Filling Equipment Market - Global Industry Size, Share, Trends, Opportunity, and Forecast, 2018-2028, Segmented By Sales Type (New Machinery and Spare Parts), By Process Type (Manual, Semi-automatic and Automatic), By Product Type (Solid, Semi-solid and Liquid), By End-user Industry (Food, Beverage, Pharmaceutical, Personal Care, Chemical and Others), By Region, and By Competition Forecast
Published Date: December - 2024 | Publisher: MIR | No of Pages: 320 | Industry: Power | Format: Report available in PDF / Excel Format
View Details Buy Now 2890 Download Sample Ask for Discount Request CustomizationForecast Period | 2024-2028 |
Market Size (2022) | USD 16.43 billion |
CAGR (2023-2028) | 3.89% |
Fastest Growing Segment | Liquid |
Largest Market | Asia Pacific |
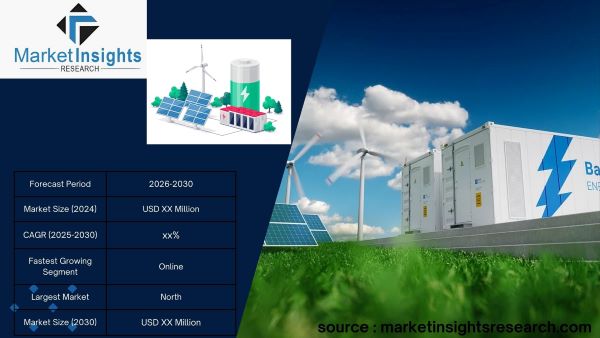
Market Overview
Global Filling Equipment Market has valued at USD 16.43 billion in 2022 and is anticipated to project robust growth in the forecast period with a CAGR of 3.89% through 2028. Filling equipment refers to the machinery used to fill various types of holding containers, such as boxes, bags, pouches, bottles, and more, with solid, semi-solid, and liquid items. The growing demand for consumable goods has prompted manufacturers to increase their production capacity. To meet this demand, manufacturers strive to provide accurate, consistent, and reliable equipment for filling consumable materials into containers like boxes, pouches, tubes, bottles, and others. This proactive approach anticipates the expansion of the filling equipment market throughout the forecast period.
Key Market Drivers
Increasing Demand for Packaged Beverages and Food Products
The global filling equipment market is witnessing substantial growth attributed to several key drivers, with one of the most notable being the rising demand for packaged beverages and food products. As consumer preferences evolve and urbanization continues to increase, there has been a significant shift towards convenience and ready-to-consume items. This shift has fueled the demand for various types of packaging, including bottles, cans, pouches, and cartons, all of which require efficient and accurate filling equipment.
One of the primary factors contributing to this driver is the changing lifestyle of consumers worldwide. As more individuals adopt fast-paced urban lifestyles, the demand for on-the-go food and beverages has surged. Packaged goods offer convenience and an extended shelf life, making them an appealing choice for consumers. Consequently, manufacturers face constant pressure to meet this demand, and filling equipment plays a crucial role in their production processes.
Furthermore, the global emphasis on sustainability has driven innovations in packaging materials and designs. Filling equipment manufacturers have adapted to meet the requirements of eco-friendly packaging, including lightweight containers and recyclable materials. This transition necessitates advanced filling equipment capable of handling diverse packaging types, sizes, and materials, further propelling market growth.
The ongoing COVID-19 pandemic has also expedited the demand for packaged products, as consumers increasingly prioritize sealed containers to minimize the risk of contamination. Filling equipment manufacturers have responded by developing technologies that enhance sanitation and hygiene during the filling process.
In conclusion, the escalating demand for packaged beverages and food products driven by shifting consumer preferences, urbanization, and sustainability concerns serves as a significant driver of the global filling equipment market. Manufacturers are investing in advanced filling equipment to meet the growing demand for a wide range of packaging formats while upholding high levels of product safety and quality.
Technological Advancements and Automation in Filling Equipment
Technological advancements and automation in filling equipment serve as significant drivers of the global filling equipment market. Over time, filling equipment has witnessed remarkable evolution from manual and semi-automatic machines to highly sophisticated, fully automated systems. This transition has played a pivotal role in enhancing efficiency, minimizing human errors, and augmenting production capacities across diverse industries, including pharmaceuticals, food and beverage, chemicals, and cosmetics.
