Markt für Werkzeugmaschinen – Globale Branchengröße, Anteil, Trends, Chancen und Prognosen, segmentiert nach Werkzeugmaschinentyp (Drehmaschinen, Fräsmaschinen, Bohrmaschinen, Schleifmaschinen, Funkenerosionsmaschinen (EDM), Umformmaschinen (z. B. Abkantpressen, Scheren), Sonstige (z. B. Laserschneidmaschinen, Wasserstrahlschneidmaschinen)), nach Werkzeugmaterial (Werkzeuge aus Schnellarbeitsstahl
Published Date: November - 2024 | Publisher: MIR | No of Pages: 320 | Industry: Infrastructure | Format: Report available in PDF / Excel Format
View Details Buy Now 2890 Download Sample Ask for Discount Request CustomizationPrognosezeitraum | 2024–2028 |
Marktgröße (2022) | 6,03 Milliarden USD |
CAGR (2023–2028) | 6,15 % |
Am schnellsten wachsendes Segment | Hartmetallwerkzeuge |
Größter Markt | Asien-Pazifik |
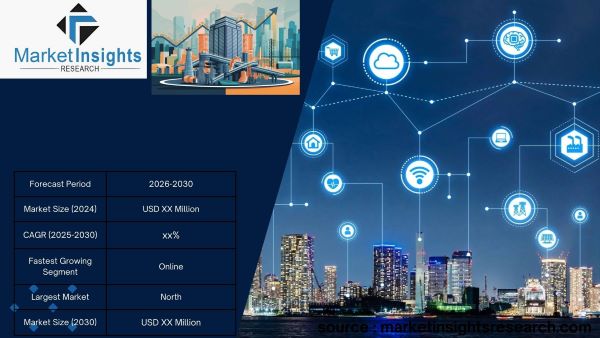
Marktübersicht
Der globale Markt für Werkzeugmaschinen wurde im Jahr 2022 auf 6,03 Milliarden USD geschätzt und wird im Prognosezeitraum voraussichtlich ein robustes Wachstum mit einer durchschnittlichen jährlichen Wachstumsrate von 6,15 % bis 2028 verzeichnen.
Führende Hersteller haben sich mit großen Werkzeugmaschinenanbietern zusammengeschlossen, um ihre Asset-Management-Funktionen digital zu transformieren. Die Lösungen verbessern die abteilungsübergreifende Zusammenarbeit, bieten Situationsbewusstsein durch mobilen Zugriff und erleichtern das Management der Einhaltung gesetzlicher Vorschriften. Die Anbieter entwickeln ihre Lösungen durch Innovationen in Bereichen wie IoT, Cloud und Cybersicherheit weiter. Dies gewährleistet sichere, skalierbare und interoperable Lösungen für vielfältige Anforderungen an Fertigungsanlagen. Laufende Forschung und Entwicklung und die wachsende Akzeptanz datengesteuerter Strategien deuten darauf hin, dass Werkzeugmaschinenlösungen eine zunehmend wichtige Rolle bei der Optimierung von Abläufen und der Entscheidungsfindung unter Unsicherheit spielen werden. Partnerschaften und die Einhaltung neuer Standards werden voraussichtlich die hohe Wachstumsdynamik dieses Marktes aufrechterhalten. Die langfristigen Aussichten für Werkzeugmaschinen bleiben positiv, da Unternehmen den geschäftlichen Wert einer proaktiven Verwaltung von Anlagenleistung und -risiken erkennen.
Wichtige Markttreiber
Fokus auf Verbesserung der Produktivität und Betriebseffizienz
In der heutigen wettbewerbsorientierten Fertigungslandschaft ist die Maximierung von Produktivität und Effizienz entscheidend für den Geschäftserfolg. Werkzeugmaschinen spielen eine Schlüsselrolle, da sie die Optimierung von Produktionsprozessen ermöglichen. Herkömmliche Methoden der manuellen Überwachung und reaktiven Wartung können mit der wachsenden Komplexität und den Produktionszielen nicht Schritt halten.
