Marché des machines-outils – Taille de l’industrie mondiale, part, tendances, opportunités et prévisions, segmenté par type de machine-outil (tours, fraiseuses, perceuses, rectifieuses, machines à décharge électrique (EDM), machines de formage (par exemple, presses plieuses, cisailles), autres (par exemple, machines de découpe laser, machines de découpe au jet d’eau)), par matériau d’outil (outils
Published Date: November - 2024 | Publisher: MIR | No of Pages: 320 | Industry: Infrastructure | Format: Report available in PDF / Excel Format
View Details Buy Now 2890 Download Sample Ask for Discount Request CustomizationPériode de prévision | 2024-2028 |
Taille du marché (2022) | 6,03 milliards USD |
TCAC (2023-2028) | 6,15 % |
Segment à la croissance la plus rapide | Outils en carbure |
Marché le plus important | Asie-Pacifique |
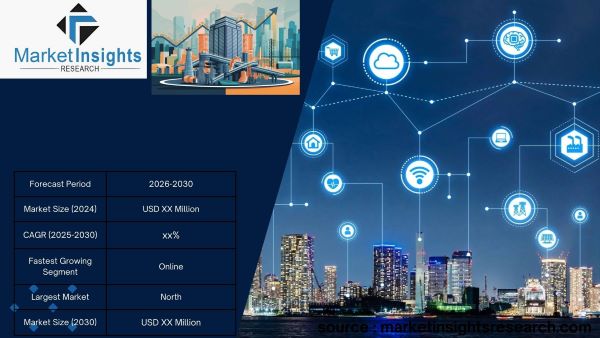
Aperçu du marché
Le marché mondial des machines-outils était évalué à 6,03 milliards USD en 2022 et devrait connaître une croissance robuste au cours de la période de prévision avec un TCAC de 6,15 % jusqu'en 2028.
Les principaux fabricants se sont associés aux principaux fournisseurs de machines-outils pour transformer numériquement leurs fonctions de gestion des actifs. Les solutions améliorent la collaboration entre les services, offrent une connaissance de la situation grâce à l'accès mobile et facilitent la gestion de la conformité réglementaire. Les fournisseurs continuent de faire progresser leurs solutions grâce à des innovations dans des domaines tels que l'IoT, le cloud et la cybersécurité. Cela garantit des solutions sécurisées, évolutives et interopérables pour divers besoins en équipements de fabrication. La R&D continue et l'acceptation croissante des stratégies basées sur les données indiquent que les solutions de machines-outils joueront un rôle de plus en plus important dans l'optimisation des opérations et la prise de décision dans des conditions d'incertitude. Les partenariats et la conformité aux normes émergentes devraient soutenir la forte dynamique de croissance de ce marché. Les perspectives à long terme pour les machines-outils restent positives, car les entreprises reconnaissent la valeur commerciale d'une gestion proactive des performances et des risques des équipements.
Principaux moteurs du marché
Accent mis sur l'amélioration de la productivité et de l'efficacité opérationnelle
Dans le paysage concurrentiel actuel de la fabrication, la maximisation de la productivité et de l'efficacité est essentielle à la réussite des entreprises. Les machines-outils jouent un rôle clé en permettant l'optimisation des processus de production. Les méthodes traditionnelles de surveillance manuelle et de maintenance réactive ne parviennent pas à suivre le rythme de la complexité croissante et des objectifs de production.
Les solutions pour machines-outils répondent à ce problème en offrant une visibilité en temps réel sur les mesures de performance des équipements. Des analyses avancées révèlent les goulots d'étranglement, les causes des temps d'arrêt et les problèmes de capacité sur les actifs distribués. Les modèles de maintenance prédictive utilisant la fusion de capteurs évitent les pannes inattendues grâce à une surveillance automatisée de l'état. Les outils basés sur la vision par ordinateur évaluent de manière autonome la qualité pour minimiser les défauts et les retouches.
