness. Additionally, innovations in turbine control systems, sensors, and monitoring technologies enable turbines to adapt to changing wind conditions more efficiently. This not only maximizes energy capture but also extends the lifespan of rotor blades by mitigating wear and tear associated with adverse conditions.
As wind turbines become increasingly integrated into power grids, smart grid technology and advanced energy management systems play a vital role. These systems enhance the stability and reliability of wind energy production, ensuring that the energy generated by the advanced turbines and rotor blades can be seamlessly integrated into the broader energy infrastructure. In the backdrop of these advancements, governments, corporations, and investors are increasingly motivated to channel resources into wind energy projects. This investment not only spurs the deployment of cutting-edge wind turbines but also catalyzes further research and development in rotor blade technology. In conclusion, the continuous advancements in wind turbine technology are revolutionizing the global wind turbine rotor blade market. These innovations drive efficiency, reliability, and cost-effectiveness, positioning wind energy as a formidable player in the global energy mix. Rotor blades, as a linchpin of wind turbines, are at the vanguard of this transformation, ensuring that wind energy remains a sustainable and competitive solution in the pursuit of cleaner and more efficient power generation.
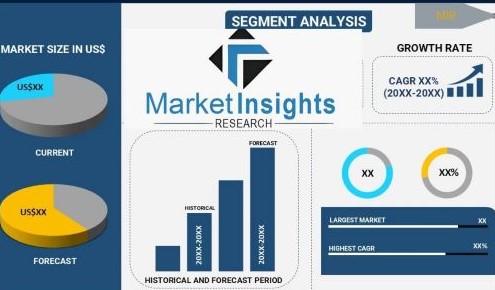
Key Market Challenges
Cost Pressure
Cost pressure is a significant and persistent challenge that has the potential to hamper the growth and development of the global wind turbine rotor blade market. This pressure emanates from various sources and can impact multiple aspects of the industry. First and foremost, the cost of manufacturing large rotor blades is substantial. These blades require specialized materials, intricate manufacturing processes, and stringent quality control measures, all of which contribute to high production costs. Additionally, the sheer size of these blades necessitates specialized transportation and installation equipment, further adding to the overall expenses.
As the wind energy industry strives for competitiveness with other energy sources, cost reduction becomes paramount. Governments, businesses, and consumers are increasingly cost-conscious, making it essential for wind turbine rotor blade manufacturers to find innovative ways to lower production costs. However, this can be a complex task, as reducing costs must not compromise the quality, durability, or efficiency of the blades, which are critical factors in wind energy generation. Furthermore, the competitive nature of the wind energy sector can exacerbate cost pressures. With numerous manufacturers vying for market share, there is a constant push to offer more cost-effective solutions. While competition can drive innovation, it can also lead to overcapacity and potential price wars, squeezing profit margins for rotor blade manufacturers.
Environmental considerations add another layer of complexity. Sustainable practices, materials, and disposal methods are increasingly important in response to environmental concerns. Balancing cost-effective production with eco-friendly processes can be challenging, as environmentally friendly alternatives may be more expensive. To address cost pressure effectively, industry stakeholders must focus on optimizing manufacturing processes, investing in research and development to create more cost-efficient materials, and streamlining logistics and transportation. Additionally, scaling up production to benefit from economies of scale can help mitigate cost pressures. Ultimately, successfully managing cost pressure is critical to ensuring that wind energy remains an economically viable and sustainable source of renewable power.
Logistics and Transportation
Logistics and transportation challenges represent a significant impediment that can hamper the growth and efficiency of the global wind turbine rotor blade market. These challenges stem from the sheer size and weight of rotor blades, along with the locations of wind farms and the need for specialized transportation and handling. First and foremost, rotor blades are colossal structures, often measuring more than 50 meters in length and weighing several tons. The transportation of these oversized components can be logistically daunting, requiring specialized equipment and careful planning. Roads, bridges, and infrastructure may need to be upgraded or reinforced to accommodate the massive dimensions of rotor blades, especially in rural or remote areas where wind farms are often located.
Moreover, many wind farms are established in remote or offshore locations, often far from manufacturing hubs. This geographical dispersion amplifies the logistics challenge. Transporting rotor blades over long distances, especially in the case of offshore wind farms, demands coordination among multiple stakeholders and modes of transportation, including ships, trucks, and sometimes even helicopters. Weather conditions can further complicate the transportation of rotor blades, particularly for offshore projects. Rough seas, strong winds, and adverse weather conditions can delay shipments, increase costs, and pose safety risks to personnel involved in transportation and installation.