Lösungen für Werkzeugmaschinen gehen dieses Problem an, indem sie Echtzeiteinblicke in die Leistungsmetriken der Anlagen bieten. Erweiterte Analysen decken Engpässe, Ausfallursachen und Kapazitätsprobleme bei verteilten Anlagen auf. Prädiktive Wartungsmodelle mit Sensorfusion verhindern unerwartete Ausfälle durch automatisierte Zustandsüberwachung. Computer Vision-gestützte Werkzeuge bewerten die Qualität autonom, um Defekte und Nacharbeiten zu minimieren.
Mit verwertbaren Informationen ausgestattet, können Hersteller proaktiv Wartungsarbeiten während geplanter Ausfallzeiten planen. Ferndiagnose und -reparaturen minimieren Störungen. Automatisierte Arbeitsabläufe gewährleisten die Einhaltung von Vorschriften und Sicherheitsbestimmungen, um die Betriebszeit aufrechtzuerhalten. Simulations- und Digital-Twin-Funktionen ermöglichen das virtuelle Testen von Prozessverbesserungen vor der Implementierung.
Dadurch profitieren Hersteller von optimierten Umrüstungen, reduzierten mittleren Reparaturzeiten, höherer Anlagenauslastung, verbesserten First Pass Yields und einer höheren Gesamtanlageneffektivität. Für kapitalintensive Branchen wie die Automobilindustrie führen selbst kleinste Effizienzgewinne zu erheblichen Kosteneinsparungen.
Angesichts des steigenden Produktionsdrucks sind datengesteuerte Tools unverzichtbar geworden, um die Produktivität nachhaltig zu maximieren. Ihre Fähigkeit, Abläufe in großem Maßstab zu rationalisieren, wird die Marktnachfrage erheblich steigern.
Umsetzung von Industrie 4.0-Technologien
Industrie 4.0 hat die Fertigung mit fortschrittlichen Technologien wie IoT, KI, Cloud, Augmented Reality, additiver Fertigung und Robotik verändert. Im Mittelpunkt steht der Bedarf an nahtlos vernetzten Werkzeugen, Maschinen und Systemen, die riesige Mengen an Echtzeitdaten erzeugen.
Werkzeugmaschinenlösungen nutzen diese Technologien, um erweiterte Intelligenz bereitzustellen. Integrierte Sensoren bieten eine digitale 360-Grad-Ansicht der Anlagen für Modelle zur vorausschauenden Wartung und Qualitätssicherung. Cloud-Plattformen bieten skalierbare Datenverarbeitung und Modellhosting. IIoT-Protokolle gewährleisten die Interoperabilität zwischen heterogenen Systemen.
Augmented-Reality-Anwendungen führen Bediener und Techniker durch Handbücher, Arbeitsanweisungen und Reparaturen. Additive Fertigung stellt Ersatzteile auf Anfrage her, um Ausfallzeiten zu minimieren. Kollaborative Roboter verbessern die Produktivität und Sicherheit der Arbeiter.
Da Technologien konvergieren, kann ihr volles Potenzial nur über zentralisierte Plattformen ausgeschöpft werden. Werkzeugmaschinen entwickeln sich zum Rückgrat, um durch datengesteuerte Erkenntnisse und Entscheidungsfindung Wert aus Investitionen in Industrie 4.0 zu ziehen.
Angesichts der steigenden Wettbewerbsfähigkeit sind Hersteller bestrebt, transformative Technologien zu nutzen. Dies positioniert Werkzeugmaschinen stark, um Branchen dabei zu helfen, das Versprechen einer intelligenten, autonomen und nachhaltigen Produktion zu erfüllen. Ihre Fähigkeit, den ROI von Industrie 4.0 zu maximieren, wird ein wichtiger Nachfragetreiber sein.
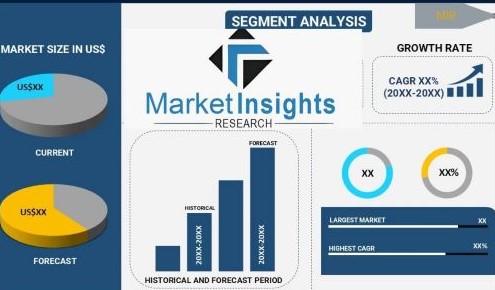
Gewährleistung der Einhaltung sich entwickelnder Standards
Die Fertigungsvorschriften werden weltweit strenger und umfassen Standards in Bezug auf Produktqualität, Umweltauswirkungen, Energieverbrauch, Sicherheit am Arbeitsplatz und mehr. Die Nichteinhaltung kann in großen Volkswirtschaften zu kostspieligen Strafen, Rückrufen oder Verboten führen.
