Organosheet and Semi-Finished Thermoplastic UD-Tape Laminate Market - Global Industry Size, Share, Trends, Opportunity, and Forecast, Segmented By Product (Organosheet, UD-Tape Laminate), By Application (Aerospace and Defense, Automotive, Sports and Leisure, Construction, Others), By Region and Comp
Organosheet and Semi-Finished Thermoplastic UD-Tape Laminate Market - Global Industry Size, Share, Trends, Opportunity, and Forecast, Segmented By Product (Organosheet, UD-Tape Laminate), By Application (Aerospace and Defense, Automotive, Sports and Leisure, Construction, Others), By Region and Competition, 2019-2029F
Published Date: December - 2024 | Publisher: MIR | No of Pages: 320 | Industry: Chemicals | Format: Report available in PDF / Excel Format
View Details Buy Now 2890 Download Free Sample Ask for Discount Request CustomizationForecast Period | 2025-2029 |
Market Size (2023) | USD 495.52 million |
CAGR (2024-2029) | 4.05% |
Fastest Growing Segment | UD-Tape Laminate |
Largest Market | Asia Pacific |
Market Size (2029) | USD 621.62 million |
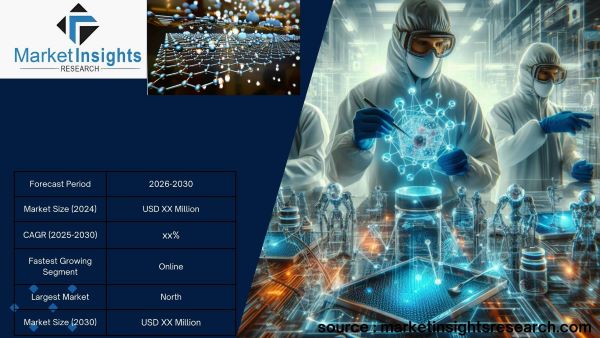
Market Overview
Global Organosheet and Semi-Finished Thermoplastic UD-Tape Laminate Market was valued at USD 495.52 million in 2023 and is anticipated to project robust growth in the forecast period with a CAGR of 4.05% through 2029.
The aerospace and defense industries are significant contributors to the demand for organosheet and UD-tape laminate materials. These sectors necessitate lightweight materials with exceptional mechanical properties, fatigue resistance, and impact resilience for applications including aircraft interiors, structural elements, and military vehicles. Organosheets and UD-tape laminates offer distinct advantages in terms of weight reduction, design flexibility, and ease of processing, making them highly desirable for aerospace and defense applications.
The renewable energy sector is a key driver of growth in the organosheet and semi-finished thermoplastic UD-tape laminate market. These materials are increasingly utilized in wind turbine blades, solar panels, and other renewable energy infrastructure due to their lightweight nature, durability, and resistance to corrosion. Organosheets and UD-tape laminates enable the construction of larger and more efficient wind turbines and solar panels, thereby contributing to the expansion of renewable energy capacity globally.
The sports and leisure industry represents another significant market for organosheet and UD-tape laminate materials. These advanced materials are employed in the production of high-performance sporting equipment such as bicycles, tennis rackets, golf clubs, and snowboards. Organosheets and UD-tape laminates offer superior strength-to-weight ratios, impact resistance, and vibration damping properties, thereby enhancing the performance and longevity of sporting gear.
Beyond their application in various industries, organosheet and semi-finished thermoplastic UD-tape laminates are also fostering innovation in manufacturing processes and material formulations. Manufacturers are heavily investing in research and development efforts to optimize material properties, improve processing capabilities, and explore new applications for these cutting-edge composite materials.
Key Market Drivers
Growing Demand of Organosheet and Semi-Finished Thermoplastic UD-Tape Laminate in Automotive Industry
The automotive sector is increasingly prioritizing advancements in fuel efficiency and emissions reduction to adhere to regulatory standards and cater to consumer preferences for environmentally friendly vehicles. Organosheets and thermoplastic UD-tape laminates present substantial weight reductions compared to conventional materials like metals and thermoset composites.
These advanced materials boast superior mechanical attributes, including impressive strength-to-weight ratios, resistance to impacts, and fatigue performance. This characteristic allows car manufacturers to engineer vehicles with heightened safety, resilience, and operational capabilities. Their inherent adaptability in design facilitates the creation of intricate shapes, contours, and configurations, enabling innovative and streamlined vehicle designs that optimize both performance and efficiency.