Armés d'informations exploitables, les fabricants peuvent planifier de manière proactive la maintenance pendant les temps d'arrêt planifiés. Les diagnostics et réparations à distance minimisent les interruptions. Les flux de travail automatisés garantissent la conformité réglementaire et de sécurité pour maintenir la disponibilité. Les capacités de simulation et de jumeau numérique permettent de tester les améliorations des processus pratiquement avant la mise en œuvre.
En conséquence, les fabricants bénéficient de changements optimisés, d'un temps moyen de réparation réduit, d'une meilleure utilisation des actifs, de meilleurs rendements au premier passage et d'une efficacité globale des équipements. Pour les industries à forte intensité de capital comme l'automobile, même les gains d'efficacité infimes se traduisent par des économies de coûts substantielles.
Avec des pressions de production croissantes, les outils basés sur les données sont devenus indispensables pour maximiser la productivité de manière durable. Leur capacité à rationaliser les opérations à grande échelle stimulera une demande importante du marché.
Adoption des technologies de l'industrie 4.0
L'industrie 4.0 a transformé la fabrication avec des technologies avancées telles que l'IoT, l'IA, le cloud, la réalité augmentée, la fabrication additive et la robotique. Au cœur de cette transformation se trouve le besoin d'outils, de machines et de systèmes parfaitement connectés générant des volumes massifs de données en temps réel.
Les solutions de machines-outils exploitent ces technologies pour fournir une intelligence augmentée. Les capteurs intégrés offrent une vue numérique à 360 degrés des actifs pour les modèles de maintenance prédictive et d'assurance qualité. Les plateformes cloud offrent un traitement des données et un hébergement de modèles évolutifs. Les protocoles IIoT garantissent l'interopérabilité entre des systèmes hétérogènes.
Les applications de réalité augmentée guident les opérateurs et les techniciens à travers les manuels, les instructions de travail et les réparations. La fabrication additive fabrique des pièces de rechange à la demande pour minimiser les temps d'arrêt. Les robots collaboratifs améliorent la productivité et la sécurité des travailleurs.
À mesure que les technologies convergent, leur plein potentiel ne peut être réalisé que par le biais de plateformes centralisées. Les machines-outils apparaissent comme l'épine dorsale pour extraire la valeur des investissements de l'industrie 4.0 grâce à des informations et une prise de décision basées sur les données.
Compte tenu de la compétitivité croissante, les fabricants sont désireux d'adopter des technologies transformatrices. Cela permet aux machines-outils de se positionner en bonne position pour aider les industries à tenir la promesse d'une production intelligente, autonome et durable. Leur capacité à maximiser le retour sur investissement de l'industrie 4.0 sera un facteur clé de la demande.
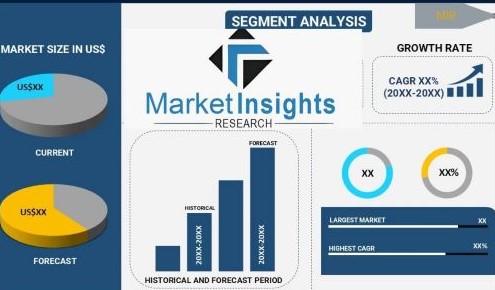
Assurer la conformité aux normes en constante évolution
Les réglementations de fabrication deviennent de plus en plus strictes à l'échelle mondiale avec des normes sur la qualité des produits, l'impact environnemental, la consommation d'énergie, la sécurité au travail et plus encore. La non-conformité peut entraîner des pénalités coûteuses, des rappels ou des interdictions dans les principales économies.
Les solutions de machines-outils aident à résoudre ce problème en surveillant en permanence les processus de production, les actifs et les travailleurs pour les paramètres réglementaires en temps réel. Les flux de travail automatisés garantissent que toutes les normes, certifications et meilleures pratiques sont suivies méticuleusement pour maintenir la conformité.
Les analyses avancées révèlent des modèles subtils pour identifier de manière proactive les non-conformités potentielles. Les capacités de simulation et de test de scénarios permettent de valider la conformité des nouveaux processus pratiquement avant le déploiement. La tenue de registres automatisée et les pistes d'audit simplifient la démonstration de la conformité aux régulateurs et aux clients.