A key technological advancement propelling this market is the development of precision filling technology. Modern filling machines leverage advanced sensors, control systems, and robotics to ensure precise and consistent filling levels. This level of precision is particularly crucial in industries where product quality, dosage accuracy, and compliance with regulatory standards are paramount, such as pharmaceuticals and healthcare.
Moreover, automation has become a defining characteristic of contemporary filling equipment. Automated filling systems are capable of performing multiple functions, including container handling, filling, capping, labeling, and quality control, with minimal human intervention. This not only improves production efficiency but also reduces labor costs and the risk of contamination, making it highly appealing to manufacturers.
The integration of Industry 4.0 principles has revolutionized filling equipment as well. Internet of Things (IoT) connectivity enables real-time monitoring and remote control of filling machines, facilitating predictive maintenance and data-driven decision-making. This enhances overall equipment effectiveness (OEE) and minimizes downtime, thereby boosting the return on investment for manufacturers.
Additionally, advancements in materials and design have led to more robust and hygienic filling equipment, meeting the stringent requirements of industries such as food and pharmaceuticals. The use of stainless steel and other corrosion-resistant materials, along with the development of easy-to-clean designs, ensures that filling equipment can maintain high levels of hygiene and meet the most stringent quality standards.
In conclusion, the continuous technological advancements and automation in filling equipment drive market growth by enhancing precision, efficiency, and versatility. Manufacturers across various industries are embracing these advanced systems to enhance their production processes and maintain competitiveness in the global market.
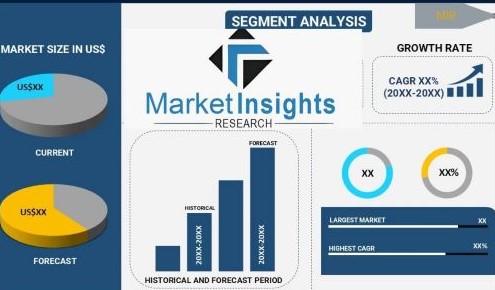
Growing Awareness of Environmental Sustainability
The global filling equipment market is witnessing substantial growth, primarily fueled by the increasing awareness of environmental sustainability. As environmental concerns intensify, both businesses and consumers are actively seeking ways to reduce their carbon footprint and minimize waste. This shift in mindset directly impacts the packaging and filling industry, driving the adoption of more eco-friendly practices and materials.
One of the key driving forces behind this transformation is the global plastic pollution crisis. Single-use plastic packaging has faced significant scrutiny, leading to regulatory changes and consumer demands for more sustainable packaging solutions. In response, filling equipment manufacturers have developed machinery capable of handling alternative packaging materials, such as glass, paper, and recyclable plastics. This adaptation allows companies to transition away from traditional single-use plastics towards more environmentally friendly options.
Moreover, minimizing product waste during the filling process is a crucial consideration. Modern filling equipment is meticulously designed to minimize overfill and spillage, ensuring efficient and accurate dispensing into containers. This not only reduces material waste but also lowers production costs for manufacturers.
The demand for energy-efficient filling equipment is also witnessing an upward trend. Manufacturers are developing equipment with improved energy efficiency and reduced resource consumption. Energy-efficient filling equipment not only lowers operational costs but also aligns with sustainability goals by reducing energy consumption and greenhouse gas emissions.
Additionally, filling equipment is being designed with ease of recycling and disposal in mind, embracing a cradle-to-cradle approach. This ensures that the entire lifecycle of the packaging and filling process remains environmentally responsible.
In conclusion, the increasing awareness of environmental sustainability is driving the global filling equipment market, as manufacturers and consumers prioritize eco-friendly packaging materials, waste reduction, and energy efficiency. Filling equipment plays a pivotal role in supporting these sustainability initiatives and is expected to continue growing in significance as sustainability remains a top global priority.
Key Market Challenges
Regulatory Compliance and Quality Assurance
One of the primary challenges faced by the global filling equipment market is the stringent regulatory landscape and the imperative for unwavering quality assurance. Industries heavily reliant on filling equipment, such as pharmaceuticals, food and beverage, and chemicals, must adhere to rigorous regulatory requirements enforced by government agencies such as the FDA (Food and Drug Administration) in the United States, the European Medicines Agency (EMA), and various other international regulatory bodies.
These regulations govern critical aspects including product safety, quality, and traceability. Ensuring that filling equipment complies with these stringent standards is a complex and costly process for manufacturers. Each equipment must undergo meticulous design, testing, and validation to meet the required regulatory criteria. Any deviation from these standards can lead to severe penalties, product recalls, or even legal consequences.
