Mercado de moldeo por inyección de metales: tamaño de la industria global, participación, tendencias, oportunidades y pronóstico, 2018-2028, segmentado por tipo de material (acero inoxidable, acero de baja aleación y material magnético blando), por industria de uso final (automotriz, médica y de atención médica, eléctrica y electrónica y otras), por región, competencia
Published Date: November - 2024 | Publisher: MIR | No of Pages: 320 | Industry: Infrastructure | Format: Report available in PDF / Excel Format
View Details Buy Now 2890 Download Sample Ask for Discount Request CustomizationPeríodo de pronóstico | 2024-2028 |
Tamaño del mercado (2022) | 1.78 mil millones de USD |
CAGR (2023-2028) | 7,52 % |
Segmento de más rápido crecimiento | Acero de baja aleación |
Mercado más grande | Asia Pacífico |
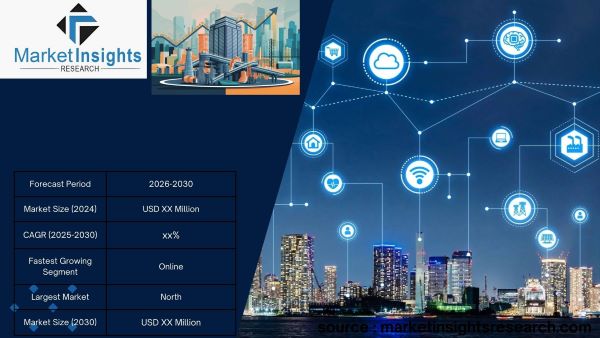
Descripción general del mercado
El mercado global de moldeo por inyección de metales alcanzó una valoración de USD 1.78 mil millones en 2022 y se proyecta que alcance los USD 3.35 mil millones para 2028, lo que refleja una tasa de crecimiento anual compuesta (CAGR) del 7,52% durante el período de pronóstico. La trayectoria de crecimiento del mercado se atribuye a la creciente demanda en diversos sectores de usuarios finales. Además, se espera que los avances tecnológicos en el campo contribuyan a la expansión del mercado durante el período de pronóstico. En particular, la creciente demanda del sector automotriz es una fuerza impulsora clave detrás del crecimiento del mercado de moldeo por inyección de metales. Los proveedores de servicios de moldeo por inyección están encontrando oportunidades dentro de la industria automotriz debido a la adopción global de vehículos eléctricos. Los componentes como engranajes, sellos e imanes utilizados para frenos, sistemas de embrague y transmisiones se fabrican utilizando técnicas de moldeo por inyección. Además, se prevé que el cambio previsto de componentes de metal a plástico en los vehículos durante el período de pronóstico impulse la demanda. La industria de vehículos eléctricos (VE), valorada actualmente en más de 250 mil millones de dólares, está preparada para una mayor expansión en el período de pronóstico.
Impulsores clave del mercado
La demanda de componentes miniaturizados y complejos impulsa el crecimiento del moldeo por inyección de metales
El mercado mundial de moldeo por inyección de metales (MIM) está impulsado por la creciente demanda de componentes miniaturizados y complejos en varias industrias. A medida que la tecnología avanza y los productos se vuelven más pequeños y complejos, los métodos de fabricación convencionales luchan por cumplir con la precisión y la eficiencia requeridas. MIM proporciona una solución al permitir la producción de piezas complejas con una precisión excepcional, atendiendo a industrias como la electrónica, los dispositivos médicos, la automotriz y la aeroespacial. Esta tendencia hacia la miniaturización es particularmente prominente en la microelectrónica, donde los conectores, sensores e interruptores producidos por MIM juegan un papel vital. Estos componentes deben ser livianos, energéticamente eficientes y ocupar un espacio mínimo. Los fabricantes que buscan alcanzar objetivos de diseño innovadores encuentran atractivo el MIM debido a su capacidad para crear piezas pequeñas y complejas con geometrías intrincadas. Además, sectores como el de la atención médica se benefician de la capacidad del MIM para fabricar componentes médicos finos e intrincados, lo que facilita el desarrollo de instrumentos quirúrgicos mínimamente invasivos y dispositivos implantables. Se espera que este impulsor continúe impulsando la expansión del mercado del MIM a medida que la demanda de componentes avanzados, de alto rendimiento y compactos continúa aumentando.