À mesure que les normes évoluent rapidement avec de nouvelles exigences en matière de réduction de l'empreinte carbone, de pratiques d'économie circulaire, de déclaration des minéraux de conflit, etc., le besoin d'une gestion centralisée de la conformité va s'intensifier. Les machines-outils apparaissent comme la plateforme idéale pour simplifier cette complexité à grande échelle.
Principaux défis du marché
Recyclage de la main-d'œuvre pour l'adoption de l'industrie 4.0
Le déploiement généralisé de machines-outils avancées exige de nouvelles compétences de la part des ouvriers et des techniciens des usines. Les compétences traditionnelles axées sur l'utilisation et le dépannage des équipements manuels doivent désormais évoluer pour inclure des domaines tels que l'IA, le big data, le cloud, la cybersécurité, la robotique, etc.
Cependant, la requalification des effectifs importants en place présente des défis. Tous les travailleurs ne sont pas forcément disposés ou capables d'adopter de nouvelles technologies en raison de leur âge, de leur niveau d'éducation ou du rythme du changement. Les programmes de reconversion nécessitent des investissements substantiels et des perturbations opérationnelles que de nombreux petits fabricants ne peuvent pas se permettre.
Même lorsque des formations sont dispensées, le transfert de nouvelles connaissances vers des applications concrètes prend du temps. Sans conseils, les travailleurs peuvent avoir du mal à contextualiser les informations basées sur les données ou à exploiter en toute confiance les outils de réalité augmentée/virtuelle.
Les fournisseurs de machines-outils doivent travailler en étroite collaboration avec les établissements d'enseignement pour développer un programme standardisé pour les rôles de l'industrie 4.0. Les programmes de certification peuvent valider les niveaux de maîtrise. Les clients doivent également favoriser une culture d'apprentissage continu par le biais de projets pratiques et de mentorat.
Si le déficit de compétences n'est pas comblé de manière proactive, les fabricants ne réaliseront pas le plein potentiel de leurs investissements dans les machines-outils. Des compétences obsolètes peuvent compromettre l'adoption, les gains de productivité et la compétitivité à long terme. La reconversion reste un défi organisationnel majeur.
Intégration de l'infrastructure existante
La plupart des fabricants exploitent des paysages d'infrastructure hétérogènes avec des machines existantes, des automates programmables (PLC) et des systèmes SCADA de plusieurs époques. L'intégration transparente des outils aux systèmes existants nécessite des efforts considérables.
Les machines existantes manquent souvent de capteurs intégrés pour la surveillance de l'état. Leur mise à niveau entraîne des coûts supplémentaires et des interruptions de production. Les protocoles et les interfaces varient également selon les PLC, les historiens et les autres systèmes de contrôle. L'intégration des données entre les silos est difficile en raison d'incohérences structurelles et sémantiques.
Les vulnérabilités de sécurité émergent également des lacunes du réseau pendant l'intégration. La conformité réglementaire doit être revalidée. Les tests de compatibilité et de performances ont un impact sur les flux de production.
À moins que les actifs existants ne soient mis à niveau ou éliminés progressivement de manière judicieuse, les machines-outils peuvent ne pas offrir la valeur promise pour les industries à forte intensité de capital. La normalisation via les protocoles IIoT et l'informatique de pointe peut aider, mais l'intégration complète restera un long chemin. Cela constitue un obstacle pour les petits fabricants dont les budgets de modernisation sont limités.
Les fournisseurs doivent proposer des solutions optimisées, des services de conseil et des options de financement pour aider les clients à surmonter ces défis d'infrastructure en douceur. Dans le cas contraire, les problèmes hérités du passé continueront de restreindre le potentiel de croissance du marché.
