Pharmaceutical Membrane Filtration Technologies Market – Global Industry Size, Share, Trends, Opportunity, and Forecast, 2018-2028 Segmented by Material (Polyethersulfone (PES), Mixed Cellulose Ester & Cellulose Acetate (MCE & CA), Polyvinylidene Difluoride (PVDF), Nylon Membrane Filters, others) by Technique (Microfiltration, Ultrafiltration, Nanofiltration, others), by Application (Final Product
Published Date: November - 2024 | Publisher: MIR | No of Pages: 320 | Industry: Healthcare | Format: Report available in PDF / Excel Format
View Details Buy Now 2890 Download Sample Ask for Discount Request CustomizationForecast Period | 2024-2028 |
Market Size (2022) | USD 5.89 billion |
CAGR (2023-2028) | 11.00% |
Fastest Growing Segment | Microfiltration |
Largest Market | North America |
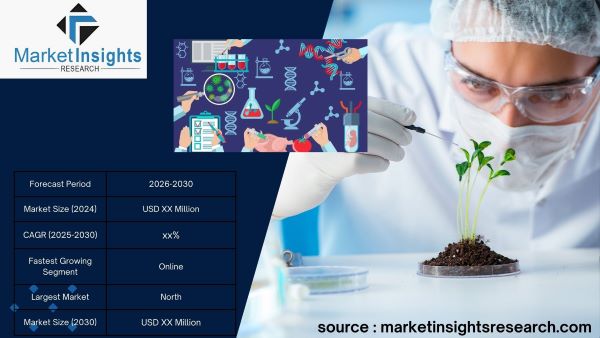
Market Overview
Global Pharmaceutical Membrane Filtration Technologies Market has valued at USD 5.89 billion in 2022 and is anticipated to witness an impressive growth in the forecast period with a CAGR of 11.00% through 2028
The development and production of biopharmaceuticals, including monoclonal antibodies, vaccines, and biosimilars, have been on the rise. Membrane filtration is crucial for the purification and sterile processing of these complex molecules. Regulatory agencies such as the FDA and EMA have imposed strict quality and safety standards on pharmaceutical manufacturing. Membrane filtration technologies help pharmaceutical companies comply with these regulations by ensuring the removal of contaminants, pathogens, and impurities. The importance of viral safety, highlighted by the COVID-19 pandemic, has driven the adoption of advanced membrane filtration technologies to remove or inactivate viruses during the production of vaccines and biopharmaceuticals. Pharmaceutical manufacturing has expanded in emerging markets, such as Asia and Latin America. This growth has driven the demand for membrane filtration technologies in these regions.
Key Market Drivers
Rising Pharmaceutical Production
The pharmaceutical industry is experiencing continuous growth due to factors such as population growth, aging demographics, and a higher incidence of chronic diseases. As a result, pharmaceutical companies are producing a greater volume and variety of drugs to meet the growing demand for healthcare products. Pharmaceutical companies are developing a wide range of drugs, including small-molecule drugs, biopharmaceuticals, vaccines, and biosimilars. Each of these product categories may require different membrane filtration processes for purification, sterilization, and quality control. Maintaining the quality and safety of pharmaceutical products is of paramount importance. Membrane filtration technologies are essential for ensuring that drugs meet strict quality standards by removing contaminants, impurities, and microorganisms from the manufacturing process. The production of biopharmaceuticals, such as monoclonal antibodies and gene therapies, has surged in recent years. These complex molecules require advanced filtration techniques to ensure purity and safety, driving the demand for specialized membrane filtration technologies.
The demand for vaccines, including the rapid development of COVID-19 vaccines, has significantly increased the need for membrane filtration technologies in the pharmaceutical sector. Sterile filtration is crucial for vaccine production to remove potential contaminants and ensure product safety. Regulatory agencies, such as the FDA and EMA, have established stringent standards for pharmaceutical manufacturing. Membrane filtration helps pharmaceutical companies comply with these regulations by providing a reliable method for achieving the required levels of product purity and sterility. The diversity of pharmaceutical products often necessitates customized filtration solutions. Membrane filtration technologies can be tailored to specific product and process requirements, allowing pharmaceutical manufacturers to address unique challenges effectively. In addition to product quality and safety, pharmaceutical companies are increasingly focused on sustainability and environmental responsibility. Membrane filtration technologies that reduce water and energy consumption contribute to environmentally friendly manufacturing practices. Pharmaceutical companies are expanding their market reach globally. This expansion has led to increased demand for membrane filtration technologies in different regions, including emerging markets. Ongoing research and development efforts in membrane filtration technology have led to advancements in membrane materials, designs, and performance. This continuous innovation further drives the adoption of these technologies in pharmaceutical manufacturing. This factor will help in the development of Global Pharmaceutical Membrane Filtration Technologies Market.