Lösungen für Werkzeugmaschinen tragen dazu bei, dies zu beheben, indem sie Produktionsprozesse, Anlagen und Mitarbeiter kontinuierlich und in Echtzeit auf regulatorische Parameter überwachen. Automatisierte Arbeitsabläufe stellen sicher, dass alle Standards, Zertifizierungen und Best Practices sorgfältig befolgt werden, um die Konformität aufrechtzuerhalten.
Erweiterte Analysen decken subtile Muster auf, um potenzielle Nichtkonformitäten proaktiv zu identifizieren. Simulations- und Szenariotestfunktionen ermöglichen die Validierung der Konformität neuer Prozesse virtuell vor der Bereitstellung. Automatisierte Aufzeichnungen und Prüfpfade vereinfachen den Compliance-Nachweis gegenüber Aufsichtsbehörden und Kunden.
Da sich Standards mit neuen Anforderungen zur Reduzierung des CO2-Fußabdrucks, zu Praktiken der Kreislaufwirtschaft, zur Berichterstattung über Konfliktmineralien usw. schnell weiterentwickeln, wird der Bedarf an einem zentralisierten Compliance-Management zunehmen. Werkzeugmaschinen erweisen sich als ideale Plattform, um diese Komplexität in großem Maßstab zu vereinfachen.
Wichtige Marktherausforderungen
Umschulung der Belegschaft für die Einführung von Industrie 4.0
Der flächendeckende Einsatz moderner Werkzeugmaschinen erfordert neue Fähigkeiten von Fabrikarbeitern und Technikern. Traditionelle Fähigkeiten, die sich auf die manuelle Bedienung und Fehlerbehebung von Geräten konzentrieren, müssen nun auf Bereiche wie KI, Big Data, Cloud, Cybersicherheit, Robotik und mehr übertragen werden.
Die Umschulung großer bestehender Belegschaften ist jedoch eine Herausforderung. Aufgrund ihres Alters, ihres Bildungshintergrunds oder der Geschwindigkeit der Veränderungen sind möglicherweise nicht alle Arbeitnehmer bereit oder in der Lage, neue Technologien anzunehmen. Umschulungsprogramme erfordern erhebliche Investitionen und Betriebsunterbrechungen, die sich viele kleine Hersteller nicht leisten können.
Selbst wenn Schulungen angeboten werden, dauert es lange, neues Wissen in reale Anwendungen zu übertragen. Ohne Anleitung fällt es den Mitarbeitern möglicherweise schwer, datengesteuerte Erkenntnisse zu kontextualisieren oder Augmented-Reality-/Virtual-Reality-Tools sicher zu nutzen.
Hersteller von Werkzeugmaschinen müssen eng mit Bildungseinrichtungen zusammenarbeiten, um standardisierte Lehrpläne für Industrie 4.0-Rollen zu entwickeln. Zertifizierungsprogramme können das Kompetenzniveau bestätigen. Kunden müssen außerdem eine Kultur des kontinuierlichen Lernens durch praktische Projekte und Mentoring fördern.
Wenn die Qualifikationslücke nicht proaktiv geschlossen wird, werden Hersteller das volle Potenzial ihrer Investitionen in Werkzeugmaschinen nicht ausschöpfen. Veraltete Fähigkeiten können die Akzeptanz, Produktivitätssteigerungen und die langfristige Wettbewerbsfähigkeit beeinträchtigen. Umschulung bleibt eine große organisatorische Herausforderung.
Integration älterer Infrastrukturen
Die meisten Hersteller betreiben heterogene Infrastrukturlandschaften mit älteren Maschinen, speicherprogrammierbaren Steuerungen (SPS) und SCADA-Systemen aus verschiedenen Epochen. Die nahtlose Integration von Werkzeugen in bestehende Systeme erfordert erheblichen Aufwand.