Another significant challenge lies in quality assurance. Maintaining consistent product quality, accurate filling levels, and contamination-free processes is of utmost importance, particularly in industries like pharmaceuticals where patient safety is at stake. Any malfunction or deviation in the performance of filling equipment can result in faulty products, recalls, and reputational damage for a company.
Furthermore, as regulations continue to evolve and become more stringent, filling equipment manufacturers must make substantial investments in research and development to keep pace with these changes. Adapting equipment to meet new requirements can be a time-consuming and costly endeavor, posing significant challenges for manufacturers in the global market.
Cost of Equipment and Installation
One of the key challenges encountered by the global filling equipment market is the substantial expense associated with equipment and installation. Manufacturing filling machines can be quite costly, especially when specialized features are required to meet industry-specific demands. Moreover, integrating and installing filling equipment into existing production lines can prove to be a complex and expensive endeavor.
The cost of filling equipment can vary significantly based on factors such as capacity, technology, and industry-specific customization. For instance, pharmaceutical-grade filling equipment often necessitates the use of specialized materials, precise engineering, and compliance with stringent regulatory standards, all of which contribute to higher costs.
Furthermore, the expenses related to installation and commissioning should not be underestimated. The integration of filling equipment into an existing production line may require modifications, additional infrastructure, and personnel training to ensure effective operation. These additional costs can significantly impact the overall cost of ownership, posing a significant challenge for manufacturers looking to invest in and adopt new filling equipment.
Additionally, small and medium-sized enterprises (SMEs) may face particular difficulties in affording advanced filling equipment, which can limit their ability to compete with larger industry players. This can result in market disparities and impede innovation within certain sectors.
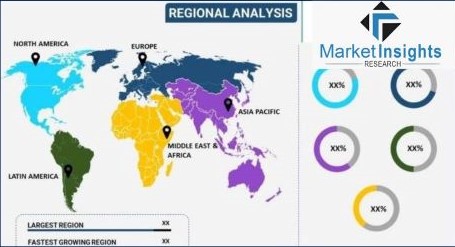
Maintenance and Downtime
Maintenance and downtime present ongoing challenges for the global filling equipment market. Filling equipment, like any machinery, necessitates regular maintenance for optimal performance and durability. However, maintenance can be time-consuming and costly, often involving production line shutdowns and resource allocation for equipment inspection, repair, and cleaning.
Unplanned downtime resulting from equipment failures or malfunctions is a significant concern for manufacturers. Downtime can lead to production delays, missed deadlines, and financial losses. Therefore, minimizing downtime and optimizing equipment reliability remains a top priority.
Predictive maintenance, leveraging data and sensors to forecast maintenance needs, has emerged as a solution to address this challenge. However, implementing predictive maintenance systems can be intricate and costly, particularly for older filling equipment lacking necessary sensors and connectivity features.
Furthermore, global supply chain disruptions witnessed in recent years have further exacerbated maintenance challenges. Obtaining replacement parts and skilled technicians promptly has become increasingly difficult, consequently raising the risk of extended downtime.
In conclusion, regulatory compliance and quality assurance, the high cost of equipment and installation, and maintenance and downtime are three significant challenges facing the global filling equipment market. Overcoming these challenges requires continuous investment in research and development, technological innovation, and efficient maintenance strategies to ensure sustained growth and competitiveness within the industry.
Key Market Trends
Automation and Industry 4.0 Integration
One of the notable trends in the global filling equipment market is the growing adoption of automation and Industry 4.0 technologies. Automation has emerged as a key driver in manufacturing, enabling companies to enhance efficiency, reduce labor costs, and improve product quality. In the context of filling equipment, automation encompasses various aspects, including the filling process itself, container handling, capping, labeling, and quality control.
Filling machines are now equipped with advanced sensors, robotics, and machine learning algorithms to optimize filling precision, minimize waste, and ensure consistent product quality. These intelligent filling machines can automatically adjust filling levels, monitor product viscosity, and detect any deviations, thereby reducing human intervention and errors.
Moreover, the integration of Industry 4.0 is transforming filling equipment into interconnected and data-driven systems. Internet of Things (IoT) sensors and cloud-based platforms enable real-time monitoring and remote control of filling equipment, enhancing predictive maintenance capabilities and providing valuable insights into production performance. Manufacturers can analyze data to optimize production processes, minimize downtime, and maximize overall equipment effectiveness (OEE).