El creciente énfasis en la sostenibilidad favorece la adopción del moldeo por inyección de metal
El creciente énfasis en la sostenibilidad y la conciencia ambiental está surgiendo como un impulsor significativo en el mercado global del moldeo por inyección de metal (MIM). A medida que las industrias se esfuerzan por minimizar su impacto ecológico y adoptar prácticas más ecológicas, el MIM surge como una alternativa ecológica a los métodos de fabricación convencionales. Los beneficios de sostenibilidad del MIM provienen de varios factores. El proceso generalmente genera menos desechos en comparación con los métodos tradicionales de mecanizado o fundición, ya que produce componentes con una forma casi neta, lo que minimiza la pérdida de material. Además, el MIM puede incorporar materias primas recicladas o secundarias, lo que contribuye a la conservación de recursos y la reducción de residuos. Además, la eficiencia energética del MIM, lograda mediante la producción de piezas complejas en un solo paso, se alinea con el impulso global para la conservación de la energía. Las industrias que buscan adoptar prácticas sostenibles y cumplir con las regulaciones ambientales recurren cada vez más al MIM como una opción de fabricación responsable. Se espera que este impulso gane impulso a medida que las organizaciones de todas las industrias reconozcan las ventajas del MIM en términos de reducción de residuos, eficiencia energética y reducción de la huella de carbono.
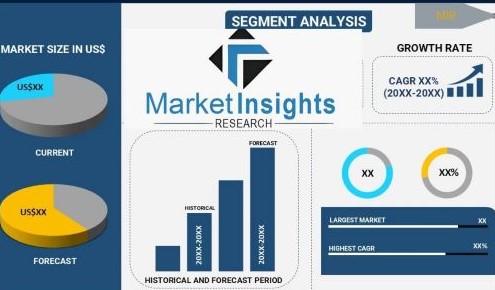
Desafíos clave del mercado
Complejidad de materiales y dilemas de selección en el moldeo por inyección de metales
Un desafío significativo en el mercado global de moldeo por inyección de metales (MIM) radica en la complejidad de la selección de materiales y los dilemas asociados. A diferencia de los métodos de fabricación convencionales que se basan en un conjunto limitado de criterios, el proceso MIM presenta una amplia gama de opciones de materiales, cada una de las cuales posee propiedades mecánicas, térmicas y químicas específicas. Esta diversidad ofrece tanto oportunidades como desafíos. La selección del material adecuado para una aplicación en particular requiere un profundo conocimiento de los requisitos de uso final, incluida la resistencia, la resistencia a la corrosión, la biocompatibilidad y la conductividad eléctrica. Además, el proceso MIM introduce complejidades debido a factores como el comportamiento del polvo, el comportamiento de sinterización y la interacción entre el polvo y el aglutinante. Equilibrar el rendimiento del material con las consideraciones de costo representa otro desafío. Los materiales de primera calidad con propiedades excepcionales pueden tener un costo más alto, lo que puede afectar la rentabilidad general de los componentes producidos mediante MIM. Por el contrario, optar por materiales más rentables podría comprometer el rendimiento o la longevidad del producto final. Para abordar este desafío, los fabricantes deben invertir en pruebas y análisis integrales de materiales y en la colaboración con los proveedores de materiales para lograr el equilibrio óptimo entre rendimiento, costo y capacidad de fabricación. Los avances continuos en la ciencia de los materiales y la disponibilidad de nuevas aleaciones siguen dando forma al panorama, lo que hace que la selección informada de materiales sea un aspecto fundamental para una implementación exitosa de MIM.
Control de calidad y consistencia en la producción de MIM
Garantizar una calidad constante y tolerancias estrictas en la producción de moldeo por inyección de metal (MIM) plantea un desafío significativo para los fabricantes. El proceso MIM implica múltiples pasos, desde la mezcla de la materia prima hasta el moldeo y la sinterización, introduciendo varias variables que afectan las dimensiones, las propiedades mecánicas y la calidad general del producto final. Lograr una contracción uniforme y mitigar defectos como deformaciones, grietas o porosidad requiere un control y monitoreo meticuloso del proceso. La regulación precisa de factores como las características del polvo, la distribución del aglutinante, la eficiencia de desaglomerado y las condiciones de sinterización es fundamental para cumplir con los estrictos estándares de calidad. Además, los componentes MIM a menudo requieren un posprocesamiento para lograr el acabado superficial o los atributos funcionales deseados. Cualquier inconsistencia en estos pasos puede comprometer el rendimiento y la confiabilidad del producto final. Para superar estos desafíos, los fabricantes deben invertir en técnicas avanzadas de monitoreo de procesos, sistemas de control de calidad y personal capacitado capaz de solucionar problemas y optimizar cada etapa del proceso MIM. La implementación sólida de protocolos de garantía de calidad y la adopción de tecnologías de fabricación digital son fundamentales para garantizar la producción de componentes MIM consistentes y de alta calidad.