Altmaschinen verfügen häufig nicht über integrierte Sensoren zur Zustandsüberwachung. Ihre Nachrüstung bringt zusätzliche Kosten und Produktionsunterbrechungen mit sich. Protokolle und Schnittstellen unterscheiden sich zudem zwischen SPS, Historian und anderen Steuerungssystemen. Die Datenintegration über Silos hinweg ist aufgrund struktureller und semantischer Inkonsistenzen eine Herausforderung.
Sicherheitslücken entstehen auch durch Netzwerklücken während der Integration. Die Einhaltung gesetzlicher Vorschriften muss erneut validiert werden. Kompatibilitäts- und Leistungstests wirken sich auf Produktionsabläufe aus.
Wenn Altanlagen nicht umsichtig aufgerüstet oder ausgemustert werden, können Werkzeugmaschinen für kapitalintensive Branchen möglicherweise nicht den versprochenen Wert liefern. Standardisierung durch IIoT-Protokolle und Edge Computing kann helfen, aber die vollständige Integration wird ein langer Weg bleiben. Dies wirkt abschreckend auf kleinere Hersteller mit begrenzten Modernisierungsbudgets.
Anbieter müssen optimierte Lösungen, Beratungsdienste und Finanzierungsoptionen anbieten, um Kunden dabei zu helfen, diese Infrastrukturherausforderungen reibungslos zu meistern. Andernfalls werden Altlasten das Wachstumspotenzial des Marktes weiterhin einschränken.
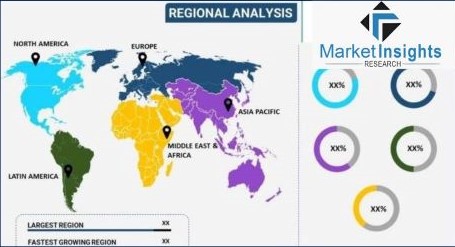
Wichtige Markttrends
Aufstieg ergebnisorientierter Preismodelle
Traditionell wurden Werkzeugmaschinenlösungen an Hersteller mit hohen Lizenzgebühren im Voraus und zusätzlichen Kosten für Anpassungen, Schulungen, Implementierung und laufenden Support verkauft. Während dieses Preismodell großen Unternehmen mit eigenen IT-Teams zur Verwaltung von On-Premise-Bereitstellungen Flexibilität bot, beschränkte es den Zugang für viele kleine und mittlere Hersteller mit begrenzten IT-Budgets und -Ressourcen.
Da der Markt für Werkzeugmaschinen jedoch immer wettbewerbsintensiver wird, erkennen die Anbieter die Notwendigkeit, ihre Lösungen einem breiteren Kundenstamm zugänglich zu machen, einschließlich flexibler Produktionsumgebungen mit geringem Volumen. Sie übernehmen zunehmend mengen- oder ergebnisorientierte Preismodelle, die auf konkrete Geschäftsergebnisse ausgerichtet sind, die die Kunden erzielen. Anstatt hohe einmalige Gebühren zu zahlen, zahlen Kunden auf der Grundlage messbarer Kennzahlen wie erhöhtes Produktionsvolumen, reduzierter Energieverbrauch, höhere Produktqualität, längere Betriebszeiten der Geräte, weniger Ausfälle und andere Vorteile, die mithilfe von Werkzeugmaschinenlösungen erzielt werden.
Dieses leistungsorientierte Modell senkt die Vorlaufkosten und finanziellen Risiken für Kunden. Es beseitigt auch Hindernisse, die kleine Hersteller davon abgehalten haben, fortschrittliche Werkzeuge einzuführen. Gleichzeitig werden Anbieter durch ergebnisorientierte Preise dazu angeregt, sicherzustellen, dass ihre Lösungen für die einzigartigen Prozesse, Arbeitsabläufe und Infrastrukturen jeder Kundenbereitstellung optimiert sind. Dies führt zu einem partizipativen Engagement zwischen Anbietern und Kunden während der gesamten Implementierung und Nutzung der Lösungen. Da im Laufe der Zeit mehr Betriebs- und Produktivitätsergebnisdaten aus Live-Bereitstellungen gesammelt werden, können die Preise automatisch auf der Grundlage nachgewiesener Leistungsniveaus angepasst werden.