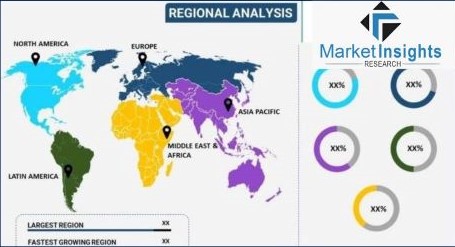
Principales tendances du marché
Montée en puissance des modèles de tarification basés sur les résultats
Traditionnellement, les solutions de machines-outils étaient vendues aux fabricants avec des frais de licence initiaux élevés et des coûts supplémentaires pour les personnalisations, la formation, la mise en œuvre et le support continu. Alors que ce modèle de tarification offrait une certaine flexibilité aux grandes entreprises disposant d'équipes informatiques dédiées pour gérer les déploiements sur site, il limitait l'accès pour de nombreux fabricants de petite et moyenne taille disposant de budgets et de ressources informatiques limités.
Cependant, à mesure que le marché des machines-outils continue de devenir plus compétitif, les fournisseurs reconnaissent la nécessité de rendre leurs solutions accessibles à une clientèle plus large, y compris aux environnements de production flexibles à faible volume. Ils adoptent de plus en plus des modèles de tarification au compteur ou basés sur les résultats qui sont alignés sur les résultats commerciaux tangibles obtenus par les clients. Plutôt que de payer des frais uniques élevés, les clients paient en fonction de paramètres mesurables tels que l'augmentation du volume de production, la réduction de la consommation d'énergie, des taux de qualité des produits plus élevés, une plus grande disponibilité des équipements, moins de pannes et d'autres gains obtenus grâce aux solutions de machines-outils.
Ce modèle de paiement à la performance réduit les coûts initiaux et les risques financiers pour les clients. Il supprime également les obstacles qui empêchaient les petits fabricants d'adopter des outils avancés. Dans le même temps, la tarification basée sur les résultats incite les fournisseurs à s'assurer que leurs solutions sont optimisées pour les processus, les flux de travail et l'infrastructure uniques de chaque déploiement client. Cela conduit à un engagement participatif entre les fournisseurs et les clients tout au long de la mise en œuvre et de l'utilisation des solutions. Au fur et à mesure que davantage de données sur les résultats opérationnels et de productivité sont collectées au fil du temps à partir de déploiements en direct, les prix peuvent être automatiquement ajustés en fonction des niveaux de performance éprouvés.
Ce modèle commercial gagnant-gagnant, basé sur l'utilisation, devrait accélérer la croissance du marché global des machines-outils en mettant les capacités de l'Industrie 4.0 à la portée financière d'un plus grand nombre d'entreprises du segment des petites et moyennes entreprises. Elle offre également aux fournisseurs un flux de revenus récurrents plus fiable que les frais de licence uniques. La tarification basée sur les résultats émerge ainsi comme un nouveau paradigme de tarification populaire dans le secteur des machines-outils.
Montée en puissance de la maintenance prédictive basée sur l'IA
Une capacité clé qui stimule la croissance des solutions de machines-outils est la maintenance prédictive alimentée par l'intelligence artificielle et les algorithmes d'apprentissage automatique. Ces algorithmes nécessitent des ensembles de données massifs contenant des mesures de capteurs en séries chronologiques, des paramètres de processus, des journaux de machines, des enregistrements de temps d'arrêt et d'autres données opérationnelles collectées à partir de parcs d'équipements sur de longues périodes dans des conditions variables. Cette richesse de données historiques sur les pannes et les performances permet aux algorithmes d'identifier des modèles et des corrélations subtils que les humains peuvent manquer, afin de prédire avec précision les problèmes potentiels bien avant qu'ils n'affectent les flux de production.