Tendencias clave del mercado
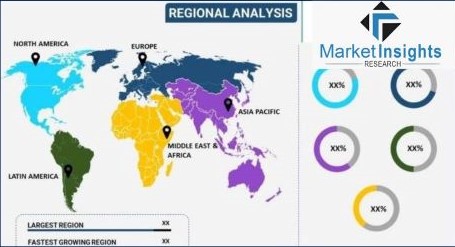
La miniaturización y la geometría compleja impulsan el crecimiento en el moldeo por inyección de metal
El mercado global de moldeo por inyección de metal (MIM) está experimentando actualmente una transformación significativa impulsada por la creciente demanda de componentes geométricos complejos y la tendencia hacia la miniaturización en varias industrias. Este cambio es particularmente prominente en sectores como la electrónica, los dispositivos médicos, la automoción, la industria aeroespacial y los bienes de consumo. A medida que los productos se vuelven más pequeños y más intrincados, los métodos de fabricación tradicionales luchan por cumplir con la precisión y la eficiencia requeridas. En respuesta a este desafío, la MIM ha surgido como una solución viable, ofreciendo la capacidad de producir piezas intrincadas y pequeñas con una precisión excepcional. El proceso de miniaturización permite la creación de dispositivos que no solo son livianos, sino que también son energéticamente eficientes y ahorran espacio. Desde sistemas microelectromecánicos (MEMS) hasta conectores en miniatura, la MIM proporciona los medios para fabricar piezas que antes se consideraban inalcanzables mediante el mecanizado o la fundición convencionales debido a sus geometrías complejas. La capacidad de la MIM para replicar detalles intrincados ha superado los desafíos de fabricación asociados con tales diseños. En consecuencia, ha habido una adopción significativa de la MIM en industrias que requieren componentes compactos y de alto rendimiento. A medida que la tecnología continúa avanzando, se espera que el proceso MIM desempeñe un papel cada vez más fundamental en la conformación del panorama del diseño y la fabricación. Fomentará la innovación y abrirá nuevas posibilidades en el desarrollo de productos, presentando perspectivas emocionantes para el futuro.
Información segmentaria
Información sobre el tipo de material
Se espera que el segmento de acero inoxidable domine el mercado durante el período de pronóstico. Los componentes fabricados con acero inoxidable mediante MIM presentan una combinación única de resistencia a la corrosión, fuerza y versatilidad, lo que los hace adecuados para una amplia gama de aplicaciones. El acero inoxidable MIM se utiliza ampliamente en la producción de componentes de motores, piezas del sistema de combustible, sensores y otros elementos críticos. Además, el acero inoxidable MIM tiene aplicaciones en dispositivos médicos, incluidos instrumentos quirúrgicos, herramientas dentales y componentes implantables, debido a su excepcional resistencia al óxido y la corrosión. Además, el acero inoxidable conserva sus propiedades incluso a temperaturas elevadas, lo que lo hace ideal para aplicaciones de alta temperatura. La creciente demanda de materiales biocompatibles y resistentes a la corrosión en el sector médico ha impulsado significativamente el uso de acero inoxidable en MIM para dispositivos médicos. Además, la creciente tendencia hacia dispositivos más pequeños ha hecho necesario producir componentes intrincados de acero inoxidable mediante MIM. A medida que las industrias continúan buscando un rendimiento superior, el acero inoxidable sigue siendo una opción preferida debido a su notable combinación de fuerza y resistencia a la corrosión.
Perspectivas de la industria de uso final
Se espera que el segmento eléctrico y electrónico domine el mercado durante el período de pronóstico. Los conectores pequeños e intrincados se utilizan habitualmente en dispositivos electrónicos, ordenadores y equipos de telecomunicaciones. Los sensores de precisión desempeñan un papel fundamental en la medición de diversos parámetros en aplicaciones industriales y electrónicas. Además, los componentes como los núcleos de inductores y transformadores son esenciales en los circuitos eléctricos. Con su capacidad para producir formas intrincadas que son difíciles de lograr mediante los métodos de fabricación tradicionales, la tecnología MIM ha ganado una importancia significativa. La creciente demanda de componentes MIM diminutos y complejos está impulsada por la creciente tendencia hacia dispositivos electrónicos más pequeños y ligeros. A medida que los dispositivos se vuelven más sofisticados, la necesidad de componentes intrincados como conectores y sensores sigue aumentando. La transición de la industria automotriz hacia los vehículos eléctricos (VE) y su mayor dependencia del contenido electrónico han abierto nuevas oportunidades para los componentes MIM en este sector. El segmento electrónico y eléctrico del mercado MIM está preparado para un mayor crecimiento debido a la creciente demanda de productos electrónicos en varias industrias. Se prevé que la tendencia actual hacia dispositivos más pequeños y complejos y la necesidad de componentes de alta precisión impulsen la adopción de la tecnología MIM.