Dieses für alle Seiten vorteilhafte, nutzungsbasierte Geschäftsmodell wird voraussichtlich das Wachstum des gesamten Werkzeugmaschinenmarktes beschleunigen, indem es die Möglichkeiten von Industrie 4.0 für mehr kleine und mittlere Unternehmen finanziell erschwinglich macht. Darüber hinaus bietet es Anbietern einen zuverlässigeren, wiederkehrenden Einnahmestrom im Vergleich zu einmaligen Lizenzgebühren. Ergebnisbasierte Preisgestaltung entwickelt sich daher zu einem beliebten neuen Preisparadigma in der Werkzeugmaschinenindustrie.
Aufstieg der KI-gestützten vorausschauenden Wartung
Eine Schlüsselfunktion, die das Wachstum von Werkzeugmaschinenlösungen vorantreibt, ist die vorausschauende Wartung, die auf künstlicher Intelligenz und Algorithmen des maschinellen Lernens basiert. Diese Algorithmen erfordern riesige Datensätze mit zeitreihenbasierten Sensormessungen, Prozessparametern, Maschinenprotokollen, Ausfallzeitaufzeichnungen und anderen Betriebsdaten, die über lange Zeiträume unter unterschiedlichen Bedingungen von Maschinenflotten gesammelt wurden. Diese Fülle an historischen Ausfall- und Leistungsdaten ermöglicht es den Algorithmen, subtile Muster und Korrelationen zu erkennen, die Menschen möglicherweise übersehen, um potenzielle Probleme genau vorherzusagen, lange bevor sie die Produktionsabläufe beeinträchtigen.
Für die meisten kleinen Hersteller ist es jedoch nicht machbar, derart große Ausfall- und Betriebsdatensätze von einzelnen Maschinen unter ihrer Kontrolle zu sammeln. Hier erweisen sich in der Cloud gehostete Modelle des maschinellen Lernens, die mit aggregierten anonymen Daten aus einer breiten Palette vernetzter Industrieanlagen trainiert wurden, als wertvoll. Anbieter nutzen gemeinsam genutzte Datensätze mit Gerätenutzungsmustern von Tausenden von Kunden weltweit, um die Vorhersagegenauigkeit ihrer KI/ML-Modelle kontinuierlich zu verbessern. Modelle, die anhand gepoolter Daten von einer Vielzahl von Maschinen in unterschiedlichen Branchen und Regionen trainiert werden, können subtile Anzeichen von Geräteverschleiß erkennen, die Einzelkundenmodellen möglicherweise entgehen.
Moderne Lösungen für Werkzeugmaschinen analysieren jetzt die hochfrequenten mehrdimensionalen Sensorströme, Prozessparameter, Maschinenprotokolle und andere Betriebsdaten mithilfe dieser in der Cloud trainierten Modelle. Sie können Anomalien erkennen, die auf drohende Komponentenfehler, Prozessabweichungen oder Maschinenausfälle hinweisen, und zwar Tage oder sogar Wochen im Voraus. Solche langfristigen Vorhersagen helfen dem Wartungspersonal, Just-in-Time-Reparaturen zu planen, ohne die Produktionspläne zu stören. Augmented- und Virtual-Reality-Tools unterstützen die Fernfehlerbehebung und Anleitung von Technikern vor Ort zusätzlich. Over-the-Air-Updates tragen auch dazu bei, die Maschinenleistung vor Ort kontinuierlich zu optimieren. Da KI-Modelle im Laufe der Zeit mit mehr Daten ausgereifter werden, werden sie die Effizienz, den Ertrag und die Betriebszeit der Geräte durch automatisierte Prozesskorrekturen, zustandsbasierte Wartungsroutinen und autonome Problemlösung aus der Ferne steigern. Vorausschauende Wartung auf Basis von Cloud-basierter KI ist daher ein wichtiger Treiber der Werkzeugmaschinenindustrie.