Increasing Production of Biopharmaceuticals and Biosimilars
Biopharmaceuticals, such as monoclonal antibodies, vaccines, and gene therapies, are large and structurally complex molecules. Their production involves the use of living cells (e.g., mammalian cell lines or microorganisms) for expression. Membrane filtration is essential to separate and purify these molecules from cell culture media, cell debris, and other impurities. Ensuring viral safety is critical in biopharmaceutical production, especially when using animal-derived cell lines. Membrane filtration technologies, including viral removal and viral filtration membranes, are employed to eliminate or inactivate potential viral contaminants, safeguarding the final product. The manufacturing of biopharmaceuticals typically involves bioprocesses, which require sterile conditions and precise control over environmental factors. Membrane filtration is used for sterilizing process gases, filtering culture media, and ensuring the sterility of equipment and consumables. Biopharmaceuticals must meet extremely high purity standards. Membrane filtration processes help achieve these standards by removing impurities, aggregates, endotoxins, and other contaminants that can affect product quality and safety.
Biopharmaceuticals often need to be concentrated to increase their potency or reduce volume for storage and transportation. Membrane filtration techniques, such as ultrafiltration and diafiltration, are employed for these purposes. Consistency in batch-to-batch product quality is essential for biopharmaceuticals. Membrane filtration technologies help maintain the reproducibility and consistency of bioprocesses, ensuring uniform product quality. The development and production of biosimilars, which are highly similar but not identical to reference biopharmaceuticals, have increased. Biosimilars require rigorous purification and characterization, and membrane filtration is integral to this process. Regulatory agencies, such as the FDA and EMA, have established stringent guidelines for biopharmaceutical production. Membrane filtration technologies are essential for compliance with these regulations by providing reliable and documented methods for product purification and sterilization. Membrane filtration solutions can be customized to meet the specific needs of biopharmaceutical production processes. This flexibility allows manufacturers to optimize filtration for individual products and processes. The biopharmaceutical market has been experiencing rapid growth due to the development of novel biologics and biosimilars. This growth has led to an increased demand for membrane filtration technologies to support biopharmaceutical manufacturing. Ongoing research and development efforts in membrane filtration technologies are geared toward meeting the evolving needs of biopharmaceutical production, including the filtration of increasingly complex molecules. This factor will pace up the demand of Global Pharmaceutical Membrane Filtration Technologies Market.
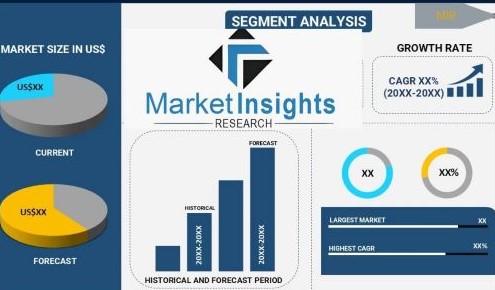
Rising Demand for Ultrafiltration Track-Etched Membranes
The biopharmaceutical and biotechnology industries require advanced filtration technologies to separate and purify complex molecules, such as proteins, antibodies, and nucleic acids. Ultrafiltration track-etched membranes can achieve precise molecular cutoffs, making them ideal for these applications. In pharmaceutical and biotechnology processes, the removal of viruses and other pathogens is critical to ensure the safety of the final product. Ultrafiltration track-etched membranes with well-defined pore sizes can effectively remove viruses while retaining valuable biomolecules. Ultrafiltration is used extensively in pharmaceutical manufacturing for the purification and concentration of drug products. Track-etched membranes enable the precise separation of target molecules, enhancing product quality. Research laboratories and academic institutions often use ultrafiltration track-etched membranes for various biological and biochemical applications, such as sample preparation, protein concentration, and desalting. These membranes are used in diagnostic devices and medical applications for tasks such as sample filtration, separation of analytes, and blood plasma processing.