Información regional
Se espera que la región de Asia Pacífico domine el mercado durante el período de pronóstico. Países como China, Japón, Corea del Sur y Taiwán han surgido como actores clave tanto en la fabricación como en el desarrollo tecnológico. Con un fuerte crecimiento en industrias como la automotriz, la electrónica y los dispositivos médicos, la región APAC ha sido testigo de un aumento en la demanda de componentes MIM. En particular, las amplias capacidades de fabricación de China y su producción rentable la posicionan como un actor importante en el mercado MIM de APAC. Japón, reconocido por su fabricación de precisión y productos MIM de alta calidad, también hace contribuciones sustanciales. Corea del Sur y Taiwán han demostrado experiencia en electrónica y aplicaciones MIM impulsadas por la tecnología. Dado que la región APAC sirve como centro para las industrias electrónica y automotriz, ambos sectores dependen en gran medida de los componentes MIM. En electrónica, MIM encuentra aplicación en la producción de piezas pequeñas e intrincadas como conectores e interruptores. En el sector automotriz, los componentes MIM se utilizan en piezas de motor, componentes de transmisión y más.
Desarrollos recientes
- Metal Powder Products anunció en agosto de 2021 que había completado con éxito la adquisición de Proform Powdered Metals, con sede en los Estados Unidos. Proform Powdered Metals es reconocida por proporcionar cojinetes, bujes y espaciadores de bronce sinterizado de alta calidad.
- En 2019, Cobra Golf presentó sus innovadores wedges KING MIM, que fueron los primeros en la industria en presentar una construcción de cabeza de acero inoxidable 304 totalmente moldeada por inyección de metal (MIM). La implementación del proceso MIM en cada wedge Cobra representa un avance significativo en la fabricación de wedges, lo que garantiza una forma óptima y una sensación excepcional para una interacción superior con el césped.
- En diciembre de 2021, Argon Medical Devices anunció la adquisición de Matrex Mold and Tool, un fabricante líder de productos moldeados por inyección de precisión con sede en los Estados Unidos. Este movimiento estratégico fortalece aún más el compromiso de Argon Medical Devices de ofrecer productos de alta calidad a sus clientes.
Principales actores del mercado
- ARC Group Worldwide
- Dynacast International
- Phillips-Medisize
- NetShape Technologies
- Smith Metal Productos
- Dean Group International
- CMG Technologies
- Sintex A/S
- Alta tecnología del futuro
- Parmatech Corporation
Por tipo de material | Por uso final Industria | Por región |
|
|
|
Related Reports
- Tamaño del mercado de equipos de construcción autónomos: por producto (equipos de movimiento de tierras y construcci...
- Tamaño del mercado de camiones de construcción: por camiones (volquetes, camiones con remolque, camiones de carga, cam...
- Tamaño del mercado de camiones mineros autónomos: por camiones (volquetes rígidos, volquetes articulados, camiones de...
- Tamaño del mercado de muros cortina de aluminio: por tipo de sistema (sistema construido con varillas, unificado y semi...
- Tamaño del mercado de camiones mineros: por modo de operación (autónomo, manual), por camiones (camiones de acarreo d...
- Tamaño del mercado de camiones grúa: por oferta (camión grúa con pluma de celosía, camión grúa telescópica, cami...
Table of Content
To get a detailed Table of content/ Table of Figures/ Methodology Please contact our sales person at ( chris@marketinsightsresearch.com )
List Tables Figures
To get a detailed Table of content/ Table of Figures/ Methodology Please contact our sales person at ( chris@marketinsightsresearch.com )
FAQ'S
For a single, multi and corporate client license, the report will be available in PDF format. Sample report would be given you in excel format. For more questions please contact:
Within 24 to 48 hrs.
You can contact Sales team (sales@marketinsightsresearch.com) and they will direct you on email
You can order a report by selecting payment methods, which is bank wire or online payment through any Debit/Credit card, Razor pay or PayPal.
Discounts are available.
Hard Copy