Anpassung durch offene Ökosysteme und App-Händler
Während standardisierte Werkzeugmaschinenlösungen einen guten Ausgangspunkt für die Digitalisierung von Fertigungsabläufen bieten, kann kein einzelner Anbieter alle einzigartigen und sich entwickelnden Anforderungen der speziellen Produktionsumgebung, der vorhandenen Infrastruktur und der strategischen Ziele jedes Kunden erfüllen. Punktlösungen fehlt oft die Flexibilität, die für eine individuelle Integration und Erweiterung erforderlich ist. Gleichzeitig hindern die hohen Kosten für den Aufbau vollständig angepasster Systeme von Grund auf viele Hersteller daran, den maximalen Nutzen aus ihren Investitionen zu ziehen.
Um diese Herausforderungen zu bewältigen, setzen Werkzeugmaschinenanbieter jetzt auf offene Ökosysteme und Partnernetzwerke. Sie bieten Herstellern Zugang zu App-Händlern und Marktplätzen mit einer wachsenden Sammlung spezialisierter, aber interoperabler Zusatzlösungen, die auf die nahtlose Zusammenarbeit mit ihren Basisplattformen geprüft wurden. Kunden können frei aus den besten Komponenten verschiedener unabhängiger Anbieter wählen, um Konfigurationen zusammenzustellen, die auf ihre spezifischen Anforderungen zugeschnitten sind. Modulare Produktarchitekturen vereinfachen außerdem die Integration dieser ergänzenden Tools und Datenquellen ohne störende Upgrades.
Standardisierte APIs und Entwicklerkits ermöglichen es Kunden zusätzlich, Schnittstellen anzupassen, proprietäre Anwendungen unter Nutzung von Werkzeugmaschinendaten zu erstellen oder Systemintegratoren mit komplexen, maßgeschneiderten Anforderungen zu beauftragen. Ein offener Ansatz, der auf Interoperabilitätsstandards basiert, ersetzt proprietäre Lock-ins und ermöglicht es Werkzeugmaschinen, als Integrations-Backbone für verschiedene erstklassige Lösungen zu fungieren.
Dieser Wandel hin zu offenen und anpassbaren Architekturen dürfte die Akzeptanzraten beschleunigen. Er bietet Herstellern eine beispiellose Flexibilität, ihre Bereitstellungen rund um einen modularen Kern zu optimieren und gleichzeitig spezialisierte Lösungen hinzuzufügen, wenn sich ihre Fertigungsanforderungen und -strategien im Laufe der Zeit weiterentwickeln. Anbieter profitieren außerdem von einem erweiterten Ökosystem von Partnern, das den Gesamtwert ihrer Angebote steigert. Offenheit wird ein bestimmender Trend sein, der die Werkzeugmaschinenlandschaft prägt.
Segmentelle Einblicke
Einblicke in die Art der Werkzeugmaschinen
Drehmaschinen dominierten 2022 den globalen Werkzeugmaschinenmarkt und machten über 30 % des gesamten Umsatzanteils aus. Drehen ist ein Materialentfernungsprozess, bei dem mit einem einschneidigen Schneidwerkzeug unerwünschtes Material von einem rotierenden Werkstück entfernt wird, um ein rotationssymmetrisches Objekt mit guter Oberflächengüte zu erzeugen. Es ist nach wie vor das branchenübergreifend am weitesten verbreitete Bearbeitungsverfahren zur Herstellung zylindrischer und anderer rotationssymmetrischer Teile.
Drehmaschinen sind vielseitig und können eine Vielzahl von Komponenten von einfachen bis hin zu komplexen Geometrien in großen Stückzahlen herstellen. Sie werden häufig in der Automobil-, Luft- und Raumfahrt-, Medizingeräte- und anderen Fertigungssektoren zur Herstellung von Wellen, Zylindern, Buchsen, Zahnrädern und anderen Rotationsteilen verwendet. Die geringen Rüstzeiten und hohen Produktionsraten, die durch Drehmaschinen erreicht werden, machen sie sehr gut für Massenproduktionsumgebungen geeignet. Darüber hinaus führt die Verfügbarkeit einer breiten Palette fortschrittlicher Drehzentren mit Multitasking-Funktionen, automatischen Werkzeugwechslern und integrierten Messsystemen zu einer zunehmenden Akzeptanz. Die wachsende Nachfrage nach gedrehten Komponenten aus expandierenden Endverbrauchsbranchen sowie die Notwendigkeit zur Steigerung der Produktivität werden voraussichtlich die Dominanz der Drehmaschinen im Prognosezeitraum aufrechterhalten.