In the food and beverage industry, ultrafiltration track-etched membranes are employed for the removal of microorganisms, particulates, and macromolecules. This helps improve product shelf life, quality, and safety. Ultrafiltration is used in water and wastewater treatment to remove particles, bacteria, and impurities. Track-etched membranes are chosen for their precise filtration capabilities. These membranes are used in electronics and semiconductor manufacturing for particle removal and the production of ultrapure water, which is crucial for semiconductor fabrication processes. Environmental agencies and organizations use track-etched membranes to monitor and analyze water quality, especially in detecting and quantifying microorganisms and pollutants. Track-etched membranes can be customized to meet specific requirements, including precise pore size, membrane thickness, and surface properties, making them versatile for a wide range of applications. In industries where product quality and consistency are paramount, such as pharmaceuticals and biotechnology, ultrafiltration track-etched membranes play a crucial role in quality control and assurance. These membranes are favored in industries subject to strict regulatory standards, as they provide reliable and well-characterized filtration solutions that meet regulatory requirements. Track-etched membranes are user-friendly and compatible with a variety of filtration systems, making them accessible and widely adopted in laboratory and industrial settings. This factor will accelerate the demand of Global Pharmaceutical Membrane Filtration Technologies Market.
Key Market Challenges
Scale-Up Challenges
Ensuring that membrane filtration processes maintain consistent performance and achieve the same results at both laboratory and industrial scales can be challenging. Factors like membrane fouling, flow dynamics, and mass transfer may behave differently at larger scales. Membrane fouling occurs when particles, contaminants, or biomolecules accumulate on the membrane surface, reducing filtration efficiency. Scaling up can exacerbate fouling issues, necessitating the development of effective fouling mitigation strategies. Large-scale filtration systems may exhibit different hydrodynamic behaviors compared to smaller-scale systems. Understanding and optimizing flow dynamics, pressure differentials, and shear forces are critical to prevent uneven filtration and membrane damage. Ensuring that scaled-up filtration processes are validated and qualified for regulatory compliance can be time-consuming and costly. This includes demonstrating that the process consistently meets quality and safety standards. Maintaining the integrity of large-scale membranes is crucial. Membrane materials must withstand the stresses of large-scale operations, and strategies for monitoring and ensuring membrane integrity must be in place. Scaling up filtration processes can introduce economic challenges, such as increased capital investment, operating costs, and resource consumption. Companies must strike a balance between cost-effectiveness and process efficiency.
Fouling and Cleaning
In the pharmaceutical industry, protein fouling is a common issue when filtering biopharmaceuticals and vaccines. Proteins can adhere to membrane surfaces, causing flux decline and affecting product yield and purity. Fouling can occur both on the membrane's surface (cake filtration) and within the membrane's pores (internal fouling). Internal fouling can be more challenging to address as it may require more aggressive cleaning methods. Microbial contaminants, including bacteria and fungi, can colonize membrane surfaces, leading to biofouling. This is a significant concern for pharmaceutical companies, as it can compromise product sterility. The presence of particulate matter in pharmaceutical formulations can lead to fouling of filtration membranes. This can occur during the filtration of drug formulations or intermediate steps in the manufacturing process. Choosing appropriate cleaning agents and procedures without compromising the integrity of the filtration membrane is challenging. Cleaning solutions must effectively remove fouling agents without damaging the membrane material. Cleaning processes must be validated and verified to ensure that they consistently achieve the desired level of cleanliness. This involves conducting cleaning validation studies and documenting the results. Cleaning procedures can be time-consuming and require significant resources. Downtime for cleaning can impact production schedules and increase operational costs.
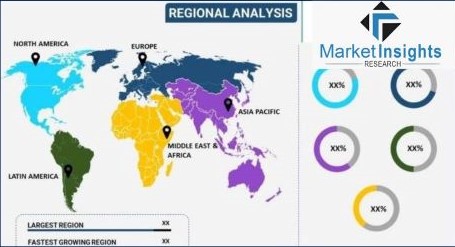
Key Market Trends
Increased Outsourcing
The pharmaceutical industry has witnessed significant growth in contract manufacturing, where CMOs provide various services, including filtration processes. Outsourcing filtration steps to CMOs allows pharmaceutical companies to focus on core competencies, such as drug development and marketing. CMOs often have specialized expertise in membrane filtration technologies and processes. They can offer advanced filtration solutions, optimization of processes, and regulatory compliance, which can be advantageous to pharmaceutical manufacturers. They can lead to cost savings for pharmaceutical companies. CMOs may have cost-effective infrastructure and economies of scale, which can result in reduced operational expenses. It also provides flexibility in managing production capacity. Pharmaceutical companies can scale production up or down as needed without making significant capital investments in filtration equipment. Reputable CMOs are well-versed in regulatory requirements, including Good Manufacturing Practices (GMP). They can ensure that filtration processes comply with regulatory standards, simplifying the regulatory approval process. Outsourcing can help mitigate risks associated with filtration processes. CMOs can provide redundancy and backup systems, reducing the risk of production interruptions due to equipment failures or maintenance.
Segmental Insights
Material Insights
In 2022, the Global Pharmaceutical Membrane Filtration Technologies Market dominated by Polyethersulfone (PES) segment and is predicted to continue expanding over the coming years.