Cependant, pour la plupart des petits fabricants, la collecte de tels ensembles de données de défaillance et de fonctionnement jusqu'à la défaillance à partir de machines individuelles sous leur contrôle n'est pas réalisable. C'est là que les modèles d'apprentissage automatique hébergés dans le cloud et formés sur des données anonymes agrégées provenant d'un large éventail d'actifs industriels connectés s'avèrent précieux. Les fournisseurs exploitent des ensembles de données partagés contenant des modèles d'utilisation des équipements de milliers de clients mondiaux pour améliorer en permanence la précision prédictive de leurs modèles d'IA/ML. Les modèles formés sur des données regroupées provenant d'un ensemble diversifié de machines dans différents secteurs et zones géographiques sont capables de détecter des signes subtils de détérioration des équipements que les modèles d'un seul client peuvent manquer.
Les solutions avancées de machines-outils analysent désormais les flux de capteurs multidimensionnels à haute fréquence, les paramètres de processus, les journaux des machines et d'autres données opérationnelles à l'aide de ces modèles formés dans le cloud. Ils peuvent détecter des anomalies indiquant des défauts imminents de composants, des écarts de processus ou des pannes de machines des jours ou même des semaines à l'avance. Ces prévisions à long terme aident le personnel de maintenance à planifier des réparations juste à temps sans perturber les calendriers de production. Les outils de réalité augmentée et virtuelle facilitent également le dépannage à distance et l'orientation des techniciens sur site. Les mises à jour en direct aident également à optimiser en permanence les performances des machines sur le terrain. À mesure que les modèles d'IA mûrissent avec davantage de données au fil du temps, ils conduiront les équipements vers une efficacité, un rendement et une disponibilité accrus grâce à des corrections de processus automatisées, des routines de maintenance basées sur l'état et une résolution autonome des problèmes à distance. La maintenance prédictive basée sur l'IA basée sur le cloud est donc un moteur majeur de l'industrie des machines-outils.
Personnalisation via des écosystèmes ouverts et des revendeurs d'applications
Si les solutions de machines-outils standardisées constituent un bon point de départ pour la numérisation des flux de production, aucun fournisseur ne peut à lui seul répondre à tous les besoins uniques et évolutifs de l'environnement de production spécialisé, de l'infrastructure existante et des objectifs stratégiques de chaque client. Les solutions ponctuelles manquent souvent de la flexibilité requise pour une intégration et une extension personnalisées. Dans le même temps, les coûts élevés impliqués dans la création de systèmes entièrement personnalisés à partir de zéro empêchent de nombreux fabricants de tirer le meilleur parti de leurs investissements.
Pour surmonter ces défis, les fournisseurs de machines-outils adoptent désormais des écosystèmes ouverts et des réseaux de partenaires. Ils offrent aux fabricants un accès à des revendeurs d'applications et à des marchés contenant une collection croissante de solutions complémentaires spécialisées mais interopérables, validées pour fonctionner de manière transparente avec leurs plateformes de base. Les clients peuvent choisir librement les meilleurs composants de divers fournisseurs indépendants pour assembler des configurations adaptées à leurs besoins spécifiques. Les architectures de produits modulaires simplifient également l'intégration de ces outils et sources de données complémentaires sans mises à niveau perturbatrices.
Les API standardisées et les kits de développement permettent aux clients de personnaliser les interfaces, de créer des applications propriétaires exploitant les données des machines-outils ou de faire appel à des intégrateurs système pour des exigences sur mesure complexes. Une approche ouverte basée sur des normes d'interopérabilité remplace le verrouillage propriétaire, permettant aux machines-outils d'agir comme une colonne vertébrale d'intégration pour diverses solutions de pointe.
Cette évolution vers des architectures ouvertes et personnalisables devrait accélérer les taux d'adoption. Elle offre aux fabricants une flexibilité sans précédent pour optimiser leurs déploiements autour d'un noyau modulaire, tout en ajoutant des solutions spécialisées à mesure que leurs besoins et stratégies de fabrication évoluent au fil du temps. Les fournisseurs bénéficient également d'un écosystème élargi de partenaires améliorant la valeur globale de leurs offres. L'ouverture sera une tendance déterminante qui façonnera le paysage des machines-outils.