Einblicke in Werkzeugmaterialien
Hartmetallwerkzeuge dominierten 2022 den globalen Werkzeugmaschinenmarkt nach Werkzeugmaterial und machten über 40 % des Gesamtumsatzes aus. Hartmetallwerkzeuge werden aus Wolframkarbid hergestellt, einem der härtesten Materialien für Schneidwerkzeuge. Sie bieten im Vergleich zu anderen Werkzeugmaterialien wie Schnellarbeitsstahl eine hohe Verschleißfestigkeit, Festigkeit und Härte.
Hartmetallwerkzeuge können eine Vielzahl von Metallen und Nichtmetallen bei hohen Geschwindigkeiten und Vorschüben bearbeiten. Sie behalten ihre scharfe Schneide lange Zeit und bieten selbst bei unterbrochenen Schnitten eine bessere Oberflächengüte. Daher können Hartmetallwerkzeuge hohe Materialabtragsraten und Produktivitätsniveaus erreichen. Ihre Fähigkeit, mit höheren Schnittgeschwindigkeiten zu bearbeiten, führt auch zu kürzeren Zykluszeiten. Darüber hinaus müssen Hartmetallwerkzeuge im Vergleich zu anderen Werkzeugmaterialien nicht häufig nachbearbeitet oder geschärft werden. Dies senkt die Werkzeugkosten und Ausfallzeiten für die Bediener. Die zunehmende Komplexität der bearbeiteten Komponenten und der Bedarf an engeren Toleranzen treiben die Nachfrage nach Hartmetallwerkzeugen in Branchen wie der Automobil-, Luft- und Raumfahrt- und Werkzeug-/Formenherstellung weiter an. Aufgrund ihrer überlegenen Leistung und Kostenvorteile gegenüber Alternativen werden Hartmetallwerkzeuge den Markt für Werkzeugmaschinen im Prognosezeitraum voraussichtlich weiterhin dominieren...
Regionale Einblicke
Der asiatisch-pazifische Raum dominierte 2022 den globalen Markt für Werkzeugmaschinen und machte über 40 % des Gesamtumsatzes aus. China, Japan, Indien, Südkorea und andere Entwicklungsländer tragen maßgeblich zum großen Anteil der Region bei.
Der asiatisch-pazifische Raum hat sich zum weltweit größten Produktionszentrum entwickelt, angetrieben durch starkes Wachstum in Branchen wie Automobil, Elektronik, Maschinenbau und Schwermaschinen. Die Region beherbergt eine große Anzahl von Werkzeugmaschinen-OEMs sowie Endverbrauchsindustrien mit enormen Produktionskapazitäten. In den letzten Jahren hat sie eine schnelle Industrialisierung und hohe Kapitalinvestitionen in fortschrittliche Produktionsanlagen erlebt. Darüber hinaus fördern staatliche Initiativen zur Förderung von „Make in India“ und „Made in China 2025“ die lokale Produktion und Importsubstitution.
Der große Fertigungssektor und die zunehmende Einführung industrieller Automatisierung im asiatisch-pazifischen Raum haben die Nachfrage nach Werkzeugmaschinen angekurbelt. Die Verfügbarkeit von qualifizierten Arbeitskräften zu niedrigen Kosten und die Nähe zu Endverbrauchsmärkten verschaffen der Region einen Wettbewerbsvorteil gegenüber anderen Regionen. Darüber hinaus erweitern Werkzeugmaschinenhersteller ihre Präsenz in Asien, um der wachsenden lokalen Nachfrage gerecht zu werden. Dies sowie steigende Investitionen in Industrie 4.0-Technologien deuten darauf hin, dass der asiatisch-pazifische Raum im Prognosezeitraum auf dem globalen Werkzeugmaschinenmarkt weiterhin dominieren wird.