Beyond their performance advantages, organosheets and thermoplastic UD-tape laminates offer economic benefits and efficiency enhancements for automotive producers. These materials can undergo processing through standard thermoplastic manufacturing methods such as injection molding, compression molding, and thermoforming, thereby reducing production timelines and expenses in comparison to traditional composite materials. The capacity to consolidate numerous components into a single part using organosheets and UD-tape laminates further diminishes assembly costs and streamlines manufacturing procedures.
Growing Demand of Organosheet and Semi-Finished Thermoplastic UD-Tape Laminate in Construction Industry
Organosheet and semi-finished thermoplastic UD-tape laminate are highly valued for their exceptional structural performance, making them ideal for a wide range of construction applications. These materials exhibit remarkable stiffness, resistance to impacts, and fatigue strength, enabling the construction of resilient yet lightweight structures such as bridges, tunnels, facades, and roofing systems. Utilizing organosheet and UD-tape laminate empowers engineers and architects to devise innovative and sustainable structures capable of withstanding environmental challenges and meeting rigorous safety regulations.
A significant catalyst driving the increasing demand for organosheet and semi-finished thermoplastic UD-tape laminate in the construction sector is their versatility and adaptability in design. These materials can be molded into diverse shapes and configurations, facilitating the realization of intricate architectural designs and bespoke building components. Whether crafting curved facades or intricate structural elements, organosheet and UD-tape laminate provide architects and designers the flexibility to explore novel possibilities and redefine conventional construction methodologies.
Organosheet and semi-finished thermoplastic UD-tape laminate offer cost-efficient solutions for construction projects by optimizing material utilization and reducing overall expenses. Despite their lightweight nature, these materials exhibit exceptional durability, resulting in decreased transportation and installation costs compared to conventional building materials like steel and concrete. The use of automated manufacturing processes for fabricating organosheet and UD-tape laminate contributes to further cost reductions and shortened lead times, making them an appealing choice for construction firms seeking efficient and economical building solutions.
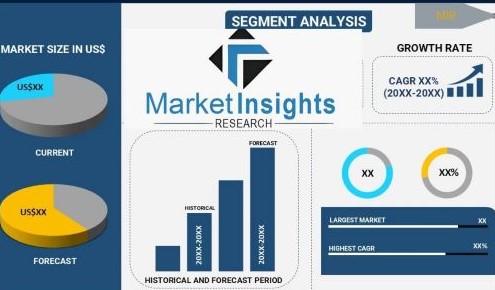
Key Market Challenges
Complex Manufacturing Processes
One of the key hurdles encountered in the production of organosheets and semi-finished thermoplastic UD-tape laminates is the necessity for meticulous precision throughout the manufacturing process. These materials demand exacting control over variables such as temperature, pressure, and alignment of reinforcing fibers during both the impregnation and consolidation stages. Any deviation from the prescribed parameters can lead to flaws like voids, misaligned fibers, or delamination, compromising the structural robustness and performance of the end product.
The manufacturing process of organosheets and UD-tape laminates entails intricate layering and stacking of thermoplastic matrices and reinforcing fibers to attain the desired mechanical attributes and structural resilience. Ensuring uniform dispersion and alignment of reinforcing fibers within the thermoplastic matrix is crucial for securing optimal strength and durability of the composite material. Maintaining consistent layering and stacking across extensive surface areas or intricate geometries presents challenges in upholding uniformity and quality throughout the production process.
The production of organosheets and semi-finished thermoplastic UD-tape laminates entails subjecting the material to heat and pressure to consolidate the thermoplastic matrix and reinforcing fibers into a cohesive structure. Effectively managing temperature and pressure parameters during both the heating and consolidation phases is imperative to achieve appropriate resin flow, fiber impregnation, and consolidation without introducing defects or voids into the final product. Ensuring precise control over temperature differentials and pressure distribution across expansive surface areas or intricate shapes can be demanding and necessitates sophisticated equipment and meticulous process refinement.
Key Market Trends
Rapid Prototyping and Digitalization
Rapid prototyping, also referred to as additive manufacturing or 3D printing, has revolutionized the production process of organosheet and semi-finished thermoplastic UD-tape laminates. This cutting-edge method enables the swift and cost-effective development of prototypes using computer-aided design (CAD) data. Manufacturers can now rapidly iterate and refine their designs, significantly reducing time-to-market and overall development expenses. Rapid prototyping facilitates the creation of intricate geometries and bespoke components, unlocking novel avenues for design enhancement and product innovation.