To address these logistical and transportation hurdles, industry must continue to invest in innovative solutions. This includes the development of specialized transportation vessels designed to carry large rotor blades and the establishment of strategically located storage and distribution centers near wind farm sites. Additionally, improved route planning and coordination can optimize transportation processes and reduce delays. In summary, logistics and transportation challenges are formidable obstacles in the wind turbine rotor blade market. Overcoming these challenges is crucial not only to ensure the timely and cost-effective delivery of blades but also to support the continued expansion of wind energy, especially in remote and offshore locations where wind resources are abundant. Innovative approaches and infrastructure improvements are essential for mitigating these logistical constraints and ensuring the industry's long-term success.
Key Market Trends
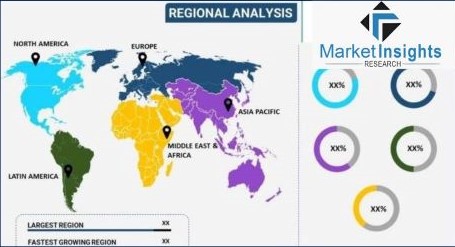
Increased Blade Length
The steady increase in wind turbine blade length is a compelling driver fueling the growth of the global wind turbine rotor blade market. This trend is underpinned by several critical factors that converge to make longer blades a cornerstone of wind energy's evolution. First and foremost, the elongation of wind turbine blades is closely tied to the pursuit of higher energy yields and greater efficiency. Longer blades, often measuring well over 50 meters in length, enable turbines to capture more wind energy across a larger swept area. This results in higher power generation, making wind farms more productive and economically viable. As governments and energy companies seek to maximize the energy output from each wind turbine, longer blades have become an essential solution.
Additionally, increased blade length contributes to the reduction of the levelized cost of energy (LCOE), a key metric in the wind energy sector. By capturing more wind energy with each rotation, wind turbines equipped with longer blades can generate electricity more efficiently, ultimately lowering the cost of producing renewable energy. Despite the many advantages, there are challenges to producing and deploying longer blades. Transportation and logistics become more complex, as these oversized components require specialized equipment and infrastructure. Manufacturing processes also demand precision and innovation to ensure the structural integrity and performance of extended blades.
In response to these challenges, manufacturers are continuously investing in research and development to create materials that are both lightweight and strong, optimizing blade designs for aerodynamic efficiency, and refining manufacturing techniques. As the demand for wind energy continues to grow globally, the trend toward increased blade length is expected to persist. It signifies not only a commitment to harnessing wind energy's full potential but also a driving force behind the ongoing transformation of the global energy landscape toward sustainability and reduced greenhouse gas emissions.
Offshore Wind Energy Expansion
The expansion of offshore wind energy is a prominent driver significantly propelling the global wind turbine rotor blade market. This dynamic trend reflects the world's increasing reliance on wind energy as a sustainable and reliable source of electricity, particularly in offshore environments. Offshore wind energy projects have gained momentum due to their numerous advantages. Offshore winds tend to be stronger and more consistent than onshore winds, leading to higher energy yields. To harness this potential, wind turbines installed offshore require larger rotor blades to capture and convert wind energy efficiently. Consequently, the offshore sector is driving substantial demand for specialized rotor blades designed to withstand the harsh marine environment.
This expansion is particularly evident in regions such as Europe, where countries are actively investing in offshore wind farms to meet renewable energy targets and reduce greenhouse gas emissions. Offshore wind projects in the North Sea, Baltic Sea, and the Atlantic Ocean are driving the need for longer and more durable rotor blades. To address the unique challenges of offshore installations, rotor blade manufacturers are developing innovative designs and materials. These blades must be corrosion-resistant, structurally robust, and capable of withstanding saltwater exposure and extreme weather conditions.
Moreover, the offshore wind sector is fostering advancements in floating wind turbine technology, opening up deeper waters for wind energy development. Floating turbines, often equipped with even larger rotor blades, are pushing the boundaries of offshore wind capacity, creating additional opportunities for rotor blade manufacturers. In summary, the expansion of offshore wind energy represents a powerful driver for the global wind turbine rotor blade market. As the offshore wind sector continues to grow and mature, it not only stimulates demand for specialized rotor blades but also fosters technological innovation, reinforcing wind energy's position as a vital contributor to the global renewable energy transition.