Jüngste Entwicklungen
- Im Juni 2022 kündigte Doosan MachineTools die Erweiterung seiner Produktionsstätte in Indien an. Das neue Werk wird sich auf die Herstellung von CNC-Drehmaschinen und Bearbeitungszentren konzentrieren, um die wachsende Nachfrage der heimischen Automobil- und Maschinenbaubranche zu bedienen.
- Im Mai 2022 erwarb DMG Mori eine Mehrheitsbeteiligung an Metalcraft Engineering, einem Hersteller von CNC-Drehmaschinen. Dadurch erweitert DMG Mori sein Produktportfolio und seine Präsenz auf dem indischen Markt.
- Im April 2022 brachte Yamazaki Mazak das Multitasking-Drehzentrum QUICK TURN SMART 250SY auf den Markt. Es verfügt über ein kompaktes Design für die Kleinserienproduktion und integrierte KI-basierte Funktionen zur automatischen Bearbeitungsoptimierung.
- Im März 2022 eröffnete AMADA ein neues technisches Schulungszentrum in Michigan, USA, um Kunden weiterzubilden und Initiativen zur digitalen Transformation zu unterstützen. Das Zentrum wird praktische Schulungen zu Blechbearbeitungstechnologien anbieten.
- Im Februar 2022 erweiterte Okuma America seine Präsenz durch die Übernahme von Cincinnati Inc., einem Anbieter von Werkzeugmaschinen, Automatisierungs- und additiven Fertigungslösungen.
- Im Januar 2022 brachte Komatsu sein neues GRACE-Zellenproduktionssystem mit autonom gesteuerten Fahrzeugen und integrierter KI-basierter Qualitätsprüfung auf den Markt.
- Im Dezember 2021, Hyundai WIA hat den deutschen Werkzeugmaschinenhersteller DMG Mori übernommen, um Zugang zu fortschrittlichen Fertigungstechnologien zu erhalten.
- Im November 2021 brachte Makino neue 5-Achsen-Vertikalbearbeitungszentren mit integrierten automatischen Werkzeugwechslern und erweiterten Arbeitsbereichen auf den Markt.
Wichtige Marktteilnehmer
- AMADA HOLDINGS CO., LTD.
- DMG MORI CO., LTD.
- TRUMPF GROUP
- JTEKT Corporation
- Komatsu Ltd
- Okuma Corporation
- DoosanMachine Tools Co., Ltd
- Makino Milling Machine Co., Ltd
- HYUNDAI WIA CORP
- CHIRON Group SE
Nach Werkzeugmaschinentyp | Nach Werkzeug Material | Nach Endbenutzer | Nach Region |
|
|
|
|
Related Reports
- Marktgröße für Auslegerkräne – nach Produkt (Wandmontage, Säulenmontage), nach Tragfähigkeit (leichte, mittlere ...
- Marktgröße für Metallschneidwerkzeuge – nach Werkzeug (Wendeschneid- und Vollwerkzeug), nach Verfahren (Fräsen, Bo...
- Marktgröße für stationäre Kräne – nach Produkt (Turmdrehkran, Portalkran, Stiffleg-Kran, Einschienenbahnkran), na...
- Marktgröße für modulare und vorgefertigte Bauten – nach Produkttyp (permanent und verschiebbar), nach Material (Sta...
- Marktgröße für Lasermessgeräte – nach Produkttyp (Handgerät, Innenbereich, Außenbereich), nach Anwendung (Bauwes...
- Marktgröße für Holz-Kunststoff-Verbundböden – nach Produkt (Polyethylen, Polypropylen, Polyvinylchlorid), nach Dic...
Table of Content
To get a detailed Table of content/ Table of Figures/ Methodology Please contact our sales person at ( chris@marketinsightsresearch.com )
List Tables Figures
To get a detailed Table of content/ Table of Figures/ Methodology Please contact our sales person at ( chris@marketinsightsresearch.com )
FAQ'S
For a single, multi and corporate client license, the report will be available in PDF format. Sample report would be given you in excel format. For more questions please contact:
Within 24 to 48 hrs.
You can contact Sales team (sales@marketinsightsresearch.com) and they will direct you on email
You can order a report by selecting payment methods, which is bank wire or online payment through any Debit/Credit card, Razor pay or PayPal.
Discounts are available.
Hard Copy