This trend holds particular significance in industries such as pharmaceuticals and food processing, where precision and consistency are of utmost importance. As filling equipment becomes more intelligent and interconnected, manufacturers can meet the growing demand for customized products, smaller batch sizes, and rapid changeovers while upholding high levels of quality and efficiency.
Sustainable Packaging Solutions
The global shift towards sustainability is significantly impacting the filling equipment market, resulting in a notable trend towards sustainable packaging solutions. Both consumers and regulatory bodies are emphasizing the importance of reducing plastic waste and minimizing the environmental impact of packaging materials. In response, filling equipment manufacturers are developing machinery capable of handling eco-friendly and recyclable packaging materials.
A noteworthy aspect of this trend is the resurgence of glass as a preferred packaging material. Glass containers offer infinite recyclability and present an appealing option for various products, including beverages, cosmetics, and pharmaceuticals. Consequently, there is a high demand for filling equipment specifically designed to handle glass bottles and jars, particularly from premium and environmentally conscious brands.
Furthermore, filling equipment is being adapted to accommodate alternative packaging materials such as paper-based cartons, biodegradable plastics, and plant-based materials. These sustainable packaging options necessitate specialized filling equipment capable of handling diverse materials while ensuring product integrity.
Moreover, filling equipment manufacturers are incorporating features that minimize material waste during the filling process. Through precision filling and accurate dosing, overfill and spillage are minimized, contributing to more efficient and sustainable production practices. The drive towards sustainable packaging is not solely motivated by consumer preferences but also by the necessity to comply with increasingly stringent regulatory standards pertaining to environmental impact and waste reduction.
Segmental Insights
Sales Type Insights
The New Machinery segment emerged as the dominant player in 2022. Technological advancements, such as robotics, machine learning, and IoT connectivity, have been seamlessly integrated into filling machinery to optimize efficiency, accuracy, and data-driven decision-making. The incorporation of quick changeover features and modular designs enables operators to effortlessly switch between various products and packaging formats, minimizing downtime.
Moreover, sustainability features have been intricately woven into the design of filling machinery, ensuring reduced material waste and enhanced energy efficiency during the filling process. The burgeoning demand for specialized filling machinery capable of handling complex formulations and vial formats, propelled by the rise of personalized medicine and biopharmaceuticals, has prompted the machinery segment to develop innovative filling solutions that cater to different viscosities, temperatures, and stringent sanitary requirements.
In addition, machinery manufacturers have recognized the significance of providing comprehensive after-sales services, encompassing maintenance, spare parts, and technical support. These services are instrumental in guaranteeing the sustained reliability and longevity of filling equipment. By offering training and technical expertise to customers, manufacturers further enhance customer satisfaction and foster long-term loyalty.
In conclusion, the new machinery segment of the global filling equipment market is characterized by rapid technological advancements, customization, sustainability, and a diverse range of applications across industries. In order to thrive in this competitive and dynamic segment, manufacturers must remain attuned to industry trends, customer demands, and regional dynamics.
Process Type Insights
The Automatic segment is projected to experience rapid growth during the forecast period. The segment of automatic filling equipment in the global market offers precise and efficient solutions to cater to various industries such as pharmaceuticals, food and beverage, cosmetics, and chemicals. Manufacturers in this segment must maintain agility, adaptability, and customer focus to thrive in this dynamic and competitive industry.
Continuous investments in technologies like servo-driven filling systems, advanced sensors, and robotics enable manufacturers to achieve accurate dosing and minimize product waste. Industries like cosmetics rely on automatic equipment to efficiently meet production targets, especially for repetitive tasks such as filling bottles with skincare products.
Modular and versatile automatic filling machines can easily adapt to changing production requirements, minimizing downtime associated with equipment reconfiguration. Moreover, these machines can be customized to work with sustainable packaging materials, including recyclable plastics and glass.
In the pharmaceutical industry, strict regulatory compliance is of utmost importance. Automatic filling equipment in this segment is meticulously engineered to meet stringent regulatory standards, ensuring product safety, sterility, and compliance with Good Manufacturing Practices (GMP). Key features like clean-in-place (CIP) and sterilization-in-place (SIP) systems are seamlessly integrated into pharmaceutical-grade automatic filling machines.