Informations sectorielles
Informations sur les types de machines-outils
Les tours ont dominé le marché mondial des machines-outils en 2022, captant plus de 30 % de la part globale des revenus. Le tournage est un processus d'enlèvement de matière qui utilise un outil de coupe à pointe unique pour couper la matière indésirable d'une pièce en rotation afin de produire un objet axisymétrique avec une bonne finition de surface. Elle reste la méthode d'usinage la plus utilisée pour produire des pièces cylindriques et d'autres pièces à symétrie de rotation dans toutes les industries.
Les tours sont polyvalents et peuvent fabriquer une variété de composants de géométries simples à complexes en grandes quantités. Ils sont couramment utilisés dans l'automobile, l'aérospatiale, les dispositifs médicaux et d'autres secteurs de fabrication pour produire des arbres, des cylindres, des bagues, des engrenages et d'autres pièces rotatives. Les faibles temps de réglage et les taux de production élevés obtenus grâce aux tours les rendent parfaitement adaptés aux environnements de production de masse. De plus, la disponibilité d'une large gamme de centres de tournage avancés équipés de capacités multitâches, de changeurs d'outils automatisés et de systèmes de mesure intégrés favorise une adoption accrue. La demande croissante de composants tournés de la part des industries d'utilisation finale en expansion ainsi que la nécessité d'améliorer la productivité devraient maintenir la domination des tours au cours de la période de prévision.
Informations sur les matériaux des outils
Les outils en carbure ont dominé le marché mondial des machines-outils en 2022 par matériau d'outil, représentant plus de 40 % du chiffre d'affaires global. Les outils en carbure sont fabriqués à partir de carbure de tungstène, l'un des matériaux les plus durs que l'on trouve pour les outils de coupe. Ils offrent une résistance à l'usure, une résistance et une dureté élevées par rapport à d'autres matériaux d'outils comme l'acier rapide.
Les outils en carbure peuvent usiner une variété de métaux et de non-métaux à des vitesses et des avances élevées. Ils conservent leur tranchant tranchant pendant longtemps et offrent une meilleure finition de surface même pendant les coupes interrompues. Par conséquent, les outils en carbure sont capables d'atteindre des taux d'enlèvement de matière et des niveaux de productivité élevés. Leur capacité à usiner à des vitesses de coupe plus élevées se traduit également par des temps de cycle réduits. De plus, les outils en carbure ne nécessitent pas de dressage ou d'affûtage fréquents par rapport à d'autres matériaux d'outils. Cela réduit les coûts d'outillage et les temps d'arrêt pour les opérateurs. La complexité croissante des composants usinés et le besoin de tolérances plus strictes stimulent encore davantage la demande d'outils en carbure dans des secteurs tels que l'automobile, l'aérospatiale et la fabrication de matrices/moules. FrançaisAvec leurs performances supérieures et leurs avantages en termes de coûts par rapport aux alternatives, les outils en carbure devraient continuer à dominer le marché des machines-outils au cours de la période de prévision...
Perspectives régionales
L'Asie-Pacifique a dominé le marché mondial des machines-outils en 2022, représentant plus de 40 % du chiffre d'affaires total. La Chine, le Japon, l'Inde, la Corée du Sud et d'autres pays en développement contribuent largement à la part importante de la région.
L'Asie-Pacifique est devenue le plus grand centre de fabrication au monde, grâce à une forte croissance dans des secteurs tels que l'automobile, l'électronique, les machines et les équipements lourds. La région abrite un grand nombre d'équipementiers de machines-outils ainsi que des industries d'utilisation finale dotées d'énormes capacités de fabrication. Elle a connu une industrialisation rapide et d'importants investissements en capital dans des installations de fabrication de pointe ces dernières années. En outre, les initiatives gouvernementales promouvant « Make in India » et « Made in China 2025 » encouragent la production locale et la substitution des importations.