Technique Insights
In 2022, the Global Pharmaceutical Membrane Filtration Technologies Market dominated by Microfiltration segment and is predicted to continue expanding over the coming years.
Application Insights
In 2022, the Global Pharmaceutical Membrane Filtration Technologies Market largest share was held by Final Product Processing segment in the forecast period and is predicted to continue expanding over the coming years.
Regional Insights
The North America region dominates the Global Pharmaceutical Membrane Filtration Technologies Market in 2022.
Recent Developments
- In January2020, Leading science and technologycorporation Merck announced a €250 million investment in a new building inCorsier-sur-Vevey, Switzerland, called the Merck Biotech research Centre, whichwould be used for the research and manufacture of biotech products for clinicaltrials. This investment will help to sustainably secure capacity and highagility to deliver clinical trial material in a cost-effective manner,contribute to accelerated development timelines of new biological entities, andaddress the rising manufacturing complexity of the upcoming generations ofbiotech compounds. It is motivated by the growth of the Healthcare businesssector R&D pipeline. The Life Sciences' process solutions for clinicalmanufacturing and pilot plant operations as well as Performance Materials'eyrise dynamic liquid crystal windows as part of the highly effective energymanagement of the building will be on display at the Biotech Development Centreas examples of Merck's science and technology across its three businesssectors.
- In February 2019, The Sani-Pro spiral elementproduct line has been introduced by Koch Membrane Systems, Inc. (KMS), and isdesigned to meet the exacting standards of membrane separations in the food,beverage, and life science industries. Sani-Pro components are designed forhigher pressure operation and to endure rigorous chemical cleaning without anyperformance degradation, prolonging their operational life in comparison toconventional products. They build on KMS' 50-year track record of dependabilityand innovation. The line is also intended to lower the danger of contamination,boost production, save operating costs, and improve energy efficiency. Sani-Prosanitary spirals exhibit long life and cost-effective operation in a variety ofapplications, including the concentration and purification of animal andplant-based proteins, the clarification of fermentation broth, productrecovery, the concentration of gelatin and juice colour, sugar separations, andsweetener clarification. Sani-Pro components adhere to all relevant FDA, 3A,EU, and Halal standards and laws.
Key Market Players
- 3MCompany
- Danaher Corporation
- GE Healthcare
- GEA Group
- Graver Technologies
- Merck Millipore
- Parker Hannifin Corporation
- Repligen Corporation
- Sartorius Stedim Biotech GmbH
- Thermo Fisher Scientific Inc.
By Material | By Technique | By Application | By Region |
· Polyethersulfone (PES) · Mixed Cellulose Ester & Cellulose Acetate (MCE & CA) · Polyvinylidene Difluoride (PVDF) · Nylon Membrane Filters · Others | · Microfiltration · Ultrafiltration · Nanofiltration · Others | · Final Product Processing · Raw Material Filtration · Cell Separation · Water Purification · Air Purification | · North America · Asia-Pacific · Europe · South America · Middle East & Africa |
Related Reports
- Veterinary Infusion Pumps Market – By Product (Syringe, Volumetric, Ambulatory, Implantable), Animal type (Companion, ...
- Veterinary CRO and CDMO Market – By Animal Type (Companion, Livestock), Service Type (CRO, [Clinical Trials, Quality A...
- Pet Sitting Services Market – By Service (In-home Pet Sitting Services, Drop-in Visits, Boarding Services, Daycare Ser...
- Veterinary Video Endoscopes Market – By Product (Equipment, PACS Software), Animal Type (Small, Large), Application (D...
- Pet Herbal Supplements Market – By Product Type (Multivitamins & Minerals, Omega 3 Fatty Acids), Application (Digestiv...
- Equine Artificial Insemination Market Size - By Component (Services, Semen [Fresh, Chilled, Frozen], Equipment, Reagents...
Table of Content
To get a detailed Table of content/ Table of Figures/ Methodology Please contact our sales person at ( chris@marketinsightsresearch.com )
List Tables Figures
To get a detailed Table of content/ Table of Figures/ Methodology Please contact our sales person at ( chris@marketinsightsresearch.com )
FAQ'S
For a single, multi and corporate client license, the report will be available in PDF format. Sample report would be given you in excel format. For more questions please contact:
Within 24 to 48 hrs.
You can contact Sales team (sales@marketinsightsresearch.com) and they will direct you on email
You can order a report by selecting payment methods, which is bank wire or online payment through any Debit/Credit card, Razor pay or PayPal.
Discounts are available.
Hard Copy