Regional Insights
Asia Pacific emerged as the dominant player in 2022, holding the largest market share. The Asia-Pacific region is a dynamic and diverse market for filling equipment, characterized by rapid growth, regulatory diversity, technological advancements, and shifting consumer preferences. Filling equipment manufacturers must adapt to these regional dynamics and seize opportunities by offering tailored solutions and staying attuned to market trends in this dynamic and evolving market.
The Asia-Pacific region is one of the largest and fastest-growing markets for filling equipment globally. This growth is driven by factors such as population expansion, urbanization, and rising disposable incomes, which increase the demand for packaged goods, including beverages, food products, pharmaceuticals, and cosmetics. The Asia-Pacific region hosts a wide range of industries that rely on filling equipment, including food and beverage, pharmaceuticals, chemicals, cosmetics, and more. Each of these industries has distinct requirements and regulations, necessitating a versatile range of filling equipment solutions.
Asia-Pacific countries have varying regulatory frameworks for the manufacturing and packaging of products. Companies operating in multiple countries must navigate these diverse regulatory landscapes, including safety, quality, labeling, and environmental regulations. The adoption of advanced filling equipment technologies, such as automation, robotics, and Industry 4.0 integration, is on the rise in the Asia-Pacific region. This trend is driven by the need to improve production efficiency, reduce labor costs, and meet quality standards.
While countries like China and India dominate the Asia-Pacific market, emerging economies across Southeast Asia, such as Vietnam, Indonesia, and Thailand, are experiencing rapid industrialization and urbanization. These countries present untapped opportunities for filling equipment suppliers as their manufacturing sectors expand.
Recent Developments
In 2022, GEA Group Aktiengesellschaft unveiled the state-of-the-art GEA DairyFeed 4500, an autonomous feeding robot equipped with cutting-edge sensors. Developed based on GEA's extensive 35 years of experience in the feeding industry, the innovative GEA DairyFeed F4500 operates autonomously and utilizes advanced sensor technology to minimize feed waste. This not only conserves valuable resources such as time and money but also enhances overall efficiency.
Moreover, in the same year, GEA Group Aktiengesellschaft launched highly adaptable CO2 capture facilities for small and medium-sized enterprises. These facilities allow clients to produce CO2 from various exhaust gas compositions, including carbonates, amines, and ammonia. This demonstrates GEA's commitment to providing versatile solutions to meet the diverse needs of its customers.
Key Market Players
- Salzgitter AG (KHS Group)
- Tetra Laval International S.A.
- Ronchi Mario S.p.A
- Bettcher Industries, Inc.
- Coesia S.p.A
- Scholle IPN
- Krones AG
- Accutek Packaging Equipment Companies,
Inc.
- Syntegon Technology GmbH
- GEA Group Aktiengesellschaft
By Sales Type |
By Process Type |
By Product Type |
By End-user Industry |
By Region |
|
|
|
|
|
Related Reports
- Biomass Boiler Market - By Feedstock (Woody Biomass, Agricultural Waste, Industrial Waste, Urban Residue), By Product (S...
- Asia Pacific Electric Boiler Market Size - By Capacity (≤ 10 MMBtu/hr, > 10 - 50 MMBtu/hr, > 50 - 100 MMBtu/hr, > 100 ...
- North America & Europe Electric Boiler Market Size - By Voltage Rating (Low Voltage, Medium Voltage), By Application (Re...
- North America Residential Boiler Market Size - By Fuel (Natural Gas, Oil, Electric), By Technology (Condensing {Natural ...
- U.S. Commercial Boiler Market – By Product (Hot Water, Steam), Application (Offices, Healthcare Facilities, Educationa...
- North America Commercial Boiler Market Size - By Fuel (Natural Gas, Oil, Coal, Electric), By Capacity, By Technology (Co...
Table of Content
To get a detailed Table of content/ Table of Figures/ Methodology Please contact our sales person at ( chris@marketinsightsresearch.com )
List Tables Figures
To get a detailed Table of content/ Table of Figures/ Methodology Please contact our sales person at ( chris@marketinsightsresearch.com )
FAQ'S
For a single, multi and corporate client license, the report will be available in PDF format. Sample report would be given you in excel format. For more questions please contact:
Within 24 to 48 hrs.
You can contact Sales team (sales@marketinsightsresearch.com) and they will direct you on email
You can order a report by selecting payment methods, which is bank wire or online payment through any Debit/Credit card, Razor pay or PayPal.
Discounts are available.
Hard Copy