Le vaste secteur manufacturier et l'adoption croissante de l'automatisation industrielle en Asie-Pacifique ont stimulé la demande de machines-outils. Français La disponibilité d'une main-d'œuvre qualifiée à faible coût et la proximité des marchés d'utilisation finale confèrent à la région un avantage concurrentiel par rapport aux autres régions. En outre, les fabricants de machines-outils étendent leur présence en Asie pour répondre à la demande locale croissante. Ceci, ainsi que l'augmentation des investissements dans les technologies de l'industrie 4.0, laisse présager une domination durable de l'Asie-Pacifique sur le marché mondial des machines-outils au cours de la période de prévision.
Développements récents
- En juin 2022, Doosan MachineTools a annoncé l'agrandissement de son usine de fabrication en Inde. La nouvelle usine se concentrera sur la production de tours et de centres d'usinage CNC répondant à la demande croissante des secteurs nationaux de l'automobile et de l'ingénierie.
- En mai 2022, DMG Mori a acquis une participation majoritaire dans Metalcraft Engineering, un fabricant de tours CNC. Cela élargit le portefeuille de produits et la présence de DMG Mori sur le marché indien.
- En avril 2022, Yamazaki Mazak a lancé le centre de tournage multitâche QUICK TURN SMART 250SY. Il présente une conception compacte pour la production en petites séries et des fonctions intégrées basées sur l'IA pour l'optimisation automatisée de l'usinage.
- En mars 2022, AMADA a ouvert un nouveau centre de formation technique dans le Michigan, aux États-Unis, pour perfectionner les compétences des clients et soutenir les initiatives de transformation numérique. Le centre offrira une formation pratique sur les technologies de fabrication de tôles.
- En février 2022, Okuma America a étendu sa présence en acquérant Cincinnati Inc., un fournisseur de machines-outils, d'automatisation et de solutions de fabrication additive.
- En janvier 2022, Komatsu a lancé son nouveau système de production cellulaire GRACE doté de véhicules guidés autonomes et d'un contrôle qualité intégré basé sur l'IA inspection.
- En décembre 2021, Hyundai WIA a acquis le fabricant allemand de machines-outils DMG Mori pour avoir accès à des technologies de fabrication avancées.
- En novembre 2021, Makin a lancé de nouveaux centres d'usinage verticaux à 5 axes avec changeurs d'outils automatisés intégrés et des enveloppes de travail élargies.
Principaux acteurs du marché
- AMADA HOLDINGS CO., LTD.
- DMG MORI CO., LTD.
- GROUPE TRUMPF
- JTEKT Société
- Komatsu Ltd
- Okuma Corporation
- DoosanMachine Tools Co., Ltd
- Makino Milling Machine Co., Ltd
- HYUNDAI WIA CORP
- CHIRON Group SE
Par type de machine-outil | Par matériau d'outil | Par utilisateur final | Par région |
|
|
|
|
Related Reports
- Taille du marché des portes coupe-feu – Par type de produit (porte coupe-feu battante, porte coupe-feu à double acti...
- Taille du marché des terrasses en bois – Par type de bois (bois traité sous pression, séquoia, cèdre, bois dur tro...
- Taille du marché des équipements de construction autonomes – Par produit (équipements de terrassement et de constru...
- Taille du marché des camions de construction – Par camions (camions à benne basculante, camions semi-remorques, cami...
- Taille du marché des camions miniers autonomes – Par camions (camions à benne rigide, camions à benne articulée, c...
- Taille du marché des murs-rideaux en aluminium – Par type de système (système construit en bâtons, unitisé et sem...
Table of Content
To get a detailed Table of content/ Table of Figures/ Methodology Please contact our sales person at ( chris@marketinsightsresearch.com )
List Tables Figures
To get a detailed Table of content/ Table of Figures/ Methodology Please contact our sales person at ( chris@marketinsightsresearch.com )
FAQ'S
For a single, multi and corporate client license, the report will be available in PDF format. Sample report would be given you in excel format. For more questions please contact:
Within 24 to 48 hrs.
You can contact Sales team (sales@marketinsightsresearch.com) and they will direct you on email
You can order a report by selecting payment methods, which is bank wire or online payment through any Debit/Credit card, Razor pay or PayPal.
Discounts are available.
Hard Copy