Segmental Insights
Location of Deployment
The market's largest contribution will be the onshore segment. The discovery of new oil and gas resources is helping the demand for onshore oilfield equipment. Oil and gas companies are focusing on exploring new oil and gas resources in order to meet the rising demand. Oil and gas drilling need oilfield equipment. They are therefore positioned at the gas or oil drilling hole. Oilfield equipment is widely utilised in onshore applications for pressure sealing of the whole casing employed in the relevant activity. Additionally, offshore oil and gas exploration and production activities offer a growing market growth potential that has the potential to be very profitable.
Regional Insights
Asia Pacific has established itself as the leader in the Global Wind Turbine Rotor Blade Market with a significant revenue share in 2022.
Asia-Pacific is one of the largest regions in the global wind turbine rotor blade market. Most of the demand is generated from China, India, and Japan. Since the invention of the modern wind turbine generator (WTG) in 1891, China has recognized that wind energy technology offers an effective way to provide electricity to rural and isolated areas. China's installed wind capacity grew from a mere 4 MW in 1990 to 338.30 GW in 2021 due to policy reforms, dedicated R&D initiatives, new financing mechanisms, and clear goals in the most recent Five-Year Plans. Both China's installed capacity and new capacity in 2021 were the largest in the world by a wide margin. According to IRENA, China is expected to continue to dominate the onshore wind power industry, with more than 50% of global installations by 2050. Also, due to the high population, high electricity demand in the country is expected to promote growth in wind energy. Several multinational corporations, including Chinese firms, are investing in this sector with the help of federal and provincial governments across the country. Therefore, factors, such as upcoming wind power projects, along with supportive government policies and regulations in different countries across the region, are expected to increase the demand for wind turbine rotor blades in the Asia-Pacific during the forecast period.
Recent Developments
- March 2022The
ZEBRA (Zero Waste Blade Research) consortium is a new step in the wind energy
industry’s transition to a circular economy with the production of its 100%
recyclable wind turbine prototype blade. The 62-meter blade was made using
Arkema’s Elium resin, a thermoplastic resin well known for its recyclable
properties, and the new high-performance Glass Fabrics from Owens Corning.
- March 2022
Hitachi Power Solutions will commence advanced services titled - Blade Total
Service. It is expected to mitigate the risks of wind power facilities,
including deterioration due to wear and tear of rotating blades, the stress
imposed by violent winds during typhoons, and damage caused by lightning — by
combining AI and other digital technologies with cutting-edge drone technology.
Key Market Players
- TPI
Composites Inc.
- Lianyungang
Zhongfu Lianzhong Composites Group Co. Ltd
- LM
Wind Power (a GE Renewable Energy business)
- Nordex
SE
- Siemens
Gamesa Renewable Energy, S.A.
- Vestas
Wind Systems A/S
- MFG
Wind
- Sinoma
wind power blade Co. Ltd
- Aeris
Energy
- Suzlon
Energy Limited
By Location of Deployment |
By Blade Material |
By Region |
|
|
Related Reports
- Industrial Electric Boiler Market - By Voltage Rating (Low Voltage, Medium Voltage), By Capacity (< 10 MMBtu/hr, 10-50 M...
- Biomass Boiler Market - By Feedstock (Woody Biomass, Agricultural Waste, Industrial Waste, Urban Residue), By Product (S...
- Asia Pacific Electric Boiler Market Size - By Capacity (≤ 10 MMBtu/hr, > 10 - 50 MMBtu/hr, > 50 - 100 MMBtu/hr, > 100 ...
- North America & Europe Electric Boiler Market Size - By Voltage Rating (Low Voltage, Medium Voltage), By Application (Re...
- North America Residential Boiler Market Size - By Fuel (Natural Gas, Oil, Electric), By Technology (Condensing {Natural ...
- U.S. Commercial Boiler Market – By Product (Hot Water, Steam), Application (Offices, Healthcare Facilities, Educationa...
Table of Content
To get a detailed Table of content/ Table of Figures/ Methodology Please contact our sales person at ( chris@marketinsightsresearch.com )
List Tables Figures
To get a detailed Table of content/ Table of Figures/ Methodology Please contact our sales person at ( chris@marketinsightsresearch.com )
FAQ'S
For a single, multi and corporate client license, the report will be available in PDF format. Sample report would be given you in excel format. For more questions please contact:
Within 24 to 48 hrs.
You can contact Sales team (sales@marketinsightsresearch.com) and they will direct you on email
You can order a report by selecting payment methods, which is bank wire or online payment through any Debit/Credit card, Razor pay or PayPal.
Discounts are available.
Hard Copy