Digitalization encompasses a broader array of technologies, spanning digital twin simulations, advanced modeling software, and data-driven analytics. By harnessing digital tools and platforms, manufacturers can streamline their production workflows, bolster quality assurance, and optimize resource allocation. Real-time monitoring and predictive maintenance capabilities empower proactive decision-making, minimizing downtime and maximizing operational efficiency. Digitalization fosters seamless collaboration across global supply chains, enabling agile responses to market dynamics and demands.
The convergence of rapid prototyping and digitalization stands out as a pivotal trend in the global organosheet and semi-finished thermoplastic UD-tape laminate market. Manufacturers are increasingly embracing these technologies to maintain a competitive edge and fulfill evolving customer expectations. Across various sectors including automotive, aerospace, consumer electronics, and sporting goods, there is a growing demand for lightweight, high-performance materials, propelling the adoption of advanced manufacturing methodologies.
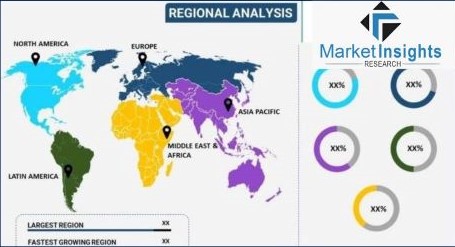
Segmental Insights
Product Insights
Based on the category of product, the UD-tape laminate
With its impressive strength-to-weight ratio, UD-tape laminate proves highly suitable for lightweight construction purposes. Substituting conventional materials like metal and concrete with UD-tape laminate enables manufacturers to decrease the overall weight of structures and vehicles, thereby enhancing fuel efficiency, performance, and sustainability.
Application Insights
The aerospace and defense segment is projected to experience rapid growth during the forecast period.
Regional Insights
Asia Pacific emerged as the dominant player in the Global Organosheet and Semi-Finished Thermoplastic UD-Tape Laminate Market in 2023, holding the largest market share in terms of value.
Asia Pacific boasts a formidable and varied manufacturing landscape, with well-established sectors in automotive, aerospace, and electronics. These industries stand as significant consumers of organosheets and UD-tape laminate, utilizing them in diverse applications such as lightweight automotive parts, aerospace components, and electronic casings. The region's robust manufacturing capacities serve as a catalyst for the increased demand for advanced composite materials like organosheets and UD-tape laminate.
Recent Development
- In June 2023, Avient Corporation and BASF collaborated to introduce colored variations of Organosheet and Semi-Finished Thermoplastic UD-Tape Laminate to the global market. These colored grades feature BASF’s Ultrason polyarylethersulfones (PAES) as the superior base polymer, combined with Avient’s Colorant Chromatics expertise in high-temperature color formulation for both color concentrates and pre-colored solutions.
Key Market Players
- Avient Corporation
- LANXESS
AG
- Covestro
AG
- Gividi
Fabrics S.r.l.
- Kingfa
Science & Technology (India) Limited
- Saudi Basic Industries Corporation
- SGL
Carbon SE
- Teijin
Limited
- Jiangsu
QIYI Technology Co., Ltd.
- Toray
Advanced Composites Netherlands B.V.
By Product |
By Application |
By Region |
|
|
|
Related Reports
- Chloromethane Market - By Product type (Methylene Chloride, Methyl chloride, Chloroform, Carbon tetrachloride), By Appli...
- Paraffin Inhibitors Market Size – By Chemistry (Poly Acrylate, EVA Acrylate Copolymer, Hyperbranched Polyester, Modifi...
- Urea Formaldehyde Market - By Form (Powder, Liquid), By Application (Particleboard and Plywood, Medium Density Fiberboar...
- Iron Powder Market - By Type (Reduced iron powder, Atomised iron powder, Electrolytic iron powder), By Purity (High puri...
- Thermal Transfer Ribbon Market – By Printing Head Type (Flat Type, Near Head), By Product (Wax Resin Ribbon, Wax Ribbo...
- Iron & Steel Casting Market - By Material (Iron, Steel), By Process (Sand Casting, Die Casting), By Application (Automot...
Table of Content
FAQ'S
For a single, multi and corporate client license, the report will be available in PDF format. Sample report would be given you in excel format. For more questions please contact:
Within 24 to 48 hrs.
You can contact Sales team (sales@marketinsightsresearch.com) and they will direct you on email
You can order a report by selecting payment methods, which is bank wire or online payment through any Debit/Credit card, Razor pay or PayPal.
Discounts are available.
Hard Copy