Forecast Period | 2025-2029 |
Market Size (2023) | USD 1.24 Billion |
CAGR (2024-2029) | 4.25% |
Fastest Growing Segment | Automotive |
Largest Market | North America |
Market Size (2029) | USD 1.60 Billion |
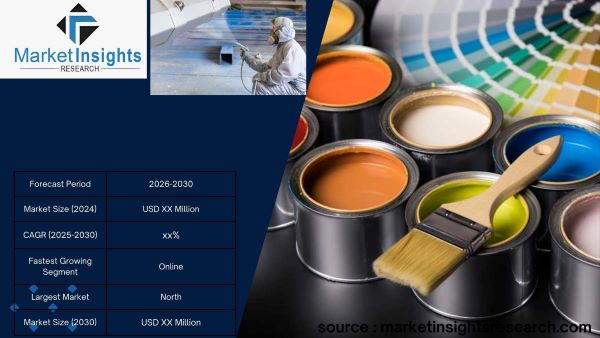
Market Overview
Global Cold Gas Spray Coatings Market was valued at USD 1.24 Billion in 2023 and is anticipated to project steady growth in the forecast period with a CAGR of 4.25% through 2029. In the realm of advanced surface engineering technologies, Cold Gas Spray (CGS) coatings have emerged as a transformative force, offering unique advantages across various industries
Key Market Drivers
Demand in Aerospace Industry
The aerospace industry, with its relentless pursuit of technological advancements, has become a primary catalyst for the remarkable growth of the global cold gas spray coatings market. This innovative coating technology has found its wings in aerospace applications, proving to be a game-changer in enhancing the performance, durability, and efficiency of critical aircraft components.
One of the key drivers of cold gas spray coatings in the aerospace sector is the emphasis on weight reduction. As the industry grapples with the challenge of improving fuel efficiency and reducing emissions, every ounce saved becomes critical. Cold gas spray coatings offer a lightweight alternative without compromising on strength and protective capabilities, contributing significantly to the overall fuel efficiency of aircraft.
Electronics Industry Growth
The rapid expansion of the electronics industry has become a driving force behind the remarkable surge in demand for cold gas spray coatings. This sophisticated coating technology has found a burgeoning market within the electronics sector, where the pursuit of miniaturization, enhanced performance, and robust protection of electronic components is paramount.
The electronics industry is synonymous with the constant quest for smaller, more powerful devices. Cold gas spray coatings offer a solution by providing a protective layer that not only shields components from environmental factors but also enhances their conductivity. This is especially crucial in the era of miniaturization, where every nanometer matters in the performance of electronic devices.
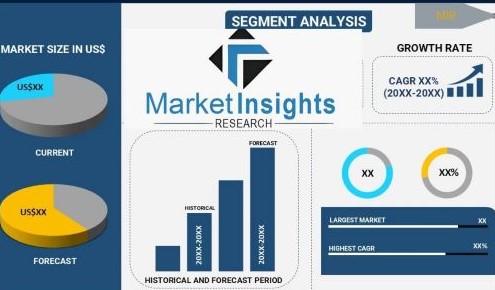
Manufacturing Efficiency
In the realm of manufacturing, where efficiency is a cornerstone, Cold Gas Spray (CGS) coatings have emerged as a transformative technology. This sophisticated coating method is increasingly becoming a driving force behind the global push for enhanced manufacturing efficiency.
Manufacturers are increasingly turning to CGS coatings to extend the operational life of their equipment. By applying durable and wear-resistant coatings to critical components, industries can enhance the reliability of machinery, resulting in fewer breakdowns and increased productivity.
Key Market Challenges
Technological Complexity
Cold Gas Spray coatings involve a precise and intricate process wherein finely powdered coating materials are accelerated to supersonic speeds and deposited onto a substrate. While the technology offers unparalleled benefits, including reduced thermal stress and superior coating adhesion, its intricacies pose challenges for widespread adoption.
Implementing CGS coatings necessitates a skilled workforce capable of operating and maintaining the specialized equipment. The training curve for technicians and operators introduces challenges, particularly in industries where traditional coating methods are prevalent.
Material Compatibility
Material compatibility in the CGS coatings market refers to the harmonious interaction between the coating material and the substrate it is applied to. Achieving compatibility is essential to unlock the full potential of CGS technology, offering benefits such as enhanced wear resistance, corrosion protection, and improved performance of coated components.
Achieving optimal adhesion and bonding between the coating material and the substrate is crucial. Material compatibility issues can lead to poor adhesion, compromising the durability and effectiveness of the coating.
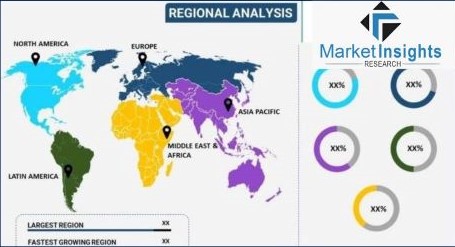
Key Market Trends
Increased Demand for Sustainable Solutions
Industries across the board are reevaluating their practices, with a heightened awareness of environmental impact. This shift is notably pronounced in coating technologies, where traditional methods often involve environmentally harmful processes and materials. In this context, the CGS coatings market is emerging as a frontrunner in providing sustainable alternatives.
Industries with stringent performance requirements, such as aerospace and defense, are embracing CGS coatings for their sustainable attributes. The coatings offer lightweight solutions without compromising on durability and protection, aligning with the sustainability goals of these high-profile sectors.
Standardization Efforts
In the realm of surface engineering, where precision and consistency are paramount, standardization efforts are playing a pivotal role in driving the Cold Gas Spray (CGS) coatings market. As industries recognize the transformative potential of CGS technology, standardization initiatives are emerging as key drivers for its widespread adoption and sustained growth.
One of the primary challenges in the CGS coatings market has been the variability in outcomes due to differences in processes and parameters. Standardization efforts seek to address this challenge by defining clear guidelines for coating processes, material specifications, and performance expectations. This not only enhances the quality of coatings but also simplifies the integration of CGS technology into diverse industries.
Segmental Insights
Technology Insights
Based on Technology,
End Use Insights
Based on End Use,
Regional Insights
Based on Region,
Recent Developments
- In March 2023, Linde, an industrial gases and engineering company, unveiled Linspray® Connect, a novel gas delivery system tailored for Cold Spray Additive Manufacturing. Developed in collaboration with Germany's Impact Innovations, this solution aims to enhance the reliability and safety of the Cold Spray AM process. During Cold Spray AM, metal powders ranging from 5 to 50 microns are propelled onto a substrate using high-pressure gases. The powder, initially at ambient temperatures, is introduced into a nitrogen or helium gas stream, which is then heated and accelerated through a supersonic nozzle at velocities ranging from 500 to 1200 meters per second. Despite the intense process, the metal powder's temperature remains well below its melting point, ensuring the particles retain their solid state, distinctive properties, and resistance to oxidation. The resulting coating is ductile, mitigating any risk of embrittlement under stress.
Key Market Players
- Hannecard Roller Coatings, Inc.
- Bodycote plc
- Flame Spray Technologies BV
- VRC Metal Systems, LLC
- CenterLine (Windsor) Limited
- WWG Engineering Pte. Ltd.
- Praxair, Inc.
- Impact Innovations GmbH
- Concurrent Technologies Corporation
By Technology
|
By End Use
|
By Region
|
- High Pressure
- Low Pressure
|
- Automotive
- Aerospace
- Electrical and Electronics
- Oil and Gas
- Medical
- Utility
- Others
|
- North America
- Europe
- Asia Pacific
- South America
- Middle East & Africa
|